What is SCADA?
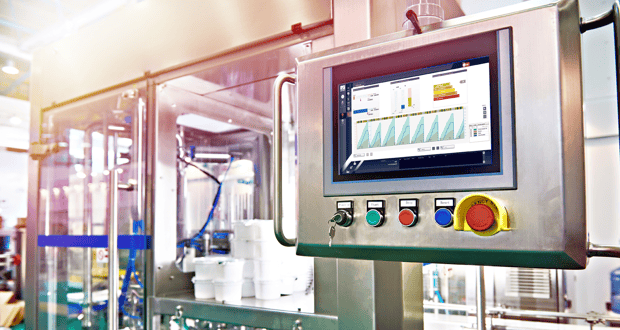
SCADA systems are crucial for a wide range of industrial organizations. These systems allow organizations to control assets of various sizes as well as entire plants. With a SCADA based on zenon, you can easily gain operational insights, control your processes and make data-driven business decisions.
On this page you find:
Definition of SCADA
SCADA stands for supervisory control and data acquisition, a term which describes the basic functions of a SCADA system. Companies use SCADA systems to control equipment across their sites and to collect and record data about their operations.
SCADA typically comes in a combination of software and hardware elements, such as programmable logic controllers (PLCs) and remote terminal units (RTUs). Data acquisition starts with PLCs and RTUs, which communicate with plant floor equipment such as factory machinery and sensors. Data gathered from the equipment is then sent to the next level, such as a control room, where operators can supervise the PLC and RTU controls using human-machine interfaces (HMIs). HMIs are an important element of SCADA systems. They are the screens that operators use to communicate with the SCADA system.
Using SCADA systems, organizations can control their industrial processes either locally or remotely and directly interact with pieces of equipment, such as motors, pumps and sensors, across the board from a central location. Sometimes, these systems can control equipment automatically based on incoming data. SCADA systems also enable organizations to monitor and report their processes based on real-time data and archive the data for subsequent processing and evaluation.
Applications of SCADA
Organizations can use SCADA systems to:
- Control processes locally or remotely
- Interact with devices through HMI software
- Collect, monitor and process data
- Log events and data
These functions give companies enhanced visibility into their processes. The data they collect enables them to see how their machinery is functioning in real-time and also view long-term trends to identify improvement opportunities. Based on this data, operators can then adjust how their equipment runs using SCADA-enabled controls. They can make changes either remotely or on-site and can adjust operations on the level of entire facilities, individual processes or just particular machines.
SCADA systems also enable organizations to use their data to improve efficiency, inform decision-making and enhance communication to help prevent downtime. To get the most benefit from your data, which you collect from various sources, you need to store it centrally in a SCADA system. A well-integrated SCADA software can combine data from numerous sources, process it and then send it to other systems in various formats.
Advanced SCADA software can create complete and custom reports. Your equipment may also be able to react automatically to the information in these reports. In a quality management application, for example, the system may trigger an alarm if a report indicates that a batch of products is defective. In energy management, a system may reduce the power consumption of certain machinery or systems if a load peak is forecasted.
Through functions such as these, SCADA systems can save organizations significant amounts of time and money. They can help companies increase the efficiency of their operations, reduce downtime, ensure product quality and much more.
SCADA systems can range from relatively simple to massive and complex, depending on the organization using them and the applications in which they're used.
An extensive SCADA network
SCADA systems are important for organizations both large and small across a wide variety of industries, including:
For a vast range of sectors and organizations, SCADA systems play a central role in how companies control their operations and use their operational data to make better decisions.
Benefits of using SCADA software
Using SCADA software provides numerous benefits to businesses, and zenon helps companies make the most of those benefits. Some of these advantages include:
- Easier engineering: An advanced SCADA application such as zenon provides easy-to-locate tools, wizards, graphic templates and other pre-configured elements, so engineers can create automation projects and set parameters quickly, even if they don't have programming experience. In addition, you can also easily maintain and expand existing applications as needed. The ability to automate the engineering process allows users, particularly system integrators and original equipment manufacturers (OEM), to set up complex projects much more efficiently and accurately.
