Industrial Control Systems
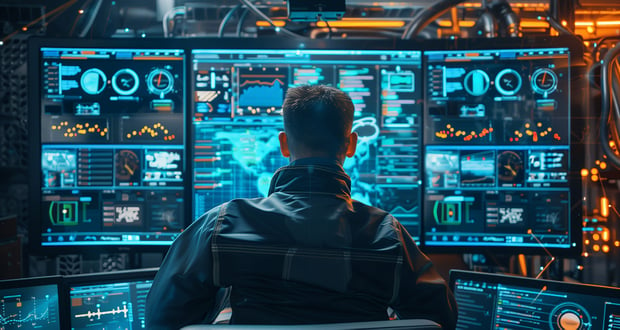
An Industrial Control System (ICS) is an essential part of many organizations, supplying automated controls for a wide range of components across multiple locations. ICSs come in a few different types and can support a massive range of elements in various operations, from energy to manufacturing to pharmaceuticals. They deliver benefits for efficiency, quality, analysis and, of course, your bottom line.
Let's take a closer look at ICSs and what they can do for industrial operations.
What is an industrial control system?
Industrial control systems handle various components, such as monitoring devices and software systems, to manage operations and automate them where possible. They balance the many components necessary for operating an industrial environment, ensuring these components work efficiently and in synchrony with each other. An ICS can take control entirely or be part of a hybrid approach that incorporates human interaction. Open-loop, closed-loop and manual options are available.
If your industrial organization involves the Industrial Internet of Things (IIoT) or other smart systems, an ICS is especially useful and minimizes security risks. Overall, ICSs provide greater visibility and user-friendly control of a complicated network of components. Some elements you might find within an ICS include servers and controllers such as:
- Remote terminal unit (RTU): An RTU is a field device that communicates with a master terminal unit and functions as a supervisory controller.
- Human-machine interface (HMI): With an HMI, humans can interact with the hardware controlling the machinery. The HMI usually takes the form of a graphical user interface (GUI) that creates a human-readable platform — in essence, software. Users can view current statuses, monitor setpoints, receive security alerts, adjust parameters and algorithms, assess historical data and more.
- Programmable logic controller (PLC): As one of the controllers of an ICS, a PLC allows for local process management or connection to an HMI. You may also see programmable automation controllers (PACs), which are similar to PLCs, but are often more advanced and may include more memory and programming flexibility along with additional features.
- Soft PLCs: PLCs can also be found in a centralized database, fed by data off the production line. zenon Logic, for instance, offers a built-in PLC environment that engineers can access through a shared database. They only need to create objects once and can repeatedly access them in the system.
- Control server: This server hosts the supervisory control software for a PLC or distributed control system (DCS). It can also communicate with lower-level control devices.
- IT and operational tech: Different devices such as sensors monitor in-field operations.
- Control loop: A control loop has different types of hardware like PLCs and actuators that interpret sensor signals, switches, breakers, control valves and more. Then, they send that information to a controller to perform a certain task.
- Remote maintenance system: This system can monitor for and detect anomalies or failures, possibly even taking action to prevent problems.
- Master terminal unit (MTU) or SCADA server: The MTU or supervisory control and data acquisition (SCADA) server can deliver commands to in-field RTUs.
- Smart electronic devices: A smart device can collect data and communicate with other devices. With SCADA and DCS infrastructures, these devices can execute local controls automatically.
- Data historian: Data collected from the ICS and its operating environment is stored in a data historian and exported to another information system. There, it can be processed for further analysis and strategizing.
The benefits of an industrial control system
Industrial automation via an ICS has a range of advantages for industrial organizations. Some industrial control system benefits include:
-
With fewer manual requirements and greater productivity, an ICS helps you boost efficiency. You can reduce manual operations and energy use. The 24/7 functionality of an ICS is a great way to enjoy around-the-clock automation or use downtime for information processing and analysis, better utilizing your operating hours.
-
Decreasing your costs makes way for greater profits. As you increase and improve your output, you can increase your profit margins, simplify staffing requirements and reduce the price of operations.
-
The optimized processes that come from an ICS aid in minimizing the resources required for creating products and contribute to more efficient management. With less waste, you don't need to spend as much time sifting through it or buying the materials that created the waste in the first place. Fewer errors also reduce the effort required to fix the problems or do damage control after these issues reach a customer.
-
An ICS contributes to product quality in many ways. It can monitor for quality or adjust processes as necessary. Industrial process automation can minimize human error, too, and support valuable product insights through analysis. With all the features of an ICS, you can greatly boost quality and enjoy the improved satisfaction, cost savings and reputational advantages that come from it.
-
Whether you have an ICS or not, a lot of data goes through your industrial facility. An ICS can collect and organize all of that data and create a centralized location for easy analysis and control. It also connects all the facility's systems, sensors and components for top-down visibility and control.
In industrial settings, automation has significant potential, and more businesses are taking advantage of that to stay competitive. The market as a whole is expected to rise at a compound annual growth rate of 8.9%, reaching $288.93 billion by 2028.
What are the types of industrial control systems?
Industrial control systems come in several varieties designed for different environments. Below are the different types of control systems available.
SCADA
A supervisory control and data acquisition (SCADA) system collects data from and controls equipment across multiple sites. Control occurs on the supervisory level, with PLCs, RTUs and modules distributed in different locations to collect and transmit data across long distances. They may be linked up with machinery, sensors or other types of equipment. Integrated HMIs send the data and humans oversee the incoming information. This process may be on-site or at another location and can include numerous inputs and outputs.
SCADA systems can range from simple to complex and are popular in industries like water and wastewater, power transmission and distribution, food and beverage, pharmaceuticals and automotive. A SCADA system relies heavily on a strong HMI platform to take advantage of an easy-to-use interface and extensive features that make data collection, visibility and efficiency easy.
DCS
A distributed control system is used at one location and works with setpoints, which are the target values for a variable or process. This system sends a setpoint to a controller that can move components like valves and actuators to maintain the desired setpoint. A DCS uses a centralized supervisory control loop to manage the devices as part of the overall production process. A DCS controls, monitors and organizes the many controllers used throughout a plant.
A DCS allows users to quickly access necessary data. Since many devices connect to it, it also minimizes the impact that any one fault can have on the overall ICS system. It is a popular choice for businesses in manufacturing, oil refinement, energy production and distribution and water and wastewater.
PLC
While programmable logic controllers are a key part of both of the above methods, they can technically function on their own. PLCs collect information from an input and process the data, initiating outputs based on the parameters given. They can again range from simple to complex.
Many PLCs have components built-in, but they could also take a modular approach to connecting to devices such as sensors, meters, lights, relays and valves. Other components that might be integrated or modular include the power supply and ports and protocols for communication with a SCADA or HMI system.
PLCs are common in industries such as distribution and manufacturing, including batch manufacturing. They can be used in one location or multiple. The primary drawback of using PLCs without an associated system such as a DCS or SCADA is the lack of centralized visibility and control. PLCs work locally and, on their own, don't communicate with other systems. The larger a business gets, the less viable a PLC-only approach will be. Still, they're a vital component of an ICS, providing the greater functionality of these systems.
How is an industrial control system set up and used?
Starting projects in an ICS provides greater control and efficiency in the future, as the project is engineered with the ICS and its structure in mind. An ICS has features that aid project planning and development, too. Walk through the process with the zenon Software Platform and see how it enables efficient engineering practices. The engineering phases of zenon include:
1. Conception
The first stage is to balance all the complexities involved in an engineering project, from quality standards to cost barriers and efficiency concerns. One requirement is a rapid proof of concept, which shows a design concept is feasible. This process may include experiments, pilot projects and testing. Engineers also need to consider the external compliance and compatibility requirements.
zenon helps by providing quick and user-friendly data generation for speedy initial testing, complete with a host of standard configurations and parameterization methods. It meets compliance requirements for DNP3, IEC 61850, IEC 60870 and others. zenon also has template components and samples to help you get started and develop your sample solutions.
2. Solution development
As you develop and implement your solution, efficiency starts gaining importance. Symbols, templates and object-orientation can help you create your energy solution faster. Templates allow you to save time by reusing components and minimizing learning time. They also make it easier to keep the project clean and organized while allowing for single verification and minimizing testing time.
Other valuable features include automation tools and configuration for existing functions. To make this stage smooth and straightforward, zenon offers features such as:
- Screen templates and symbols: zenon allows for easy visualization with different layouts for different tasks, including sequence of events (SoE) lists, switching sequence management and command processing. You can use generic screen symbols and assign dynamic variables and functions. Then, the symbol can be used in multiple assets in the HMI while the original symbol implementation stays centered in one spot.
- Smart Objects: With Smart Objects, zenon makes elaborate automation templates possible. You can use graphical symbols, variables, data types, drivers, command groups, detailed screens and interlockings to preconfigure a data model and attach alarms, functions and views to the template.
- Import/export mechanisms and defaults: Utilize robust import/export mechanisms and practicable defaults for greater efficiency and a more capable template environment.
- Configuration and parameterization: These features reduce complexity by allowing you to set essential parameters and help the rest of the solution fall into place. There's no need to develop or reverse-engineer custom code or use highly advanced programming skills. These resources can reduce errors from custom coding and retain standardized parameters for easy transfers while you develop the solution.
- Automation: Automated engineering can save time by offering easy visualization planning. With zenon's object-oriented engineering, for instance, you can create variables and custom wizards to conduct repetitive, standardized tasks. This ability allows you to minimize human error, standardize and boost efficiency.
3. Commissioning
In the commissioning phase, you need to know your solution can quickly scale up for large applications with all the right verifications in place. The standardization of zenon helps in this area with features like templates, building blocks and automated tools for custom algorithms and configuration wizards. When it comes to testing, you can see communication links and statuses within zenon and utilize process templates to avoid duplicate tests.
Another valuable component of commissioning is process simulation. This helps you prepare screens, perform first tests, control algorithms and optimize designs. zenon optimizes process stimulation by switching drivers to simulation mode, keeping variables on static values or animating variables dynamically.
4. Extension and updates
Efficiency in this phase helps ensure hands-off operation in the future. After finishing a project, you'll want to be able to update or extend the content, make agile changes to the project and extend architecture as needed. In zenon, the modular project architecture allows you to make changes and perform updates quickly and easily without affecting interdependent modules. The modular design means you can also add onto the architecture as needed with duplicate, specialized and templated modules.
The features of a strong ICS make long-term compatibility easy to come by, allowing for retrofits, updates and extensions long after the project is finished.
Implementing the right ICS with zenon
An ICS is a necessity for industrial environments, bringing clear visibility, control and data collection to various organizations. Because an ICS is such a foundational piece of the puzzle, you need one built by the experts. zenon by COPA-DATA is a powerful modular software platform that makes the most of SCADA environments and delivers benefits for efficiency, costs, data management and more.
Here at COPA-DATA, we've been in the business since 1987 and are continuously improving our platform to meet the industry's evolving needs. We utilize all the necessary logic and algorithms to keep your business moving. Reach out to us today to learn more about zenon and what the platform can do for your organization.