zenon MSI Interface integrates easily with Werum PAS-X MES
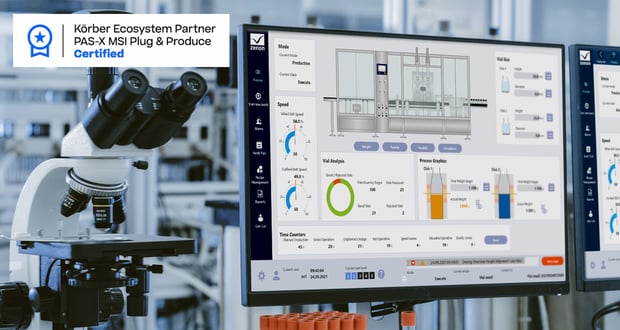
Pharmaceutical companies are pushed to make production lines and their processes increasingly flexible and compliant with Data Integrity regulations. To meet these requirements, a Manufacturing Execution System (MES) and an Industrial Control Software are needed, not only in terms of functionality but also in terms of usability. However, the vast majority of companies still rely on error-prone manual documentation. So, bridging the gap between your MES and your Industrial Control Software gets even more challenging.
Needless to say, the transition from paper-based batch records to electronic ones is one of the biggest aspects in the life sciences industry.
The challenges and limits of the classical approach
In today's approach, MES is used to exchange messages with one message including all parameters such as Batch ID, Product Name and Recipe Name, while most ICS software uses real-time values (TAGS).
MES systems, like all IT systems, are not designed to exchange values in real-time with SCADA and PLC. Communication between MES and shopfloor takes place in a transactional manner by exchanging messages in the specific moment.
This means the conversion between the two is not easy and can create limitations with your data integrity. The production results and any GMP exceptions (e.g. a critical product quality alarm) are not transferred to the MES system. Therefore, operations need a streamlined MES integration with their Industrial Control Software to benefit from the needed amount of flexibility.
The right Industrial Control Software will help your plant with everyday challenges
This is where a communication interface called Werum PAS-X MSI Plug & Produce (Message-based Shopfloor Integration) comes into play in order to solve the limitations of current OT and IT integrations.
Werum PAS-X MES by Körber is the leading MES for pharma, biotech, and cell & gene therapy used to implement Electronic Batch Records (EBR). To communicate with shop floor equipment, PAS-X MES offers the MSI adapter. The adapter is designed as a message-based solution and builds on the industry-standard communication technology OPC-UA and REST-based web services. PAS-X MES sends batch parameters in messages to the Industrial Control Systems and receives values or GMP exceptions.
Using zenon as Industrial Control System you will be able to bridge the gap with Werum PAS-X MES by offering an integrated configurable MSI connector to connect machines and manufacturing lines with ease.
Does Werum PAS-X MES integrate with zenon?
zenon's MSI interface allows you to receive and send batch information from/to PAS-X MES directly to your equipment as well as sending GMP alarm data to the MES. The zenon PAS-X MES integration will allow you to reduce errors, improve batch release time and reduce downtime between batches. But most importantly, it allows you the much-needed flexibility of a modern life sciences facility.
The current version includes new and innovative functions, ensuring an unsurpassed level of usability supporting the following MSI messages:
-
Used by PAS-X MES to send parameters to zenon, or by zenon to send back counters and values. (e.g., Start Batch, In-Process Controls, End of Batch).
-
Triggered by zenon when a GMP relevant deviation occurred during batch execution. (e.g., when the Sterilization Temperature Low Limit Alarm is activated).
-
Triggered by zenon to inform PAS-X MES about current equipment status or operation in progress. (e.g., “Recipes download to PLC in progress …”).
-
Triggered by zenon to inform PAS-X MES to indicate that the order or recipe on the equipment has been aborted.
With the push for productivity and flexibility in pharmaceutical production lines, the zenon PAS-X MES integration provides the functionality your operation needs.
Transform your brownfield application
The scenario offers a 'Plug & Produce' approach for new machinery. However, it is also necessary to think about existing machines in the company. Machines that have been installed for some time and are functioning correctly but do not have a direct interface to Werum PAS-X MES nor integrated Data Storage capability. For this use case, middleware between the existing machines and the MES system must be provided.
Through the zenon software platform, it is possible to implement a modular and scalable middleware that we call Automation Integration Layer serves (AIL). In this configuration, zenon offers integration with existing machines through wide connectivity with PLCs (including legacy PLCs like Simatic S5!) and field equipment, contextualization and historicization of collected data, and integration with Werum PAS-X MES through the MSI interface.
For example, zenon receives a batch open message from PAS-X MES. Interpreting the message, zenon routes the received information to the recipient machine by mapping it based on the possibilities offered by the existing controller. Batch contextualization, if not present in the machine, is implemented in zenon AIL so that the information collected such as counters or GMP alarms can be correctly sent to the MES system at the end of the batch.
However, zenon is not limited to integration with Werum PAS-X MES. Other interfaces to IT systems such as Historian or ERP are available. Last but not least, within zenon it is also possible to use the collected data to create dashboards or reports addressed to the various company functions as presented in figure 1.
-
Figure 1 – zenon as a modular Automation Integration Layer, including Data Storage, Reporting and IT integration.
Green field scenario: A PAS-X MSI Plug & Produce Ready machine
A typical green field use case concerns the use of zenon as an on-board machine HMI. In this case, the machine can include a Werum PAS-X MSI interface pre-configured by the manufacturer for classic batch opening and closing operations and for sharing critical GMP alarms. The messages to be exchanged with the MES can be agreed upon in advance with the end customer. The machine arrives at the customer with the MSI interface pre-configured.
For integration with the end customer's PAS-X MES system, it will be sufficient to share the MSI message definition prepared by the manufacturer. Finally, some addresses must be configured to establish communication between the machine and the MES system. The messages prepared by the machine manufacturer can, however, be modified in the future by the end customer to better adapt them to their own needs through menus that can be configured according to GAMP5 SW CAT.4. A simplified approach that does not require costly hierarchical integration. This is why we can call such machines PAS-X MSI Plug & Produce Ready.
-
Figure 2 – Direct integration of PAS-X MSI Plug & Produce Ready machines with integrated Data Storage capability
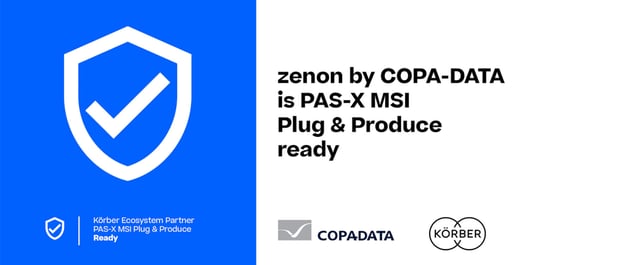
zenon by COPA-DATA is PAS-X MSI Plug & Produce ready
See also Körber’s press release about zenon’s PAS-X MSI Plug & Produce ready certificate.
zenon MES integration for Life Science Industry
Whether you use a biotech MES or a pharmaceutical MES, zenon offers a solution for complete connectivity and project validation. zenon by COPA-DATA is a powerful modular platform that delivers benefits for efficiency, costs, data management, and features data integrity tools such as Line Execution System (LES), ISA 88 Modular Process Automation, Continuous Manufacturing and much more.
Here at COPA-DATA, we are continuously enhancing our Industrial Control Software to meet the industry's evolving needs. We utilize all the necessary logic and algorithms to keep your business moving. Reach out to us today to learn more about zenon and what it can do for your organization.