Industrielle Prozessleitsysteme
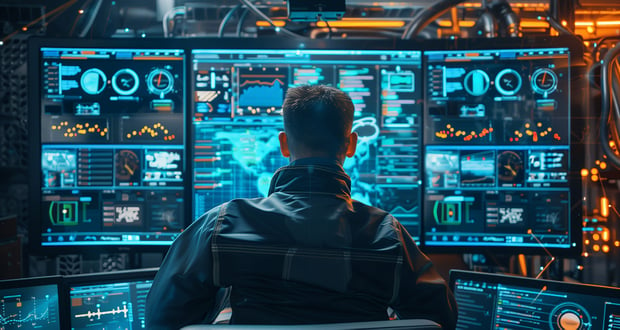
Als integraler Bestandteil vieler Betriebe ermöglicht ein industrielles Prozessleitsystem die automatisierte standortübergreifende Steuerung zahlreicher Komponenten. Industrielle Prozessleitsysteme sind in verschiedenen Ausführungen erhältlich und unterstützen eine Vielzahl von Anwendungen in Branchen wie der Energiewirtschaft, der Fertigungs- oder Life Sciences Industrie. Sie bieten viele Vorteile rund um Effizienz, Qualität, Analyse und beeinflussen Ihr wirtschaftliches Endergebnis positiv.
Werfen wir nun einen genaueren Blick auf industrielle Prozessleitsysteme und ihre Möglichkeiten.
Was ist ein industrielles Prozessleitsystem?
Mit industriellen Prozessleitsystemen werden verschiedene Komponenten wie Überwachungsgeräte und Softwaresysteme verwaltet, um industrielle Abläufe zu steuern und so weit wie möglich zu automatisieren. Sie schaffen das nötige Gleichgewicht zwischen den zahlreichen für den Betrieb einer industriellen Infrastruktur erforderlichen Komponenten und sorgen dafür, dass diese effizient und synchron ineinandergreifen. Ein industrielles Prozessleitsystem kann entweder vollständig die Kontrolle übernehmen oder Teil einer Hybridlösung sein, die auch menschliche Interaktionen beinhaltet. Es sind Open-Loop-, Closed-Loop- sowie manuelle Optionen erhältlich.
Wenn Ihr Unternehmen das Industrial Internet of Things (IIoT) und moderne Technologien nutzt, ist ein industrielles Prozessleitsystem besonders hilfreich und minimiert zudem mögliche Sicherheitsrisiken. Insgesamt bieten industrielle Prozessleitsysteme mehr Transparenz und eine benutzerfreundlichere Möglichkeit zur Steuerung eines komplizierten Netzwerks von Komponenten. Zu den Elementen eines industriellen Prozessleitsystems zählen unter anderem folgende Server und Steuerungen:
- Remote Terminal Unit (RTU): Ein RTU ist ein Feldgerät, das mit einem Master Terminal Unit kommuniziert und die Funktion einer übergeordneten Steuerung hat. Vordefinierte Funktionen und intuitive Parametrierung mittels Webinterface ermöglichen auch Benutzern ohne Programmierkenntnisse eine einfache Bedienung.
- Mensch-Maschine-Schnittstelle (HMI): Über eine HMI können Menschen mit der Hardware interagieren, die eine Maschine steuert. Anwender können aktuelle Status anzeigen, Sollwerte überwachen, Sicherheitswarnungen erhalten, Parameter und Algorithmen anpassen, historische Daten auswerten und vieles mehr.
- Speicherprogrammierbare Steuerung (SPS): Als eine der Steuerungen eines industriellen Prozessleitsystems ermöglicht die SPS lokales Prozessmanagement bzw. die Anbindung an eine HMI. Darüber hinaus gibt es sogenannte Programmable Automation Controller (PAC), die in ihrer Funktion den SPSen ähneln, aber oftmals komplexer sind und mehr Speicher und Programmierflexibilität sowie zusätzliche Funktionen bieten.
- Soft-SPS: SPSen finden sich gelegentlich auch in zentralen Datenbanken, die mit Daten aus der Fertigungsstraße gespeist werden. zenon Logic bietet zum Beispiel eine integrierte SPS-Umgebung, auf die Anwender über eine gemeinsame Datenbank zugreifen können. Dabei müssen Objekte nur einmal erstellt werden und lassen sich dann beliebig oft im System abrufen.