- Improved data management: A high-quality SCADA system makes it easier to collect, manage, access and analyze your operational data. It can enable automatic data recording and provide a central location for data storage. Additionally, it can transfer data to other systems such as MES and ERP as needed. zenon has a variety of drivers and open interfaces to enable this, even across heterogeneous hardware landscapes.
- Greater visibility: One of the main advantages of using SCADA software is the improvement in visibility into your operations. It provides you with real-time information about your operations and enables you to conveniently view that information via an HMI. SCADA software can also help in generating reports and analyzing data.
- Enhanced efficiency: A SCADA system allows you to streamline processes through automated actions and user-friendly tools. The data that SCADA provides allows you to uncover opportunities for improving the efficiency of the operations, which can be used to make long-term changes to processes or even respond to real-time changes in conditions.
- Increased usability: SCADA systems enable workers to control equipment more quickly, easily and safely through an HMI. Rather than having to control each piece of machinery manually, workers can manage them remotely and often control many pieces of equipment from a single location. Managers, even those who are not currently on the floor, also gain this capability.
- Reduced downtime: A SCADA system can detect faults at an early stage and push instant alerts to the responsible personnel. Powered by predictive analytics, a SCADA system can also inform you of a potential issue of the machinery before it fails and causes larger problems. These features can help improve the overall equipment effectiveness (OEE) and reduce the amount of time and cost on troubleshooting and maintenance.
- Easy integration: Connectivity to existing machine environments is key to removing data silos and maximizing productivity. zenon features more than 300 available communication protocols to enable simple integration into your existing machinery and network infrastructure. It also features pre-configured drivers, functions and variables that you can use across projects.
- Unified platform: This isn't the case with all SCADA systems, but with zenon, you can control all of your equipment and processes using one unified platform, which significantly reduces operational complexity and makes your life easier. All of your data is also available in one platform, which helps you to get a clear overview of your operations and take full advantage of your data. All users also get real-time updates locally or remotely, ensuring everyone on your team is on the same page.
A brief history of SCADA
SCADA enables organizations to control equipment, even over long distances, and gain data-powered insights into their operations.
Before SCADA was introduced, many industrial organizations relied on workers manually controlling and monitoring equipment using analog push buttons, dials and other controls and gauges.
As industrial sites began to expand in size and remote sites became more common, companies needed more efficient ways to control equipment. They began to use relays and timers to gain some level of control over long distances and without the need for manual interaction with each device.
Relays and timers added some automation capabilities but could also be difficult to reconfigure and troubleshoot. The control panels also had a large footprint. As industrial operations continue to grow larger, companies needed a more efficient method of control and monitoring that provided more comprehensive automation functionality.
With the introduction of computers into the industrial space, control and automation capabilities improved. Utilities and other industrial organizations began to use computers for supervisory control. Telemetry technology was also introduced, which enables the automatic measurement and transmission of data across distances. As microprocessors and PLCs became more common, these monitoring and control systems became more sophisticated, and the term SCADA came to be.
The integration of modern IT practices and technologies such as web-based applications, OPC and SQL into SCADA software has significantly increased its capabilities and enhanced its efficiency, reliability and security. Today, many SCADA applications have features that enable engineers to design applications quickly and easily even if they don't have extensive software development knowledge. This opens up the use of SCADA systems to more individuals and organizations.
-
With zenon, you can control all of your equipment and processes using one unified platform. Reduce the operational complexity and make your life easier.
Modern SCADA systems provide users with real-time data about their facilities' operations, which they can access from anywhere in the world. The ability to record and replay events also enables users to review incidents to make changes to prevent problems from reoccurring in the future. This process recording feature can also be useful for employee training.
HMI and SCADA
SCADA and HMI are often discussed together and even used as interchangeable terms. However, they are not synonymous. They are, though, part of the same system.
An HMI is part of the larger SCADA system, along with PLCs, RTUs and other features. The HMI is the part of the system that operators use to interact with the SCADA, while the larger SCADA system does the work of collecting and storing SCADA data and controlling equipment. HMIs typically feature screens and, ideally, user-friendly dashboards and controls. They may use graphics and visualization to make data and features easier to use and understand.
An HMI is an essential element of a SCADA system since it's what you use to interact with and manage the system. Without an HMI, you could not take advantage of the many useful features of SCADA systems. The SCADA system, on the other hand, provides the actual functionality.
HMI and SCADA are often referenced together because they are part of the same larger system. The term SCADA refers to the larger systems and all of its functionality, while HMIs are the screens that workers use to interact with and control the SCADA system.
It is possible to use different HMI and SCADA systems. However, as connectivity becomes more important than ever in the Industry 4.0 era, businesses are increasingly looking for an integrated platform that can consolidate data pipelines for holistic, enterprise-wide management of their industrial equipment, processes and people.
-
zenon collects and analyzes data for better business decisions, such as quality assurance, production optimization and energy management.
The future of SCADA
As technology continues to advance, SCADA systems gain new functionality and begin to play a key role in IoT enabled smart factories and smart cities.
Today's SCADA systems can automatically collect data in real-time from sensors located across a facility. They then make this data available to authorized personnel via local servers or the Internet connection. These enhanced data collection and management capabilities allow companies to benefit from the advanced data analysis technologies available today. For example, zenon securely collects, connects and analyzes data, turning it into insights for better business decisions, such as quality assurance, production optimization and energy management.
SCADA systems are also increasingly making use of modern IT standards with the rise of IT/OT convergence. The use of open standards such as OPC UA and SQL makes it easier to integrate a SCADA system into a manufacturing execution system (MES) and enterprise resource planning (ERP) system. Combined with cloud computing, this allows businesses to connect operational and business systems and share data across the entire enterprise.
More and more users access their projects from tablets and mobile devices, enabled by web-based and mobile-responsive applications. Using zenon's HTML 5 technology, for instance, users can easily configure dashboards, screens, KPIs, etc., and acquire process data from anywhere at any time. This greatly improves the efficiency, security and productivity of the SCADA projects.
Another recent advancement in HMI/SCADA systems is the support of multi-touch gestures in HMIs. zenon is the first software to offer this. Multi-touch gestures enable new methods of operation, enhanced usability and improved operational security.
As companies increasingly focus on industry 4.0 technologies, SCADA systems will continue to play an integral role in industrial operations. Advanced data analytics, machine learning and other related technologies will also become more important parts of the system. Meanwhile, industrial facilities are becoming more interwoven and SCADA systems will be more interconnected with other business systems and equipment. As a result, SCADA will evolve to become more open, secure, flexible and accessible, driving the digital transformation.
zenon's SCADA solutions
The zenon software platform encompasses SCADA, HMI, soft PLCs, IoT, reporting, alarming, messaging and more in one integrated platform. Projects from various industries such as energy, automotive, food and beverage, pharmaceutical and other sectors use zenon to monitor, analyze, control and automate the processes.
Using zenon as an HMI/SCADA application gives you enhanced visibility into your operations and improved control over your processes, either on-site or remotely. The platform can assist in collecting real-time information about your operations and distributing this information to authorized users, so your organization can make the most of it.
zenon also features graphical HMIs with efficient controls and easy-to-read visualizations of events and alarms. Users can create custom dashboards and quickly gain access to the information they need. The intuitive multi-touch functionality helps make it easier and safer to control processes.
The software platform ensures a more unified environment that enhances consistency and ease of use. It is independent of the hardware used, which gives you a consistent control system and makes it easier for workers to operate machinery. Machine operation, data recording and business intelligence are also all integrated into one platform.
With its more than 300 supported communication protocols, simple-to-setup ERP and cloud interfaces, zenon becomes a key component in the Industrial Internet of Things (IIoT), helping organizations make smarter decisions and embrace the shift towards industry 4.0. To learn more about our industrial automation and SCADA solutions, contact us today.
SCADA Solutions by zenon
All you need to know about the past and the future of SCADA automation
Wir freuen uns über Ihre Fragen. Kontaktieren Sie uns einfach, wie es Ihnen am liebsten ist: