Aus alt mach neu: Wie EREMA Kunststoffen ein zweites Leben gibt (Österreich)
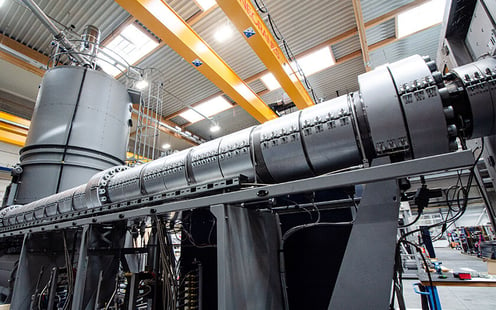
Recyclingmaschinen von EREMA führen verbrauchte Kunststoffprodukte in den Produktionskreislauf zurück. So tragen sie zum Aufbau einer nachhaltigen Kreislaufwirtschaft und zur Vermeidung von Kunststoffmüll bei. Die auf zenon basierende Gesamtsteuerung und Visualisierung sorgt für höchste Effizienz in Engineering und Betrieb.
Highlights
zenon als Visualisierungs- und Steuerungssystem für Kunststoff-Recyclingmaschinen von EREMA
- Einheitliche Benutzeroberfläche
- Schnelles Engineering ohne vertiefende Softwarekenntnisse
- Effizienzgewinn durch Rezepturen
- Hohe Energieeffizienz durch integriertes Energiemonitoring
- Reduzierter Aufwand für Test und Inbetriebnahme
Um den Planeten vor dem Kollaps zu bewahren, müssen wir mehr tun, als den Klimawandel durch die Verringerung der Treibhausgasemissionen zu drosseln. Nachhaltiges Wirtschaften bedeutet, den Verbrauch von nicht erneuerbaren Ressourcen wie Kohle, Erdöl und Erdgas radikal einzuschränken. Es bedeutet auch, die Verschmutzung von Böden und Gewässern durch sich nicht abbauenden Abfall zu vermeiden.
Zero Waste
Verbrauchte Kunststoffprodukte sollen weder auf Deponien noch in den Meeren landen. Auch die thermische Verwertung, also die Nachnutzung als Brennstoff in Fernheizkraftwerken, ist zu hinterfragen. Das Ziel muss eine Kreislaufwirtschaft sein, bei der diese als Sekundärrohstoffe in die Produktionskette zurückfließen und neue Produkte entstehen.
Diese sollen ebenso hochwertig sein wie jene, aus denen sie entstehen. Recycling ist nur dann ökonomisch und ökologisch sinnvoll, wenn es energie-, wasser-, platz- und kostensparend, d.h. ressourceneffizient erfolgt.
Führende Kunststoffrecyclingmaschinen
Als führender Hersteller entwickelt und produziert die EREMA Kunststoffrecyclingmaschinen für alle thermoplastischen Kunststoffe.
Diesen Zielen hat sich die EREMA Engineering Recycling Maschinen und Anlagen Ges.m.b.H. in Ansfelden (Österreich) verschrieben. 1983 als Pionier der Branche gegründet, ist sie heute weltweit die Nummer eins in der Entwicklung und Produktion von Kunststoffrecyclingmaschinen für alle thermoplastischen Kunststoffe wie PE, PP, PET, PS, ABS, PA, PC, Biopolymere und Compounds.
Das Unternehmen ist Teil der EREMA-Gruppe und beschäftigt mehr als 800 MitarbeiterInnen. Diese produzieren mehrere hundert Anlagen pro Jahr und erwirtschaften einen Jahresumsatz von 295 Mio. Euro (2021/22).
Verpackungen aus Verpackungen
Rund um den Globus sind mehr als 6.500 EREMA Anlagen in Betrieb. Damit produzieren EREMA-KundInnen jährlich in Summe mehr als 14 Mio. Tonnen Kunststoffgranulat und verarbeiten 2,5 Mio. Tonnen PET zu lebensmitteltauglichem rPET, aus dem dann Getränkeflaschen und ähnliche Produkte hergestellt werden. Sie schätzen diese Anlagen wegen ihres Innovationsgrades (EREMA hält über 1.000 Patente), ihrer Robustheit und Betriebssicherheit sowie ihrer kompromisslosen Lebensmitteltauglichkeit, Sicherheit und Energieeffizienz.
Im November 2021 erhielt EREMA den Plastics Recycling Award Europe in der Kategorie „Recycling Machinery Innovation of the Year“. Ausgezeichnet wurde damit ein Recyclingsystem zur Verarbeitung von HDPE-Lebensmittelverpackungen zu hochwertigem Rezyklat, das wieder in Verpackungen für Kosmetikartikel oder Lebensmittel eingesetzt werden kann.
Durchgängigkeit und Qualität
In den Bottle2Bottle-Anlagen von EREMA werden die gewaschenen PET Bottle Flakes zunächst unter absolutem Vakuum im Reaktor erwärmt, vorgetrocknet und in mehreren Stufen gereinigt. Im Fall der VACUREMA-Anlagen erfolgt zudem die Dekontaminierung in einem Vakuum-Reaktor. Danach wird das Material der direkt angeschlossenen Extrusionseinheit kontinuierlich übergeben, mit der Extruderschnecke schonend aufgeschmolzen und verdichtet sowie mit höchster Feinheit filtriert. Das erhöht die Energieeffizienz des Gesamtprozesses und sorgt für gleichbleibende Werte bei Farbe, intrinsischer Viskosität (IV) und Qualität.
Anschließend erfolgt entweder die Herstellung von hochwertigem, lebensmittelechtem Granulat zur Weiterverarbeitung oder die Schmelze wird, um zusätzlich Energie zu sparen, in einem Arbeitsgang inline z. B. einer Preform-Anlage zur Herstellung von PET-Flaschenpreforms oder einer Flachfolienanlage zur Herstellung von Folien zugeführt.
Komplexität und Skalierbarkeit
Die Maschinen und Anlagen von EREMA sind modular aufgebaut. So können sie je nach Bedarf zu hochkomplexen Gesamtanlagen zusammengestellt werden. Diese reichen von der reinen Materialaufbereitung bis hin zu schlüsselfertigen Lösungen, bei denen die Schmelze direkt zu den gewünschten Endprodukten wie Flaschen oder Folien weiterverarbeitet wird.
Zum Steuern der einzelnen Maschinen und Teilanlagen verwendet EREMA speicherprogrammierbare Steuerungen (SPS) eines führenden europäischen Herstellers. „Für das Steuern, Bedienen und Beobachten der Gesamtmaschinen ist aufgrund deren Komplexität eine übergeordnete Lösung erforderlich“, sagt EREMA-Automatisierungstechniker Siegfried Blaslbauer. „Um die verschiedenen Anlagenkomplexitäten abzubilden, muss diese einfach zu bedienen und mit überschaubarem Engineering-Aufwand skalierbar sein.“
Maschinenvisualisierung mit zenon
Für die Maschinenvisualisierung nutzt EREMA bereits seit 1999 zenon von COPA-DATA.
Bereits seit 1999 nutzt EREMA zenon für die Maschinenvisualisierung, die zu jener Zeit noch nicht Standard war, sondern als Option angeboten wurde. Siegfried Blaslbauer war zu diesem Zeitpunkt seit mehr als einem Jahrzehnt bei dem Recyclingmaschinenhersteller beschäftigt. Als einer der Beweggründe für die Einführung der Softwareplattform zenon von COPA-DATA nennt er deren Fähigkeiten zur Archivierung von Produktions- und Betriebsdaten, die andere SCADA-Systeme damals in dieser Umfänglichkeit, Geschwindigkeit und Qualität nicht bieten konnten.
„Wir schätzten die Möglichkeit, im Engineering ohne zusätzliche aufwendige Programmierung mit Standardmodulen auszukommen und Visualisierungsprojekte durch reines Parametrieren zu erstellen“, erklärt der Automatisierungstechniker. „Diese Aufgabe erleichtert zenon zusätzlich noch mit der Möglichkeit, unterschiedliche Maschinenkonfigurationen mittels Rezepturen abzubilden.“
Ein System für alle Bedarfsfälle
EREMA nutzt für die Erstellung der Visualisierung Smart Objects. Damit schaffen sie durch reines Konfigurieren einfach zu interpretierende und zu bedienende Benutzeroberflächen.
Die Visualisierung mittels zenon wurde sehr schnell zum Standard bei EREMA-Maschinen. Ihre Funktionen wurden laufend ausgebaut. Dabei nutzen die EREMA-Automationsingenieure sehr intensiv die Funktionalitäten der Softwareplattform, wie zum Beispiel die Chargenverfolgung oder die Energieüberwachung. „Für zenon spricht neben der einfachen Integration der SPS-Systeme unter anderem, dass es Lösungsansätze aus vielen Branchen einfach nutzbar macht“, bestätigt Siegfried Blaslbauer. „Diese integrierten Lösungspakete helfen uns, Maschinen im Betrieb besonders effizient und energiesparend zu gestalten."
Beschränkte sich die Nutzung von zenon früher auf die Visualisierung von Einzelmaschinen, so deckt EREMA heute alle Bedarfsfälle bei der Visualisierung seiner Maschinen und Anlagen ab. Dabei ist auch die übergeordnete Gesamtsteuerung komplexer Großanlagen ein Thema. Gleiches gilt für die Anbindung an MES-Systeme, etwa für die Integration von Schicht- oder Wartungsplänen.
Standardisiertes Engineering
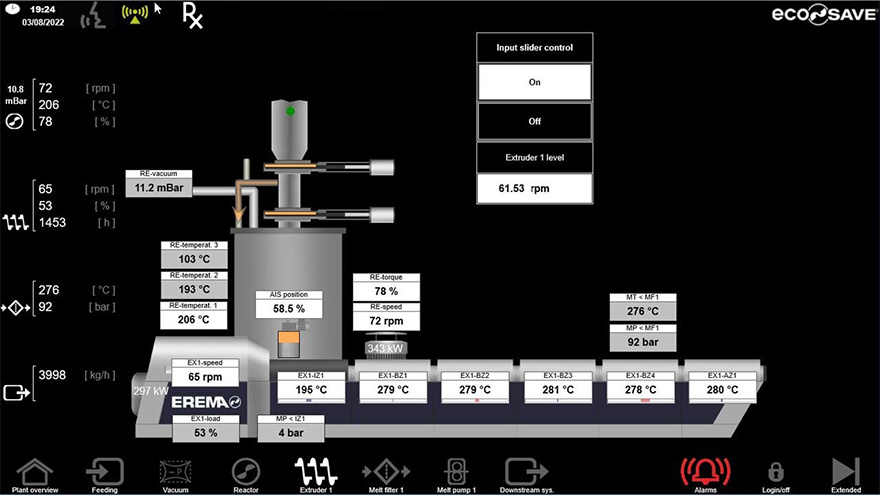
EREMA nutzt für die Erstellung der Visualisierung Smart Objects. Damit schaffen sie durch reines Konfigurieren einfach zu interpretierende und zu bedienende Benutzeroberflächen.
Auch im Engineering setzen die Automatisierer bei EREMA auf Automatisierung. Dazu nutzen sie Smart Objects, die zenon in Bibliotheken für die Erstellung von Bildern, Funktionen und deren Kombinationen zur Verfügung stellt. Diese können überall in einem zenon Projekt aufgerufen und damit beliebig oft wiederverwendet werden. „Engineering mit zenon ersetzt nicht das Denken, aber die Automatisierung mit Smart Objects hat uns bei der aktuellen Maschinengeneration viel Zeit erspart“, berichtet Martin Kienbauer, Leiter Automatisierung bei EREMA.
Die rund 200 Aktoren und Sensoren, die in diesen Maschinen zum Einsatz kommen, werden SPS-seitig per Funktion angesteuert. Zu jeder dieser Funktionen haben die Automatisierungsspezialisten von EREMA ein äquivalentes Smart Object erstellt. „Damit können wir die Übereinstimmung zwischen dem Verhalten der Funktion im Inneren der Maschine und auf der Visualisierung gewährleisten und Software-Inkompatibilitäten als Fehlerursache ausschließen“, erklärt Martin Kienbauer. „Der Aufwand hat sich schnell amortisiert, denn das reduziert den Aufwand für Test und Inbetriebnahme vor Ort um 20 bis 30 Prozent.“
-
Für zenon spricht neben der einfachen Integration der SPS-Systeme unter anderem, dass es Lösungsansätze aus vielen Branchen einfach nutzbar macht.
Siegfried Blaslbauer | Automatisierungstechniker bei EREMA Engineering Recycling Maschinen und Anlagen Ges.m.b.H.
Download
-
Mit zenon von COPA-DATA Maschinen für die Kreislaufwirtschaft belebenEREMA_SUS_DE_final.pdf
Wir freuen uns über Ihre Fragen. Kontaktieren Sie uns einfach, wie es Ihnen am liebsten ist: