Perfect automotive surfaces with zenon
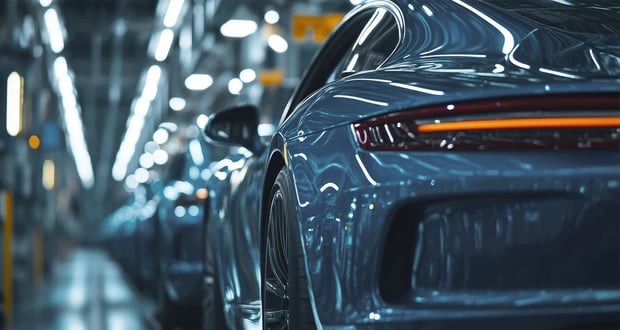
As much as tastes in the color of a car can vary, buyers, dealers, and automakers agree on one thing: paintwork stands for the quality of a vehicle and protects car bodies from the weather. When applied evenly, the paint provides its protective function for the auto body and ensures a beautiful, gleaming surface, rich with color.
Painting technology is considered one of the most sensitive processes in modern automobile manufacturing. It holds this status because of the high degree of process engineering involved. Automotive painting requires the highest precision and innovative technologies to ensure that as little material as possible is lost and emissions to the environment are kept to a minimum. In the painting process, a variety of production steps are necessary. zenon clearly maps this complex structure of process and conveyor technology and manages the entire process from start to finish.
Precision conveyor technology solution for optimized painting processes
The body shop supplies the paint shop with car bodies via fully automated conveyor systems. The subsequent painting process includes several steps. First, the car body is cleaned to obtain a clinically clean surface. Different materials are then applied in layers to provide corrosion protection. After the undercarriage protection has been applied and hardened in the dryer, robots apply further layers of paint and clear coat to produce the vehicle's shiny finish. For transport and to control the flow of car bodies, a reliable conveyor technology is required. Due to the high investment costs for paintwork, these systems are designed to have a long service life. As a result, the paint shop handles a wide variety of vehicle types and models. This diversified production environment calls for complex control to manage the flow of car bodies, material, and parts. In the paint shop, vehicles are often transported through areas that are inaccessible to people for safety reasons. This requires reliable, end-to-end control of these processes.
The zenon software platform provides a wide range of functionalities suitable for use with conveyor technology. The zenon network functions enable the configuration and operation of distributed systems with the ability to manage multiple clients for on-site control. The powerful zenon Multi-Project Administration feature supports intuitive engineering and maintenance for such project structures. The zenon Worldview clearly shows the complete system layout with intuitive navigation and the option of continuous zooming.
To ensure the conveyor technology is operating properly, the positions of the car bodies at various equipment stations are captured automatically. Mobile data carriers enable automatic car body identification which, in combination with central systems, enables car body tracking. This provides transparency over the “lifecycle” in production. This data is also used for calculating the shift-related cycle times of the various production stations and for monitoring throughput times.
-
A variety of steps are necessary in the painting process.
Effective analysis with zenon Process Recorder
Several decentralized controllers manage the conveyor technology that transports car bodies through the different areas of the paint shop. Cross-control data exchange between the individual PLCs is carried out via direct interfaces. The car bodies are identified using data carriers that travel with them. The destinations of the conveyor technology can be detected by querying the process control system. zenon monitors this system in a control room. Users can also intervene here to manage the system. For example, they can define new destinations, block transport routes, or release them for certain vehicles.
The zenon Process Recorder is a valuable add-on for subsequent targeted analysis – for example, in the event that a vehicle reaches the wrong destination. It is integrated in the existing zenon project: the variables from the connected controllers are recorded using the integrated module. Configuration can be completed with a click of a mouse. The optimized recording by the Process Recorder also ensures that the condition data is stored on the server in a way that saves resources.
To interrogate the entire system at a later time, a zenon client can start the Process Recorder in a simulation mode. This client “decouples” itself from the online connection to the server and uses the recorded data to display the values on the screens. The Process Recorder provides a special control screen to “navigate” the timeline. It lists the time stamps of the recorded data and, at the same time, similar to a media player, offers buttons for forward, back, play, or pause. This enables zenon users to bring a past situation back to the screen and study it. Using the controls, users can repeat chosen events at will or stop the display to look at the details. The screen contents are displayed exactly as they were at the time selected. In real operation, such analyses have already made it possible to identify the cause of vehicles being misdirected on several occasions and have helped to further optimize the overall control system.
Interactive, safe operation even in difficult situations
Some production equipment in the painting process can pose a risk to employee health. Despite a high degree of automation in production, a human has to intervene in some situations, such as changeovers, maintenance work, cleaning, or downtime. Well-trained and experienced employees are an important factor here, and zenon supports them with interactive operator prompts that help to avoid stressful situations for employees and reduce potential operating errors. The operator gets clear instructions, a detailed description, and safety information about the work steps that will be performed. The system prompts the operator to carry out certain actions or enter information. The information entered is checked directly for “correctness” and “completeness”. Only when all entries are complete does the process continue. The procedure defined is followed strictly, and the operator is guided through the process. All data and work steps are recorded digitally and are available for use in quality reports.
The interactive operator prompts make it easier for users to carry out the work process, as zenon supports them with sensitive tasks. The assistant function leads to increased productivity and reduces operating errors.
Spotlight on energy consumption
High-performance ovens are used in the drying processes for the painted car bodies. This energy-intensive equipment has to be used efficiently in a continuous production flow. The lengthy heating and cooling stages must also be optimally integrated in the production plan. Continuous monitoring of the energy consumption of the ovens, and all other systems, serves as a basis for identifying inefficient controls or possible malfunctions.
With the help of zenon Energy Data Management System (EDMS), expenses for energy and resource consumption can be reduced significantly. Legal requirements and standards, such as ISO 50001, set the environmentally oriented course. A forward-looking energy data management system not only identifies data for energy consumption, peak loads or usage, but it also establishes rules for proactive behaviors. In this way, for example, peak loads can be prevented and forecasts can be used to optimize future energy consumption.
In the painting processes, the resources being used have to be monitored and recorded continuously. All emission data is logged based on the process values of the hall ventilation system and the central supply of product. The values that require documentation are stored in the corresponding databases and are available in detailed reports.
Interactive quality control
For car buyers, paintwork will always stand out as a visible sign of quality. As a result, the painting process includes continuous, comprehensive quality control measures. The painted car body is inspected by trained employees under special optical conditions. Any defects found are corrected immediately, if possible, or the body is reworked. Using a zenon screen, employees can report complaints conveniently, clearly, and quickly, and these are then reported back to the central systems. The graphics displayed are used to select the corresponding auto body part, and the error type is entered. The position is indicated on the monitor. The processes necessary are then initiated for the rework control system. Employees can record rework, add comments, define times, change error types, and assign rework to the proper cost centers. They use task lists to document the rework requested. By seamlessly recording all data and actions within a cycle period, the system provides the framework for comprehensive quality assurance in the painting process. In addition to
Optimal information flow with consistent usability
This may also require switching and operating actions. The system has to be able to support both centralized and decentralized operation. Depending on the location of the interaction and the user logged on, the operating options may have to be updated. The zenon software platform supports a flexible architecture with a combination of central servers and distributed systems. zenon Multi-Project Administration can help users realize an efficient project structure. The use of clients, standalone stations, and mobile devices ensures end-to-end control of the entire paint shop. To manage the diverse range of equipment, solutions should have standardized styles and a user-friendly navigation concept.
From an ergonomic perspective, it is important to provide a user-oriented interface in terms of data preparation and information visualization. This means users should see only essential and relevant information about their tasks. As a result, users get a better overview of the process and their decisions are not affected by unnecessary information.
For operation and display, the screen contents, as well as underlying functionalities and calculations, are standardized centrally and used across the board.
This has several benefits: by defining things in advance, systems can be put into operation more quickly. Operators can also be deployed more flexibly because the navigation and look of the production areas are identical on all the stations. zenon is designed for universal use thanks to its consistently applied standardization methods. With Smart Objects, process experts develop encapsulated, functional software objects. These can be incorporated easily in the respective equipment projects. They contain all the information needed to ensure their functionality, such as interface variables for the process, formulas for calculations required, or recipes.
Flexible applications in paint technology
The requirements for paint shop technology are demanding and diverse. The systems used have to be flexibly configurable, but they also have to provide a stable architecture. For 25 years, zenon has successfully supported the manufacturing processes described here. Through continuous development, we have met updated security requirements and the other requirements that have developed over time. Thanks to its interdisciplinary strengths, zenon will continue to evolve to meet the demands of the future.
Our Customers
zenon for colorful production
The professionals at COPA-DATA work continuously to improve zenon and its features while maintaining the required logic and algorithms.
Contact our team today a find out more about zenon for automotive manufacturing.
Wir freuen uns über Ihre Fragen. Kontaktieren Sie uns einfach, wie es Ihnen am liebsten ist: