Process automation in the food and beverage industry
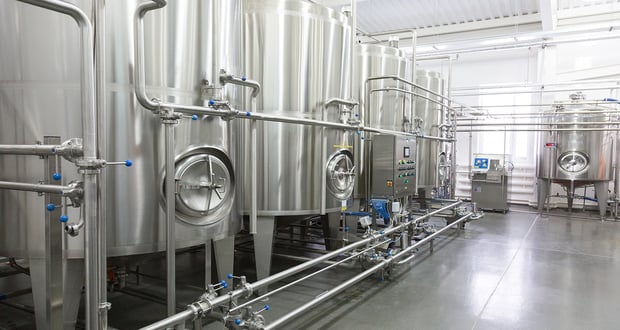
Process automation plays a key role in the food and beverage industry (F&B). In a globalized world, where efficiency, quality, and security are critical, process automation in the food and beverage industry provides solutions to meet these challenges. Increasing digitalization makes it possible to make production processes not only more efficient, but also more flexible and sustainable.
Businesses are faced with the challenge of adapting to rapidly changing market conditions and strict regulations. By implementing state-of-the-art automation technologies, businesses can increase their competitiveness and meet growing requirements. However, digitalizing and automating the end-to-end process flow presents a range of obstacles.
Some of the main challenges are
-
Smaller food and beverage manufacturers may lack the expertise needed to develop their own automation solutions. As a result, these businesses turn to third-party integrators or equipment manufacturers for turnkey solutions. Additionally, the food industry, for example, works with live cultures, which can produce variable processes that require customized responses.
-
Despite a rapid return on investment, process optimization in the food industry and beverage industry requires considerable investment in person hours, hardware, and software. These upfront costs can present a hurdle to going digital. In addition, there are opportunity costs resulting from the production downtime when systems are migrated.
-
When implementing new modules, the software part of this process is critical, especially with integrations with existing systems. Individual devices at field and I/O level may operate autonomously but they will need to be coordinated with other equipment in the future. For end-to-end automation, new equipment has to communicate with existing systems, and this can often be an issue with equipment from different manufacturers.
-
Data security at the level of the process control system is important for process automation in the food and beverage industry. In closed systems, the focus is on protecting production data, often through redundant systems. For external interfaces, such as data analysis in the cloud, the potential for data theft represents a new threat.
-
The scope of automation develops gradually over the entire project lifecycle, often even during commissioning. Many operating requirements only become apparent during testing and through users. Additionally, there is often a discrepancy between the requirements of process engineering and the needs of process automation, which calls for good internal communication among solution providers.
-
Alongside the technical requirements, acceptance by staff is also critical. Even the best automation is of little use without the buy-in of users and staff. The relevant teams must understand the user interfaces and be able to maintain them at the IT/OT level. For this reason, it is important to promote acceptance among all stakeholders.
Modular process automation
Process automation refers to the use of technologies to automatically control and monitor production processes. Its objective is to improve efficiency, consistency, and quality by automating time-critical or complex tasks. Traditionally, this is often done in a monolithic approach, where complete systems are developed and implemented in one step. In this context, modifications or add-ons can be complex and costly.
In contrast, modular process automation takes a more flexible approach. In this scenario, the entire automation process is divided into smaller, independent modules that can be developed, tested, and integrated separately. The modular approach enables a gradual and scalable implementation and continual modernization, as modules can be easily added, removed, or replaced without redesigning the entire system.
Benefits of a modular approach
- Flexibility and scalability: modules can be easily adapted or replaced, allowing businesses to respond quickly to new requirements or technologies.
- Cost efficiency: reusing standard modules reduces development costs and integration effort. This leads to greater cost efficiency.
- Less integration effort: standardized interfaces make it easy to integrate new modules, even from different manufacturers, and they reduce integration effort.
- Shorter time-to-market for products based on low-code/no-code configuration and hence greater flexibility.
- Smaller potential for errors: the use of standardized modules reduces complexity and consequently the likelihood of integration errors.
- Increased ease of maintenance: individual modules can be maintained or replaced independently, increasing system availability and minimizing downtime.
- Better support for innovations: new technologies can be integrated as separate modules, promoting continuous improvement and adaptation as technology advances.
In summary, modular process automation provides a flexible, scalable, and cost-effective solution compared to traditional process automation. It is particularly useful in dynamic production environments where rapid adaptation and innovation are essential.
The entire automation manufacturing process becomes modular
-
The modular approach provides food producers greater flexibility and hardware independence through standardized interfaces. It makes it easier to replace or upgrade equipment, regardless of the manufacturer. This enables tailor-made, cost-effective solutions and faster adaptation to new markets. In addition, modular systems make it easier to produce a variety of batch sizes. Especially for smaller laboratory or trial batches, automated solutions remain easy to implement.
-
OEMs benefit from new opportunities such as easier integration in brownfield projects and reduced automation costs. Thanks to reduced automation effort, equipment manufacturers can decide whether to take on this work themselves in the future or to outsource it, with modular engineering also providing considerable benefits either way.
-
System integrators, who specialized previously in certain software and hardware, will now be able to implement cross-system projects more readily thanks to hardware-independent, modular solutions. This expands their customer base and increases quality and interdisciplinarity. Additionally, more efficient configuration can also combat the shortage of skilled workers.
Modular process automation with zenon
The zenon software platform is itself composed of various components. Depending on the activity, different software modules can be applied and used in combination with each other. At the highest level of modularity are the zenon projects, which consist of variables, images, functions, and drivers.
With its project structure and architecture, zenon enables these projects to be used both in standalone formats and on a network. This means large applications can be easily divided into smaller ones and managed. For example, individual zenon projects can be created for each machine on a filling and packaging line. These projects can be fully functional onsite on the line, but they can also function at the same time as a sub-project in a line management project. This reduces engineering effort while increasing flexibility.
The zenon projects themselves can contain different modular components. The zenon symbols are a good example of this principle: once created as a template, they can be used for any number of instances. Thanks to the ability to release certain properties of the symbol and make them configurable, every instance benefits from flexibility in this regard.
Taken one step further, the concept of symbols is referred to in zenon as Smart Objects Templates (SOT). In addition to symbols, these templates can also contain their own variables, images, and functions. This enables businesses to create templates that can then be customized at the instance level. For example, equipment modules such as valves can be created once as a SOT, and then instances can be created as often as desired in order to recreate a PI&D image with minimal effort. These instances can then be designed, including pop-ups, interlocking conditions, alarm handling, etc. This approach can significantly reduce engineering and testing time.
The zenon Equipment Model module provides an alternative to SOTs for structuring the machines and equipment in a production facility in line with ISA-95. Users can assign variables, functions, symbols, etc. to a hierarchical structure that corresponds to the real production site and group modules in order to visualize or archive alarms, measurement data, etc. depending on the equipment.
Libraries
Since SOTs can also contain zenon logic modules, this combination of zenon technologies provides the prerequisite not only to create templates for SCADA and HMI solutions but also to create modules for a process component library.
A process component library allows system integrators and equipment manufacturers to build a central library independent of the control module manufacturers, which can then be used to create an instance for projects anywhere in the world. It, thus, combines the benefits of zenon’s hardware independence with rapid implementation.
Our Customers
Modular production based on MTP standards
The MTP standard (Module Type Package) divides the production process into standardized services that can be flexibly combined ("Plug & Produce"). A standardized description of the modules enables these to be integrated in a Process Orchestration Layer (POL), which reduces engineering effort.
With the zenon MTP Suite, COPA-DATA provides all the necessary tools for agile, modular production. In the Orchestration Studio you can create modular projects. The Validator allows you to check your MTP files for standards compliance, PEAs can be instantiated from templates, and the MTP Gateway connects existing equipment to the orchestration.
zenon leads the way in topics such as modular production and these advances are shaping new approaches. zenon also supports modular process automation in all other fields, at all levels – and right from the start. If you want be part of these developments from the start, please contact Food and Beverage Industry Management.
Blog & Magazine
-
Emilian Axinia HMI excellence for Original Equipment Manufacturers
MoreWe’ve experienced a great deal of change in recent years. At a global level, the COVID-19 pandemic brought numerous challenges. Supply chains were disturbed and reaching customers suddenly became …
-
Thomas Feßl How MTP can future-proof industrial machines
MoreShorter innovation cycles, smaller product batches and more frequent changeovers are becoming the norm across many industries. In the pharmaceutical sector, this trend is driven by the need to …
-
Thomas Feßl How OEE monitoring enables real-time analysis of production processes
MoreMeasuring, analyzing, and enhancing overall equipment effectiveness (OEE) of an operation can yield significant benefits for manufacturers. OEE expresses productivity as a percentage. For …
-
IU Magazine. Issue 42.
Inspiring stories
IU Magazine. Issue 42.
Inspiring stories/IU-and-Newsletter-Images_Blog_Teaser_610x800px_IU42.jpg?width=620&height=813&name=IU-and-Newsletter-Images_Blog_Teaser_610x800px_IU42.jpg)
Wir freuen uns über Ihre Fragen. Kontaktieren Sie uns einfach, wie es Ihnen am liebsten ist: