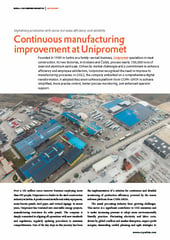
Continuous manufacturing improvement at Unipromet
Success Story
Founded in 1989 in Serbia as a family-owned business, Unipromet specializes in steel construction. Its two factories, in Kraljevo and Čačak, process nearly 100,000 tons of steel and aluminum each year. Driven by market challenges and a commitment to enhance efficiency and employee satisfaction, Unipromet recognized the need to improve its manufacturing processes. In 2022, the company embarked on a comprehensive digital transformation. It adopted the zenon software platform from COPA-DATA to achieve simplified, more precise control, better process monitoring, and enhanced operator support.
Now a 102 million euros turnover business employing more than 650 people, Unipromet is a leader in the steel construction industry in Serbia. It produces and installs road safety equipment, noise barrier panels, steel pipes, and vertical signage. In recent years, Unipromet has ventured into renewable energy projects, manufacturing structures for solar panels. The company is deeply committed to aligning all operations with new standards and regulations, regularly updating procedures to maintain competitiveness. One of the key steps in this journey has been the implementation of a solution for continuous and detailed monitoring of production efficiency, powered by the zenon software platform from COPA-DATA.
The metal processing industry faces growing challenges. This sector is a significant contributor to CO2 emissions and is under increasing pressure to adopt more environmentally friendly practices. Fluctuating electricity and labor costs, driven by global conflicts and market disruption, impact profit margins, demanding careful planning and agile strategies to maintain profitability. In this industry, digital transformation is still under-utilized, hindering process optimization and supply chain management. To remain competitive, manufacturers must increasingly turn to advanced technologies that enable more efficient operations. Addressing these challenges requires innovative approaches and strategic planning to ensure sustainable growth and long-term stability.
Unipromet’s manufacturing facilities involve complex processes that demand high levels of precision and efficiency to uphold quality and safety standards. Diverse equipment of differing ages and from a variety of manufacturers necessitates varied approaches to monitoring efficiency and conducting preventive maintenance. This complex manufacturing environment complicates Unipromet’s sales processes because it is difficult to clearly see the precise status of work through each stage of production – from procurement and manufacturing to delivery to the end customer.
Additionally, market demands call for cost reduction, energy consumption optimization and decreased greenhouse gas emissions alongside improved productivity. These requirements often place significant pressure on employees, negatively affecting their satisfaction and engagement. Outdated or malfunctioning equipment can lead to production errors, increased costs, and further dissatisfaction among employees.
To successfully address these challenges and ensure long-term stability, Unipromet has embraced digital transformation using the zenon software platform. This solution enables process standardization, centralized data collection, and significant efficiency improvements.
A production line for manufacturing noise barrier panels for roads, integrated into a monitoring system.
Main screen (dashboard) for all lines at the Čačak site.
At Unipromet, efficiency measurements relied on parameters and production-line statuses which were manually recorded, along with the operators' personal assessments of time spent on production, downtime, and fault resolution. These assessments were processed using a cumbersome administrative process and entered into the ERP system. Records were not precisely accurate but instead rounded to estimated times, relying on the operators to record accurately and free from subjective bias.
Even with these manual data collection methods, the recorded results highlighted unsatisfactory levels of production inefficiency. At the same time, information about factors which are essential for monitoring and improving Overall Equipment Effectiveness (OEE) were missing, including precise information about the main causes of downtime or other losses. Consequently, there was no way to identify, address or optimize causal issues. Additionally, accurate delivery planning for customers was hindered by the lack of reliable information about production lead times.
Unipromet began implementing a production process monitoring and management solution based on zenon to address the aforementioned challenges. The primary objectives were to improve process efficiency and effectiveness, enable detailed monitoring of all machine parameters, and collect data on downtime to better analyze bottlenecks. These insights would ultimately allow for the optimization of multiple processes, including activities before and after production, such as waiting for work orders or the availability of resources for internal transport and logistics.
With the support of the local system integrator, Automat, a successful pilot project on a relatively new line for profiling C profiles was completed at the end of 2022. This includes profiling, drilling, cutting, and robotic welding. The pilot project served to define the right steps in project development, the layout and arrangement of screen elements, and system functionalities. Following its successful completion, a broader implementation process began.
A detailed analysis of all machines in production determined the sequence in which the project would be rolled out. Over the course of the following year, the project encompassed a total of 14 different machines, with different PLC devices, across two locations in two cities. These included production lines for producing barriers, C profiles, sigma profiles, welded pipes, and noise protection panels, as well as longitudinal cutting lines.
The zenon software platform enabled the integration of these diverse machines from different manufacturers using a variety of communication protocols, including Modbus, Siemens S7 TIA and Siemens S7 TCP/IP. In this way, zenon proved to be an ideal solution.
The project operates in a multi-server configuration, where the zenon operator stations at the machines function as independent servers, collecting data directly from each machine. These local servers then forward the data to the main zenon server, located in the operational planning department. This centralizes all information, performs analyses, and generates reports that are tailored to user needs. On certain stations, operators can manually input data into zenon when it is not available through automated collection. They are also required to confirm alarms and record the causes of scrap, if it occurs.
Additionally, a VPN was used to connect the two locations. The zenon Smart Server with access for three users is in operation, allowing employees to access the project and SCADA system from the two production locations in Čačak and Kraljevo.
Unipromet now benefits from automated data collection and analysis directly from production lines. The system now provides real-time insights into machine efficiency and OEE, incorporating information on downtime, nonconformities and line performance.
Users can generate reports containing detailed information on the types and durations of downtime, presented according to the Pareto principle, as well as view data on nonconforming products.
Through zenon, production parameters are monitored daily, with reports automatically generated at 7am, 3pm and 11pm. The reports are then sent to plant managers and the production director. These reports offer management a clear overview of issues, such as production bottlenecks, enabling timely actions to optimize processes.
The zenon software platform supports Unipromet’s system for continuous improvement and World Class Manufacturing, including the key element of "focused improvement". Unipromet can now use zenon to analyze all collected data and define actions to eliminate identified losses. Data gathered through zenon highlights the primary causes of losses based on frequency and duration, presented in precise Pareto diagrams, making analysis significantly more efficient.
To ensure information is accessible and promptly shared with employees, the system is currently being expanded with the implementation of HTML5 client stations. These function as "Andon screens," displaying real-time status updates on large monitors in the production halls. This approach enables detailed recording of all downtime. Plus, efficiency and the current status of work orders are more easily tracked.
Shift report with production parameters and EE and OEE values.
Detailed view of Availability, Performance and Quality for a specified time period
The implementation of the zenon software platform by the system integrator Automat has brought significant improvements to Unipromet's operations. Automated data collection and centralized monitoring have reduced administrative time, enabling faster responses to potential issues.
“The implementation of the zenon software platform has not only enhanced the efficiency of our production processes but also improved working conditions for our employees,” says Nikola Bojović, Chief Operating Officer at Unipromet d.o.o. “This is essential for our continued development.”
Furthermore, optimizing production processes and reducing downtime has resulted in operational cost savings. At the same time, the precise monitoring of process parameters has ensured high product quality is maintained. The introduction of modern tools and reduced manual labor has increased employee motivation and satisfaction, positively impacting overall productivity.
The availability of detailed reports and analyses has enabled management to respond quickly to changes. Employees in production and maintenance now collaborate more efficiently, significantly reducing response times to production line downtime. The contribution to informed decision-making enables senior management to refine business strategies and further company development.
“The introduction of continuous improvement and OEE parameter monitoring with zenon has transformed our operations, elevating efficiency and productivity to an entirely new level. Within just one year, we initiated over 25 improvement projects, increased the total volume of production by approximately 10 percent and significantly improved working conditions,” reports Nikola Bojović. “This has led to higher employee satisfaction and the positive trend is continuing. In 2024, our total production volume reached a historic peak. This success demonstrates how critical digitalization and continuous improvement, powered by our use of zenon, are for achieving outstanding results and ensuring the sustainable growth of our company.”
Additionally, the planning, internal logistics and sales teams can now more accurately estimate when products will be ready for delivery to end customers. In case of any challenges, customers can be promptly notified of potential delays, enhancing their satisfaction and strengthening their trust in the company.
Pareto chart of downtime causes and durations.
The scalability and flexibility of the zenon software platform has empowered Unipromet to continue to expand its digitalized system and advance in all aspects of its operations. This system offers horizontal scalability – making it easy to include additional production lines and machines. It also offers vertical scalability through standardized integration with ERP and MES systems, where zenon becomes a central data source automatically synchronized with other business solutions.
In preparation for new standards and directives, Unipromet is also planning to implement an energy management system to monitor energy consumption. This will enable more efficient resource management and cost reduction. Additionally, data from the company’s own solar power plant, located on the roofs of the production halls and currently meeting 60 percent of Unipromet’s electricity needs, will be integrated.
With the zenon software platform as a reliable foundation for further digitalization with the support of Automat, Unipromet is poised to achieve stable growth and ensure market competitiveness by improving efficiency, optimizing resource management, and reducing its environmental impact.
The introduction of continuous improvement and OEE parameter monitoring with zenon has transformed our operations, elevating efficiency and productivity to an entirely new level. Within just one year, we initiated more than 25 improvement projects, increased the total volume of production by approximately 10% and significantly enhanced working conditions.
Success Story
Success Story
Wir freuen uns über Ihre Fragen. Kontaktieren Sie uns einfach, wie es Ihnen am liebsten ist: