BMW Dynamics Center: zenon - realiable information flow, steady flow of goods (Germany)
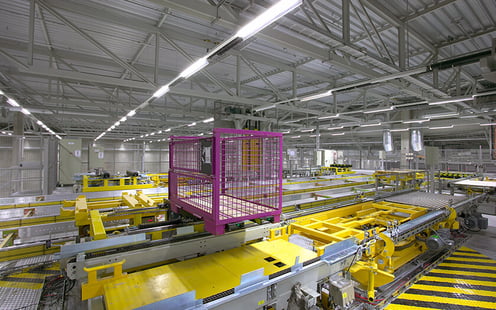
Modern commissioning and storage systems are the basis for quickly supplying a distribution structure with parts and accessories. The BMW Group uses its Dynamics Center in Dingolfing to ensure that all replacement parts are at the right place at the right time. zenon visualizes the materials handling from the receipt of goods through to the high bay warehouse.
The car manufacturer has created one of the largest replacement part warehouses in Europe with its Dynamics Center close to the BMW factory in Dingolfing. The building complex covers 153,400 m². Approximately 2,000 suppliers from around the world supply their goods to the central parts delivery center in Dingolfing. Each individual article is tested for quality, examined and stored. 3,700 dealers worldwide are supplied from the center. 55,000 transactions are made each day. The receipt and dispatch of goods requires up to 500 trucks and 60 containers each day, which are transported by train. Every year, goods with a total volume of 1.4 million cubic meters are moved.Parts for all types of cars and motorcycles are kept for 15 years. Around 260,000 articles are stored in the Dynamics Center. The cleverly thought-out logic enables all articles for Germany to be delivered overnight; it takes a maximum of 48 hours for the goods to be delivered to anywhere else in Europe.
High-tech storage with zenon
In order to be constantly competitive in the automotive industry, the central logistics and parts delivery center must always be as up to date as possible. As part of the most recent expansion, or rather refurbishment, of the Dynamics Center, the computers processing the flow of material were replaced with a Simatic S7-400 master controller. In addition, BMW also requested a new software solution for the process control level and operation of the control panels, of which there are currently 50. zenon came into play here. zenon from COPA-DATA displays all processes – from the receipt of goods, through internal movement, to dispatch. The solution thus enables the people operating it to know where a replacement part or accessory is at any time.
Two methods of transport, one solution
There are a total of 325 chain conveyors on the ground floor. The containers to be transported are placed on or transferred to defined locations on the chain conveyor by means of fork lift trucks. 11 lifting stations, 16 lifting tables, 6 rotary tables and 19 telescopic inverters connect the chain conveyor with the elements of the electric pallet conveyor. They also form the interface between the two levels and methods of transport. The telescopic inverters and lifter bring the skeleton containers with the objects being transported to the upper level, where they are transported by the electric pallet conveyor passed up to 63 four-way points and 7 rotary points to their destination. The electric pallet conveyor is the heart of the internal transport system and serves to bridge the very long distances in the Dynamics Center. It connects the areas for receipt of goods with pre-packaging, storage, order consolidation and final packaging. The electric pallet conveyor is approximately 6 meters above the facility floor. The conveyor system is 2,650 meters long in total. zenon visualizes the complete conveyor technology on both levels.
Focus on safety and flexible access
Visualization and master control and therefore the overall flow of material are set up as a client/server system (web server) with a server and a redundant stand-by server. Reliable industrial computers with four 19” monitors and a RAID storage system provide additional security and also make a comfortable control room. This is because the employees particularly benefit from one of zenon’s features; during operation, the display resolution dynamically adapts to the respective monitor size completely automatically; in this way, the master control visualization
is currently displayed on different systems with 2560 x 2048, 1024 x 768 and 1680 x 1050 pixels. For safety, and to be highly accessible, zenon also has alarm management. Thanks to the reports from alarms and reports of events in the system, users are immediately made aware of all critical activity in the process. zenon comprehensively supports BMW maintenance staff in localization and rectifying any possible problems. “High availability and safety were important requirements for BMW. Just as important was flexibility and ease of access to all information at any location in this giant logistics center”, explained the software engineers at Staudinger GmbH.
A well thought-out flow of information
The master control, as well as the seven group controls, ensures that there is a continuous flow of information. The 50 control panels are not connected directly to the master control but instead they are connected to the seven group controls. These move the conveyor technology parts – lifters, invertors, chain conveyors and receive instructions for the respective switch settings, which are determined by means of routing tables, from the master control. The exchange of data between the master controls and group controls is recorded and stored in a database (Microsoft SQL Server). The database also runs on an industrial computer with high availability. zenon ensures that, thanks to the web client, the respective employees can access not only information from group controls but also information from the process control level.
Easy process control
The SCADA solution records the flow of goods and prepares the data for statistics. In this way, the operators always have an overview of stock levels and can estimate and analyze trends using previously recorded data. The information is saved in Microsoft’s SQL database. “Thanks to the easy to use VBA integration in zenon, it
is easy to access objects, variables and functions and also to set up user defined analyses – one of the many advantages which this software offers”, adds Markus März from Staudinger.
Simple planning, time-saving management
The previous solution had a deficiency that has now been put rectified: a separate, independent project was installed
on each direct control panel. Each addition and each change to an object therefore had to be carried out 50 times. Thanks to the integrated multi-project administration in zenon, it is possible to define projects centrally and to consistently generate or change all defined objects from one place; once defined, or changed, objects are available quickly and are error free. The possibilities for reusing these objects increase and the effort needed to
maintain these is drastically reduced as a result. Markus März also confirms this: “Planning is exceptionally efficient with this. This also means that the customer enjoys an enormous saving in time and cost during the commissioning phase and in particular thereafter, for instance when expanding or making changes to the facilities. I particularly liked the possibility in zenon to activate or deactivate the drivers for the different controls during operation. As a result, the data traffic on the network was reduced considerably for the customer.”
User-friendly solution, immediate implementation
With zenon, Staudinger has developed an application that is very intuitive and easy to understand. With the previous
solution, the employees in the Dynamics Center worked for over four years on the changeover; however the transition to the new solution was made with relatively little effort involved in training and also went very smoothly, despite the fact that the software was fundamentally different to the existing software. zenon offers a wide range of design possibilities for intuitive and yet demanding process images. One of the functions which made the quick transition to the zenon solution possible is the zenon worldview: the zenon worldview makes it possible to pan across very large images of facilities with the mouse or by using the touch panel. In addition, it is possible to zoom, and add or remove detailed information into the image at any zoom level – comfortably, clearly, efficiently.
Download
-
Success StoryBMW_Dingolfing_Dynamics_Center_SUS_EN.pdf