- Steuerserver: Dieser Server hostet die Supervisory Control Software für eine SPS oder ein Distributed Control System (DCS). Er kann außerdem mit untergeordneten Steuergeräten kommunizieren.
- IT und Betriebstechnologie: Verschiedene Geräte wie Sensoren überwachen die Vorgänge im Feldbetrieb.
- Regelkreis: Ein Regelkreis besteht aus verschiedenen Arten von Hardware wie SPSen und Aktoren, die Sensorsignale, Schalter, Schutzschalter, Steuerventile und mehr auswerten. Diese Informationen werden anschließend an eine Steuerung übermittelt, um eine bestimmte Aufgabe auszuführen.
- Fernwartungssystem: Dieses System kann Unregelmäßigkeiten oder Ausfälle überwachen und erkennen, und gegebenenfalls sogar Maßnahmen ergreifen, um Probleme zu verhindern.
- Master Terminal Unit (MTU) oder SCADA-Server: Das MTU oder der (SCADA)-Server (Supervisory Control and Data Acquisition Server) kann im Feldbetrieb Befehle an die RTUs übermitteln.
- Intelligente elektronische Geräte: Ein Smart Device kann in erster Linie Daten sammeln und mit anderen Geräten kommunizieren. Mit einer SCADA- und DCS-Infrastruktur können diese Geräte auch automatisch lokale Kontrollen durchführen.
- Archivserver: Die vom industriellen Prozessleitsystem und seiner Betriebsumgebung gesammelten Daten werden auf einem Archivserver gespeichert. Von dort aus lassen sie sich in andere Informationssysteme exportieren, wo sie dann zur weiteren Auswertung und strategischen Planung verarbeitet werden können.
Die Vorteile eines industriellen Prozessleitsystems
Die Industrieautomatisierung über ein industrielles Prozessleitsystem bietet eine Reihe wichtiger Vorteile, auf die wir im Folgenden näher eingehen.
-
Durch den geringeren manuellen Aufwand und die höhere Produktivität trägt ein Leitsystem für industrielle Prozesse unmittelbar zur Effizienzsteigerung bei. Neben manuellen Aufgaben lässt sich so auch der Energieverbrauch deutlich senken. Da ein industrielles Prozessleitsystem immer verfügbar ist, können Sie die Automatisierungsfunktionen im Rund-um-die-Uhr-Betrieb verwenden. Alternativ können Stillstände effektiv für die Informationsverarbeitung und -analyse genutzt werden, um Ihre Anlagen im Betrieb optimal auszulasten.
-
Durch die Senkung Ihrer Kosten nimmt der Spielraum für höhere Gewinne zu. Wenn Sie Ihren Durchsatz steigern und verbessern, können Sie Ihre Gewinnspannen erhöhen, die Personalanforderungen vereinfachen und die Kosten für den Betrieb senken.
-
Die mit einem industriellen Prozessleitsystem optimierten Prozesse helfen, die für die Produktfertigung erforderlichen Ressourcen zu minimieren, und tragen zu einer effizienteren Verwaltung bei. Je weniger verschwendet wird, desto weniger Zeit müssen Sie für die Abfallsortierung aufwenden. Beschaffungskosten für das Material, das den Abfall überhaupt erst verursacht hat, werden reduziert. Wenn weniger Fehler gemacht werden, sinkt auch der Aufwand für die Problembehebung bzw. die Schadensbegrenzung beim Kunden.
-
Ein industrielles Prozessleitsystem trägt in vielerlei Hinsicht zur Produktqualität bei, beispielsweise indem es die Qualität überwacht oder Prozesse bei Bedarf anpasst. Darüber hinaus können mit der industriellen Prozessautomatisierung auch menschliche Fehler minimiert und durch Analysen wertvolle Erkenntnisse über das Produkt gewonnen werden. Mit allen Funktionen eines industriellen Prozessleitsystems können Sie die Produktqualität erheblich steigern. Zudem profitieren Sie von einer höheren Kundenzufriedenheit und einer dadurch bedingten verbesserten Reputation.
-
In Ihrer Industrieanlage fallen umfangreiche Datenmengen an - unabhängig davon, ob Sie bereits ein industrielles Prozessleitsystem haben oder nicht. Ein Leitsystem für industrielle Prozesse kann alle diese Daten erfassen und organisieren und einen zentralen Ort für eine einfachere Analyse und Kontrolle schaffen. Zudem verbindet es alle Systeme, Sensoren und Komponenten der Anlage miteinander und ermöglicht so umfassende Transparenz und Kontrolle von oben nach unten.
In der Industrie bietet Automatisierung ein enormes Potenzial, das immer mehr Unternehmen nutzen, um ihre Wettbewerbsfähigkeit zu erhalten. Insgesamt dürfte der Markt mit einer durchschnittlichen jährlichen Wachstumsrate von 8,9 % weiter zulegen und bis 2028 einen Wert von 288,93 Milliarden US-Dollar erreichen.
Welche Arten von industriellen Prozessleitsystemen gibt es?
Industrielle Prozessleitsysteme sind in verschiedenen Varianten erhältlich, die jeweils für unterschiedliche Umgebungen vorgesehen sind. Nachfolgend werden die verschiedenen Arten von Leitsystemen vorgestellt.
SCADA
Ein SCADA-System (SCADA = Supervisory Control and Data Acquisition) erfasst Daten von den verschiedenen Anlagen eines Betriebs und kann diese standortübergreifend steuern. Diese Steuerung erfolgt auf Überwachungsebene, wobei SPSen, RTUs und entsprechende Module an verschiedenen Standorten eingesetzt werden, um die Daten zu sammeln und über große Entfernungen zu übertragen. Sie können mit Maschinen, Sensoren oder anderen Anlagentypen verbunden sein. Dabei übermitteln integrierte HMIs die Daten und Menschen überwachen die eingehenden Informationen – ein Prozess, der vor Ort oder aus der Ferne stattfinden und zahlreiche Ein- und Ausgänge umfassen kann.
SCADA-Systeme können einfach, aber auch sehr komplex aufgebaut sein. Besonders verbreitet sind sie in Branchen wie der Energieübertragung und -verteilung, der Lebensmittel- und Getränkeindustrie, dem Pharmasektor und der Automobilindustrie. Ein SCADA-Leitsystem basiert im Wesentlichen auf einer leistungsfähigen HMI-Plattform und profitiert so von einer benutzerfreundlichen Schnittstelle und umfangreichen Funktionen, die die Datenerfassung, Sichtbarkeit und Effizienz erleichtern.
DCS
Ein Distributed Control System (DCS) kommt an einem Standort zum Einsatz und arbeitet mit Sollwerten, bei denen es sich um die Zielwerte für eine Variable oder einen Prozess handelt. Das System übermittelt einen Sollwert an eine Steuerung, die Komponenten wie Ventile und Aktoren bewegen kann, um den gewünschten Sollwert zu halten. Ein DCS nutzt einen zentralen Überwachungsregelkreis, um die Geräte als Teil des Produktionsprozesses zu verwalten. Dabei steuert, überwacht und organisiert es die vielen in einer Anlage eingesetzten Steuerungen.
Mit einem DCS erhalten die Anwender schnellen Zugriff auf alle erforderlichen Daten. Da viele Geräte mit diesem System verbunden sind, minimiert es auch die Auswirkungen einzelner Fehler auf das gesamte industrielle Prozessleitsystem. Ein DCS-Leitsystem ist eine beliebte Wahl für Unternehmen in den Bereichen Fertigung, Ölraffination, Energieerzeugung und -verteilung sowie Wasser und Abwasser.
SPS
Obwohl speicherprogrammierbare Steuerungen (SPS) ein wichtiger Bestandteil der beiden oben genannten Methoden sind, können sie technisch gesehen auch eigenständig betrieben werden. SPSen erfassen im Grunde Informationen von einem Eingang, verarbeiten die Daten und lösen basierend auf den jeweiligen Parametern Ausgaben aus. Sie können einfach bis sehr komplex aufgebaut sein.
Viele SPSen verfügen über integrierte Komponenten, können aber auch modular an Geräte wie Sensoren, Zähler, Leuchten, Relais und Ventile angeschlossen werden. Weitere integrierte oder modulare Komponenten können beispielsweise die Stromversorgung sowie Anschlüsse und Protokolle für die Kommunikation mit SCADA- oder HMI-Systemen sein.
SPSen sind in Branchen wie Vertrieb und Fertigung, einschließlich Serienfertigung, weit verbreitet und können an einem oder mehreren Standorten eingesetzt werden. Der Hauptnachteil beim Einsatz von SPSen ohne übergeordnetes System wie DCS oder SCADA ist, dass es keine zentrale Sichtbarkeit und Kontrolle gibt. SPS-Leitsysteme arbeiten lokal und kommunizieren selbst nicht mit anderen Systemen, was konkret bedeutet: Je größer ein Unternehmen wird, desto weniger lohnt sich ein rein SPS-basierter Ansatz. Trotzdem sind sie ein wichtiges Element industrieller Prozessleitsysteme, da sie einen Großteil der Funktionalität dieser Systeme bieten.
Wie wird ein industrielles Prozessleitsystem eingerichtet und genutzt?
Wenn Sie ein Projekt mit einem industriellen Prozessleitsystem beginnen, profitieren Sie später von mehr Kontrolle und Effizienz, weil die Projektierung unter Berücksichtigung des industriellen Prozessleitsystems und dessen Struktur erfolgt. Ein industrielles Prozessleitsystem verfügt über Funktionen, die Ihnen auch bei der Projektplanung und -entwicklung helfen. Lernen Sie den Prozess mit der Softwareplattform zenon kennen und erfahren Sie, wie Ihre Projektierung mit zenon noch effizienter wird. Die einzelnen Projektierungsphasen von zenon sind:
1. Konzeption
In der ersten Phase geht es darum, die Komplexität der Projektierung auszugleichen – von den Qualitätsstandards bis hin zu Kostenhindernissen und möglichen Effizienzproblemen. Wichtig dabei: ein schneller Proof of Concept, der zeigt, dass ein Designkonzept realisierbar ist. Dieser Prozess setzt voraus, dass auch externe Vorschriften und Kompatibilitätsanforderungen berücksichtigt werden.
zenon unterstützt diesen Vorgang durch schnelle und benutzerfreundliche Datengenerierung, die eine schnelle erste Testphase mit einer Vielzahl von Standardkonfigurationen und Parametrierungs-Methoden ermöglicht. Die Softwareplattform erfüllt die Konformitätsanforderungen von DNP3, IEC 61850, IEC 60870 und weiteren Normen. Außerdem verfügt zenon über Vorlagenkomponenten und Muster, die Ihnen den Einstieg erleichtern und Sie bei der Entwicklung eigener Musterlösungen unterstützen.
2. Lösungsentwicklung
Bei der Entwicklung und Implementierung Ihres Prozessleitsystems liegt der Schwerpunkt vor allem auf Effizienz. Mithilfe von Symbolen, Vorlagen und Objektorientierung können Sie die Erstellung Ihrer Energielösung beschleunigen. Zudem sparen Sie mit Vorlagen Zeit, indem Sie Komponenten wiederverwenden und die Lernzeit auf ein Minimum begrenzen. Darüber hinaus helfen Ihnen Vorlagen, eine saubere Struktur im Projekt aufrechtzuerhalten, und ermöglichen eine gezielte Überprüfung sowie eine Reduzierung der benötigten Testzeit.
Weitere wichtige Funktionen sind Automatisierungstools und die Konfiguration bestehender Funktionen. Damit diese Phase reibungslos und unkompliziert verläuft, bietet zenon unter anderem folgende Funktionen:
- Bildvorlagen und Symbole: zenon ermöglicht eine einfache Visualisierung mit verschiedenen Layouts für unterschiedliche Aufgaben, einschließlich chronologischer Ereignislisten (CEL), Schaltfolgenmanagement und Befehlsverarbeitung. Dabei können Sie generische Bildsymbole verwenden und dynamische Variablen und Funktionen zuweisen. Anschließend kann das Symbol an mehreren Stellen in der HMI verwendet werden, während die ursprüngliche Symbolimplementierung an einem zentralen Ort verbleibt.
- Smart Objects: Mithilfe von Smart Objects ermöglicht zenon komplexe Automatisierungsvorlagen. Anhand von grafischen Symbolen, Variablen, Datentypen, Treibern, Befehlsgruppen, Detailbildern und Verriegelungen können Sie ein Datenmodell vorkonfigurieren und der Vorlage Alarme, Funktionen und Sichten hinzufügen.
- Import-/Exportmechanismen und Standardwerte: Nutzen Sie solide Import-/Exportmechanismen und praktikable Standardwerte für mehr Effizienz und noch leistungsfähigere Vorlagen.
- Konfiguration und Parametrierung: Diese Funktionen reduzieren die Komplexität, indem sie Ihnen helfen, wichtige Parameter festzulegen, und Ihnen den Rest abnehmen. Sie müssen keinen benutzerdefinierten Code entwickeln oder rückentwickeln und benötigen keine tiefergehenden Programmierkenntnisse. Mit diesen Ressourcen können Sie bei der Entwicklung Ihrer Lösung Fehler durch benutzerdefinierten Code reduzieren und standardisierte Parameter für einfache Übertragungen beibehalten.
- Automatisiertes Engineering: Mit der automatisierten Projektierung sparen Sie viel Zeit, da zenon Ihnen eine einfache Visualisierung und Planung ermöglicht. Die objektorientierte Projektierung von zenon erlaubt Ihnen zum Beispiel, Variablen und benutzerdefinierte Assistenten zu erstellen, um wiederkehrende, standardisierte Aufgaben auszuführen. So können Sie ganz einfach menschliche Fehler minimieren, Arbeitsschritte standardisieren und die Effizienz steigern.
3. Inbetriebnahme
Auch nach der Inbetriebnahme-Phase muss Ihre Lösung flexibel anpassbar und skalierbar bleiben, um Ihr zukünftiges Unternehmenswachstum nicht einzuschränken. Hierbei hilft die Standardisierung von zenon mit Vorlagen, Bausteinen und automatisierten Tools für benutzerdefinierte Algorithmen und Konfigurationsassistenten. Beim Testen können Sie Kommunikationsverbindungen und -status in zenon einsehen und Prozessvorlagen nutzen, um die Wiederholung identischer Tests zu vermeiden.
Ein weiterer wichtiger Bestandteil der Inbetriebnahme ist die Prozesssimulation, mit der Sie Bilder vorbereiten, erste Tests durchführen, Algorithmen steuern und Designs optimieren können. zenon optimiert die Prozesssimulation, indem die Softwareplattform die Treiber in den Simulationsmodus schaltet und die Variablen auf statischen Werten hält oder dynamisch animiert.
4. Erweiterung und Updates
Die Effizienzsteigerung in dieser Phase trägt zur weiteren Automatisierung des Betriebs bei. zenon als Prozessleitsystem ermöglicht es Ihnen, Automatisierungsprojekte klein zu starten und über längere Zeit – und auch mehrere Software-Versionen – zur High-End-Lösung zu entwickeln. So können Sie die Produktionsanlage Schritt für Schritt weiterentwickeln. Dank der modularen Projektarchitektur von zenon können Sie Änderungen und Aktualisierungen schnell und einfach umsetzen, ohne dabei voneinander abhängige Module zu beeinträchtigen. Außerdem bedeutet der modulare Aufbau, dass Sie die Architektur bei Bedarf mit duplizierten, spezialisierten und vorlagenbasierten Modulen erweitern können.
Ein solides industrielles Prozessleitsystem erleichtert die langfristige Kompatibilität und ermöglicht Nachrüstungen, Updates und Erweiterungen auch noch lange nach Abschluss des Projekts.
Ein optimales industrielles Prozessleitsystem mit zenon
Ein industrielles Prozessleitsystem ist für Industrieumgebungen unerlässlich, da es den verschiedenen Bereichen wichtige Funktionen wie Sichtbarkeit, Kontrolle und Datenerfassung bietet. Aufgrund dieser hohen Bedeutung für Ihre Anlagen sollten Sie sich für ein industrielles Prozessleitsystem entscheiden, das von Experten entwickelt wurde. zenon von COPA-DATA ist eine leistungsstarke modular aufgebaute Softwareplattform, die SCADA-Umgebungen hervorragend ergänzt und darüber hinaus Vorteile in Bezug auf Effizienz, Kosten, Datenmanagement und mehr bietet.
COPA-DATA ist bereits seit 1987 in der Branche vertreten. Unsere Softwareplattform zenon entwickeln wir kontinuierlich weiter, um mit den sich verändernden Anforderungen Schritt zu halten und Ihnen die nötigen Logiken und Algorithmen für Ihren Erfolg anbieten zu können. Kontaktieren Sie uns noch heute, um mehr darüber zu erfahren, wie Ihr Unternehmen von zenon profitieren kann.
Wir freuen uns über Ihre Fragen. Kontaktieren Sie uns einfach, wie es Ihnen am liebsten ist: