Automation and pharmaceutical industry challenges
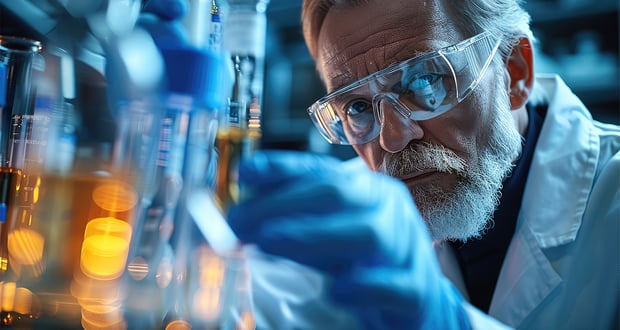
One industry that has come a long way over the past century is the pharmaceutical sector. In the 19th century, patients had no way to know whether the medicines they took would actually help or if they were potentially harmful. For example, doctors often prescribed blue pills of questionable origin and efficacy. In some cases, the pills contained mercury, which is poisonous. At the start of the 20th century, the Pure Food and Drug Act became law in the U.S. The act forbid interstate sale of adulterated drugs.
Though that law was far from perfect, it set the stage for the advancement of the pharmaceutical industry. Over the past few decades, this field has grown by leaps and bounds. Over 48% of adults in the U.S. take at least one prescription medication regularly. Additionally, several pharmaceutical companies set records with the speed at which they developed effective COVID-19 vaccines.
As the pharmaceutical industry continues to grow and adopts new manufacturing technology, it will face new challenges. COPA-DATA's zenon Software Platform can play a role in meeting the needs of any pharmaceutical company. Our solution can help businesses stay competitive and allow them to develop new medications and vaccines safely and efficiently.
Challenges in pharmaceutical manufacturing
Today's pharmaceutical manufacturers deal with equipment that is much bigger and more complex than the vials and tubes used by mid-19th-century apothecaries. Automation helps companies streamline their processes, avoid contamination and ensure the quality of the drugs they produce.
Explore some common pharmaceutical manufacturing challenges below and see how using automation with the zenon Software Platform can help companies overcome these obstacles:
1. Regulations
Regulations combine administrative, technical and legal measures. Governments put regulations in place to guarantee drug quality, efficacy and patient safety. Regulations also help ensure the information provided about medication is accurate and relevant.
Federal regulations can change to meet the needs of consumers and manufacturers. Companies that fail to keep up with these regulatory shifts will face severe fines and business disruptions. They can also put patients' lives and well-being at risk. This is why, whether you are part of a company that manufactures Class II or Class III drugs, APIs or medical devices, if you sell in the U.S. market sooner or later you will face an FDA inspection. Some companies will receive 483 observations, while others will receive a warning letter. It is critical to understand the differences between these two communications in order to respond appropriately to the Authority.
483 Observation
A 483 is an observation about something FDA considers significant relative to a problem or potential problem observed during an inspection. It may relate to the facility, equipment, processes, controls, products, activities, or personnel records. "Potential problems" should have a reasonable probability of occurring based on what the inspector observed. A 483 may refer to inadequate situations, as long as FDA provides examples or explanations as to why those conditions should be considered so. A 483 can be very costly to companies, costing thousands or even millions. This is because if the problems highlighted affect the entire system, the 483 may involve training, redesign, process implementation or other measures. Therefore, it is best to anticipate the issues that could result in a 483 and structure robust processes to avoid this scenario.
The most common causes that lead to a 483 are:
- Procedures not followed
- Inadequate investigation and lack of CAPA process
- Absence of written procedures
Warning Letter
A Warning Letter, on the other hand, is a formal notification from FDA that identifies serious regulatory violations. A Warning Letter is issued by more senior FDA officials after reviewing an inspector's report and the company's response to a 483. The Warning Letter is considered an escalation of the 483 observation.
The primary causes that lead to a Warning Letter are:
- Written procedures not in compliance
- Personnel not following procedures
- Failure to document evidence of adherence to standards
The Warning Letter requires a written response within a maximum of 15 days. If the cause of the Warning Letter is serious, FDA may give the company a longer response time. Violations described in a Warning Letter are required to be handled and corrected if you want to continue selling in the U.S. market. Warning Letters are public so anyone can see what violations were found at each inspected company. Warning Letters, like 483s, can cost companies significant assets by delaying market access. Using a software platform that follows regulatory guidelines ensures a pharmaceutical manufacturer remains compliant with all relevant regulations.
2. Efficiency
It takes an average of 10 years for a prescription medication to be developed and approved for use. There are obviously exceptions to the rule, such as the COVID-19 vaccines that were approved by the Food and Drug Administration for emergency use at the end of 2020.
The high cost of research and development — along with a failure rate of seven out of eight drugs in clinical trials that don't reach consumer sales — contributes to rising costs and a decrease in efficiency.
While manufacturers can recover the costs during the initial 180 days of exclusive drug production, focusing on decreasing drug costs by pushing through generic applications can increase the number of competitors on the market. Adding a pair of generic competitors can drop the price of the original brand name medication by 52%.
Biosimilar drugs replicate the function and structure — with only minor differences — of brand name medications at a fraction of the cost. The FDA considers some biosimilar drugs to be interchangeable, meaning a patient may use a biosimilar drug to replace one their doctor prescribed without calling the physician first. Like generic drugs, biosimilar pharmaceuticals do not require as much testing to gain approval, hence their lower costs.
With rising competition from both generic and biosimilar drugs, manufacturers and contract development and manufacturing companies (CDMOs) must find ways to remain relevant and profitable in the market. Increasing efficiency can help a manufacturer or CDMO develop medications more quickly, potentially reducing the time it takes to get them to market.
-
zenon fully meets the requirements created by FDA 21 CFR Part 11, plus international regulations
3. Data integrity during digitization
The future of record-keeping is digital. Relying on physical paperwork takes more time and effort, as it usually requires human input. Physical paperwork also tends to be more error-prone. A person can misrecord a notation or put a digit in the wrong place, throwing off the data's accuracy and potentially ruining an entire batch of medication. Digitalization also helps ensure records are clean and compliant with any and all regulations.
Using paper along the supply chain for manufacturing can cause problems with lost documents, missing information and communication issues. Going digital for supply chain communications and documentation prevents these issues while allowing better forecasting and flexibility throughout production levels.
ISPE Pharma 4.0 Special Interest Group is actively working to make it easier to integrate manufacturing and IT systems. Recently ISPE issued a Concept Paper entitled: "Connectivity between shopfloor and Manufacturing Operation Management Systems with OPC UA - A tangible step towards Plug & Produce (April 2021)”, also with the contribution of COPA-DATA.
Digital integration between shopfloor and IT systems is a key function of zenon software platform. As example we mention the integrated MSI interface to integrate zenon to Werum PAS|X MES system with ease.
Pharmaceutical manufacturers can move to digitization and reduce errors at all phases of production by choosing machinery that is Pharma 4.0-ready. Similarly, they can also do so by using an Automation Integration Layer when onboarding data for their current equipment.
4. Resistance to change
The pharmaceutical industry can be resistant to change for several reasons. Change can be difficult to accomplish due to management resistance to major alterations in operations. The industry is also highly regulated, which means any change made can be expensive because of the need for revalidation. Some manufacturers might prefer to stick to paper records because doing so makes it easier to mask errors.
However, manufacturers need to grow and change, due in large part to data integrity regulations. Under the regulations, manufacturers need to digitize their operations and switch to electronic records. This is a massive cultural shift within the sector. Pushing companies to move on from what worked in the past and pivot toward what will work for the future is essential so pharmaceutical manufacturers can grow and thrive in upcoming years.
5. Flexible and modular production in plants
The next growth area for pharmaceutical companies is personalized medicine. Personalized medicine tailors treatments to each patient based on their genetic profile. With personalized medicines, doctors can eliminate much of the trial and error associated with traditional medical treatment. This can help patients get the precise treatment they need — when they need it and at the optimal dose. With the rise of personalized medicine comes an increased need for smaller batches of medications. Those batches will also often need customization for each patient.
Modular manufacturing allows pharmaceutical processing companies to produce multiple batches of various types of drugs, all from the same facility. A traditional plant layout makes it challenging for a factory to switch over and adjust equipment as needed to produce several different types or strengths of medications. To allow for modular production, some processors are using a ballroom layout, meaning there is no fixed equipment. The facility can be broken down and rearranged as needed, depending on that day's manufacturing needs.
As more manufacturers embrace modular production, there will be a need for renewed techniques within their facilities. For example, manufacturers will require a method of efficiently mapping out the sequence of a process and planning how to reduce the time to market for medications.
To support this challenge the association NAMUR propose the MTP concept. MTP stands for “Modular Type Package”. Thanks to MTP flexibility and interoperability in process automation is going to be a reality. COPA-DATA strongly believes in MTP. For more information about MTP have a look to this article.
How zenon Can Help Pharmaceutical Manufacturers Face These Challenges
The right software can address many of these concerns. With a technological solution to meet the industry's challenges, shifting toward future-focused operations becomes easier. COPA-DATA's zenon Software Platform fulfills these needs in several ways.
1. Comprehensive Software
Your business needs an all-in-one software solution to track data, control machinery and improve efficiency, and zenon offers all of these features. The platform's scalability allows it to adapt to both large- and small-scale production.
The zenon Software Platform integrates several products into one production solution. Your facility can benefit from the following qualities:
- Automated production
- Process control
- Quality and production report creation
- Report analysis
- Audit trail creation
- Alarm management
- User administration
2. Regulatory Compliance
Protecting data integrity to meet the requirements of regulatory authorities is possible with zenon Software. Our platform fully meets the requirements created by FDA 21 CFR Part 11, plus international regulations.
zenon makes the validation process easy. Our software platform protects data integrity and helps you get faster product approval in multiple ways. The software platform creates audit trails to trace those who access the system and data. By eliminating paper data that can fade over time, your records remain traceable for years for audit information.
Using data creation immediately after production enables your facility to get approval more quickly for each batch produced. Also, with our alarm controls, you can stop production and address problems immediately, reducing wasted time and product.
3. Flexible Production
Production accessibility and flexibility set zenon apart from other software programs. Our platform uses ISA 88 Batch Control, which means you can validate a system once for producing a batch and make changes to recipes as needed without revalidating. The ISA 88 standard from the International Society of Automation provides notable terminology within batch control operations and offers information on comprehensive, regulated data structures. This facilitates easier communication between batch components and offers a common touchpoint for understanding between manufacturers.
The flexibility of batch control also regulates the entire production system. With zenon, you can integrate new and used equipment from various manufacturers, control your systems and create reports that allow you to optimize production.
COPA-DATA has been committed to simplifying processes with digital and automation solutions for over 30 years. Today, the technology behind it has a name: MTP. We draw on our extensive experience to continuously advance the zenon software platform. You can rely on us to meet your modular production requirements both now and in the future. When well thought through, modularization via MTP can revolutionize the process manufacturing sector and make it competitive for the future.
-
Integration of modules via MTP allows for a new level of flexibility
4. Paper on Glass and Automation Integration Layer
Our Paper on Glass technology replaces old paper records for batches with real-time controls from a tablet. Missing or incorrect entries disappear, allowing for improved consistency between batches. Plus, with remote control, your operators can start production sooner and see reports immediately. You can achieve better quality during each batch's first production run thanks to the digital verifications our Paper on Glass technology offers.
Converting your facility to electronic records with zenon prevents lost data, ensures secure archiving, allows immediate reporting and offers accurate information. No longer will your facility have to track and store large amounts of physical paper that could become lost or damaged, reducing your production tracking capabilities.
The zenon Software platform easily connects on premises or cloud-based Data Storage. (e.g SQL Server or Mongo DB). These remote servers store encrypted data that always remains available from anywhere. Data are safely sent from zenon to Data Storage using an integrated buffering mechaninsm, so that GMP relevant process information are never lost.
Cloud-based storage allows for easy scalability as your company's record-keeping needs grow.
The Automation Integration Layer (AIL) lets you connect older manufacturing equipment to your company's IT infrastructure while remaining compliant with relevant data integrity regulations. AIL is a scalable software platform that can extract, consolidate and evaluate current data as it develops a new network. AIL will support your manufacturing plant on its journey to connectivity. Features of the AIL include data encryption, ongoing updates and easily configurable authentication features.
5. Building management system, environmental monitoring system, centralized technical services
In a life science facility, there are technical services like purified water production for water for injection (WFI) or clean-in-place/sterilization-in-place (CIP/SIP) systems that require data management according to Current Good Manufacturing Practice (cGMP) regulations. Sterile manufacturing area environmental parameters, such as temperature, pressure and humidity, must be monitored, logged and recorded to detect any deviations. The zenon Software Platform easily integrates various sensors distributed in different locations. Thanks to the integrated soft logic, mathematical operations can easily be created.
The platform distributes the right information to a responsible group of persons using the integrated network capabilities. It also provides evidence to inspectors, thanks to an integrated reporting module.
Contact COPA-DATA for Answers to Your Questions
Pharmaceutical manufacturers can meet the coming challenges with technological innovations in data handling. For more than 30 years, COPA-DATA has helped those in the industry with innovative software solutions. At COPA-DATA, we are always continuously improving our software to adhere to all necessary logic and algorithms to meet the industry's changing needs and future obstacles.
As your business continues changing to overcome industry hurdles, our zenon Software Platform will also adapt to your company's shifting needs. When you integrate zenon into your operations, you benefit from the software's scalability, flexibility, regulatory compliance and security. For any questions you may have about zenon or COPA-DATA, contact us.