What is HMI?
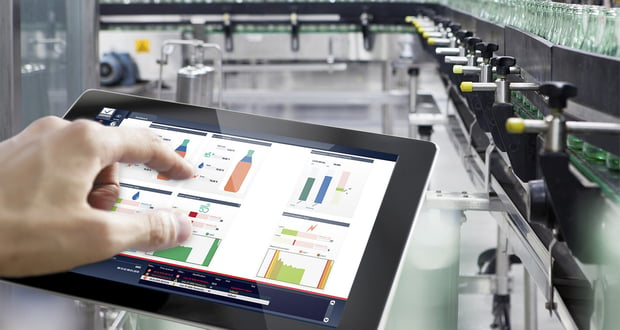
What is HMI? Advanced HMI let you easily communicate with machines and visualize operational data from across your equipment.
Industrial control systems continue to advance, and in today's world, the tasks operators need to complete can change frequently. To handle this complexity, you need flexibility and usability in your controls. That is the benefit of HMI. With an HMI based on zenon, you can easily communicate with machines and obtain operational data from across your equipment and facilities.
Human Machine Interface Definition
HMI stands for human-machine interface and refers to a dashboard that enables a user to communicate with a machine, computer program or system. Technically, you could apply the term HMI to any screen that someone uses to interact with a device, but it's typically used to describe such screens used in industrial settings. HMIs display real-time data and allow a user to control machinery using a graphical user interface.
What is the use of HMI? Take the example of a car. A car is a complex machine. The driver can control the engine, steering, lights, air conditioning, stereo and various other elements. You don't have to interact directly with each of these elements, though, to control them and get information about their operation. Your speed is displayed on your speedometer. You can control your stereo, lights and air conditioning with knobs and buttons or perhaps a touchscreen. To control the engine, you use the gas pedal, and to turn, you use the steering wheel. These controls and feedback instruments are like the HMI of the car. Now, imagine if you could control every aspect of your vehicle and get detailed information about its operation all on one screen. If you could, your car's dashboard would be even more like an HMI.
In an industrial setting, an HMI may come in several forms. It could be a standalone screen, a dashboard attached to another piece of equipment or a tablet. Whatever it looks like, its primary purpose is to allow users to visualize data about operations and control machinery. Operators could use an HMI to, for example, see which conveyor belts are on or adjust the temperature of an industrial water tank.
Uses of HMI
HMI sees use across a wide range of industries. It is common in manufacturing various types of goods, from automobiles to food and beverage to pharmaceuticals. Industries such as energy, water, wastewater, buildings and transportation may also use HMIs. Roles such as system integrators, operators and engineers, especially process control system engineers, frequently use HMIs. These professionals may use HMIs to control machines, vehicles, plants or buildings.
The sophistication of the HMI varies according to the complexity of the machine or system it's used for. It also varies according to how you plan to use the HMI. You might use an HMI for one function, such as monitoring a piece of machinery, or for multiple purposes, including monitoring plant operations and controlling equipment.
When your supervisory control and data acquisition (SCADA) system communicates with Programmable Logic Controllers (PLCs) and input/output sensors to obtain information about equipment operation, that information is displayed on an HMI. An HMI may display this information in a graph, chart or other visual representation that makes it easy to read and understand. With an HMI, you can view all of the performance information for a facility's equipment in one place, improving your visibility into your plant's operations. Operators can also view and manage alarms using an HMI, helping to ensure they can handle them quickly.
Operators can also use HMIs to control equipment to increase productivity or adjust to changing circumstances. They may make adjustments based on the data they view on the HMI. Being able to make the relevant changes right from the screen makes this process faster and easier.
As the Internet of Things (IoT) continues to play a more prominent role in industrial facilities, HMIs become even more useful. You can use them to view data about and control the various connected devices within your facility.
How to integrate HMI
HMI solutions can come in a variety of forms, from standalone terminals to tablets to dashboards integrated into other pieces of machinery. A facility may have one central HMI or numerous distributed ones, which may all be connected through the Internet.
Integrating zenon into your existing systems is easy, as it has more than 300 available communication protocols and works with a variety of systems. It's compatible with all major Microsoft Windows platforms and only requires the basic operating system to run. You can also access zenon using the Webserver or the HTML5 web engine. The web version of zenon has the same look and functionality, and any changes you make on a web client or HTML5 will update for all users, enabling you to work from anywhere.
With zenon, users can also set up their own dashboards by creating widgets and positioning them according to their needs. You can also lock and control the visibility of the elements of your HMI for security purposes and to create dashboards for different types of users. This enables you to create easy-to-use dashboards that only include the information relevant to each role.
You can also create various color palettes for your HMI, which allows you to customize dashboards that work for your corporate branding, particular lighting situations, as well as different teams and individual users (e.g. colorblind employees).
-
Benefits of using HMI: enhanced visibility, usability and efficiency using a unified system, with less downtime.
HMIs provide a number of benefits to today's industrial organizations, including:
- Enhanced visibility: A high-performance HMI gives you enhanced visibility into your operations at all times. It allows you to see how your equipment or facility is performing from a single dashboard. You can even view this dashboard remotely. These capabilities help you to improve productivity over time and respond to alerts more quickly.
- Increased efficiency: Because an HMI provides constant access to real-time data, you can use it to monitor production and adjust to changing demand in real time. Data visualization, especially when combined with data analysis technologies, can help you identify areas where you can improve the efficiency of your operations.
- Decreased downtime: With alerts on a central dashboard, you can respond to problems more quickly, reducing downtime. Viewing and analyzing equipment performance data can also help you to identify signs of future mechanical problems and address them before they escalate into issues that may cause significant downtime.
- Improved usability: HMIs make it easier for users to view and understand data and control equipment. They present data using graphs, charts and other visualizations, which makes it easy for users to interpret it quickly. With zenon, users can also customize their dashboards to fit their needs and preferences.
- Unified system: With zenon, you can control all equipment using the same platform, which makes it easier for operators to learn how to control equipment. You can also view all of your data in one location, helping you to get a clear overview of your entire facility. Additionally, all users get updates in real time, so your team is always on the same page.
Industrial HMI solutions by zenon
Human Machine Interface eBook:
All you need to know about the past and future of HMI systems
HMI and SCADA
HMI and SCADA are sometimes confused because of their similarities and the fact that they work together. In fact, an HMI is often a part of a SCADA system.
A SCADA system is used for controlling large systems, such as an entire plant or site. It is a combination of many other systems including PLCs, sensors and Remote Terminal Units (RTUs). A SCADA system is what collects and records data. It can also control equipment operations, sometimes automatically.
-
While the SCADA collects and stores the data, the HMI enables users to interact with the equipment by providing a user-friendly dashboard.
An HMI, on the other hand, is the interface that someone uses to interact with a SCADA system and other systems and equipment. They are both essential elements of the larger industrial control system. While the SCADA collects and stores the data, the HMI enables users to interact with the equipment and manage it by providing a user-friendly dashboard. They are both necessary. Without SCADA, an HMI would not have any information to show or be able to control equipment. Without an HMI system, users would not be able to see the data the SCADA system collects or tell it how to control equipment.
SCADA and HMI are part of the same larger system. SCADA works in the background, while HMI is typically the only element that users interact with. This is why users often reference them together.
Advances in HMI
Technological advancements and evolving business needs have resulted in changes in the functionality of HMI technology. Touchscreens, mobile devices, cloud-based HMIs and high-performance HMIs are becoming more common.
The term high-performance HMIs refers to an HMI design method that aims to draw user attention to only the most critical elements. This helps users to see and respond to issues more quickly and more easily gather the information needed to make decisions. The indicators on these types of HMIs are simple, and the dashboards don't include non-essential graphics and controls. Other design elements are used sparingly so as not to distract the user from the most important items.
In addition, advanced technologies like IoT and data analytics technologies are beginning to have more impact on HMIs. As more connected devices come online, HMIs can collect more data and become a part of the IoT network. Advanced data analytics techniques applied alongside HMI/SCADA software can help companies make the most of the data presented on their dashboards.
Multi-Touch
Touchscreens gained popularity with the rise of the smartphone, thanks in part to the multi-touch screen, which users can interact with using multiple touches and gestures simultaneously. This feature is now available in the industrial sector, with zenon representing the first HMI/SCADA that supports Multi-Touch gestures. With zenon's Multi-Touch functionality, you can use two fingers to zoom in and out, drag and drop screen elements and use other intuitive gestures.
Some of the benefits of a multi-touch HMI include:
- Enhanced operating safety: The intuitive control of the HMI means fewer errors. Multi-Touch also features two-hand operation, which means that users can't complete certain actions using only one hand. This feature helps avoid potentially costly and even fatal mistakes.
- Usability: zenon's Multi-Touch gestures are intuitive and comfortable to use. Rather than complex menu structures, you get user-friendly scrollable toolbars. It's easy for users to drag elements around and get the information they need.
- Reduced training time: The ease of use Multi-Touch provides helps to reduce training time. Users can learn how to use the system more quickly, and less experienced users can handle more projects safely and easily.
- Durability: With no moving parts, touchscreens can withstand harsh conditions better than keyboards, mouse devices and other controls may be. This means your equipment will last longer and work more reliably.
- Flexibility: With a touchscreen, process changes do not require rewiring a control panel. Instead, you can simply update your software. Users can also easily create their own custom dashboards based on their needs and preferences.
Remote monitoring
Another valuable feature of the modern HMI is remote monitoring. With zenon, authorized users can access dashboards and reports from anywhere over a browser. This means that you can check in on operations and complete operational tasks from a computer in an office, from a tablet at home or from a smartphone while on the road. Remote monitoring allows for supervision after working hours without having to be onsite and allows you greater control over your processes and enhanced access to your data.
-
You can check in on operations and complete operational tasks from a computer in an office, from a tablet at home or from a smartphone while on the road.
Future of HMI
As data takes on a more prominent role in industrial processes, HMI is bound to become even more important. The technology has made significant advancements in recent years but will continue to evolve into the future.
More companies are moving toward high-performance HMI, which helps draw users' attention to only the most critical information. This helps users make sense of all the data that's available and prevents information overload. Companies are also increasingly using multi-touch screens, remote monitoring and cloud-based systems.
As technology continues to evolve, companies will increasingly use advanced data analytics and artificial intelligence to derive insights from data. They can then communicate these insights to users via HMIs. In the future, HMIs may also incorporate augmented reality (AR), which overlays digital graphics on the real world, and virtual reality (VR) technology, which immerses users in a digital world, to create more effective visuals for HMI users. As automation continues to play a more central role in industrial processes, users can leverage HMIs to monitor automated activities and adjust them as needed.
zenon's high-performance HMI
When using zenon as an HMI/SCADA application, you get access to a high-performance human-machine interface that provides ease of use, enhanced situational awareness and intuitive control. zenon can provide you with easy-to-read visualization of relevant process data and alarms. Intuitive Multi-Touch functionality makes it easy to control processes safely, and remote monitoring capabilities mean you can observe and control your processes from anywhere.
zenon processes information live and distributes it to the relevant users while reducing complexity for operators. This enables your team to respond more quickly to issues that may arise and make more informed decisions. Users can also easily create custom dashboards so that they always have the information they need in the format they prefer. Because zenon is independent of the hardware used, you'll have a consistent system across numerous kinds of equipment, making it easier for operators to learn how to control machinery and view data.
With the advanced, user-friendly HMI/SCADA capabilities available with zenon, you can increase visibility in your operations and more easily control your processes. To learn more about the solutions COPA-DATA offers, contact us today.
Wir freuen uns über Ihre Fragen. Kontaktieren Sie uns einfach, wie es Ihnen am liebsten ist: