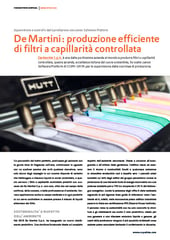
De Martini: Efficient production of capillary flow-control filters
Success Story
De Martini SpA is one of the very few companies in the world to produce capillary flow-control filters. This leading Italian company with sustainability at its heart has chosen the zenon software platform by COPA-DATA for the supervision of its production lines.
The capillary filters produced by De Martini can be found in every type of product which requires the precise control of the release of liquids through filters. Each time you write a perfect line, freshen a room with the ideal dose of fragrance or highlight your eyes precisely with eyeliner without smudging, you rely on small reservoirs of liquid that retain and release the liquid in a controlled manner. This is why De Martini capillary flow-control filters are needed in the fields of writing, cosmetics, room fresheners, medical devices and more.
In 2016, De Martini inaugurated a new production plant in Cerrione in the Italian province of Biella. The functional structure was designed with complete respect for the surrounding environment. Cutting-edge solutions and geothermal energy have been used to create a zero-carbon-impact building that is fossil fuel free and emission free. Solar panels installed on the building’s roof produce a significant amount of renewable energy. Together, they have an installed power of 700 kW and cover 30 percent of the plant’s energy needs. An office building was also built on the same site, according to the strictest environmental guidelines. It is the first industrial building in Italy to be certified by the Passive House Institute (PHI). The path to sustainability involves not only the buildings but also the site’s manufacturing activities. They have been redesigned to avoid generating or releasing liquid or gaseous emissions and to maximize the reuse of production waste as secondary raw materials and, in doing so, limit the amount of waste going to landfill.
At the Cerrione factory there are several production lines formed of different machines. They carry out the various stages of the process, such as cutting and packaging, and include a defect vision system based on high-resolution cameras for automated on-line quality control which covers 100 percent of the production operations.
For the supervisory application for the monitoring and control of production, De Martini turned to Motion Engineering S.r.l. in Biella. For more than 20 years, it has specialized in the development of motion control application software for high-performance machines. For this application, the partners chose the zenon software platform by COPA-DATA.
The technicians of Motion Engineering developed the automation software solution, including at PLC level and for the motion control system. To connect all the machines with the servers, they took full advantage of the excellent connectivity of zenon. zenon offers over 300 native communication drivers and open interfaces to connect to any type of hardware. zenon’s connectivity, performance and resilience is ideal to support the collection of the varied and large amounts of data required to populate De Martini’s supervision application.
Precise and detailed control of the line, with dynamic colors, dashboards and graphics that clearly show the status of the line, the availability and efficiency of production, as well as the defects and causes of rejects.
HTML 5 visualization of the status of the production lines. The indicators enable operators to see an overview of the production line trends without having to be close to the line.
The zenon-based solution presents an overview which enables the production managers and operators of De Martini to check the status of all the production lines at a glance, thereby enabling improved line management. It is possible to ascertain, both quickly and intuitively, whether there are any alarms, warnings or machines at standstill and whether everything is running normally.
Each line can be analyzed and managed individually. Performance dashboards and bar graphs can be used to analyze the overall equipment effectiveness (OEE) of each individual line and machine in real time. Operators can check for active alarms, see the batch in production, the number of rejects and the number of pieces produced, as well as the status of the machines. It is possible to remotely load the recipes, view historical trends with over 300 variables per line, and see the log of alarms and events.
Motion Engineering’s implementation of zenon enables the line operators to identify the causes of downtime, as well as to enter an "ideal speed" to be compared with the actual speed for each article and line. This way, they can calculate the uptime efficiency component of OEE.
The lines produce thousands of pieces per minute. Therefore, quality is a primary focus for De Martini, alongside its commitment to sustainability. Quality control relies on a computer vision system which interfaces in a fast and simple way with zenon. This provides information about the defects of any filters which have been discarded as well as the precise measurements of the non-compliant pieces. This enables operators to investigate the causes of inefficiencies and any defects in the pieces which mean the pieces do not comply with the specifications and are discarded. This data can then be saved and analyzed using different criteria, such as diameter or length compared to tolerance limits. The operators can refer to simple bar or pie charts to ascertain which defect occurs most frequently and consequently produces most rejects. The volume of rejects is analyzed with a view to continuously improving the performance of each line.
Laura Caprile, Head of Continuous Improvement at De Martini, explains, “Thanks to zenon we can easily and thoroughly investigate the correlations between the various parts of our production lines and the effects on the finished product.”
Two 50-inch monitors have been installed inside the plant. They use the zenon Web Visualization Service to show the status of the lines in HTML 5. Each monitor shows several lines simultaneously and in real time. The staff on duty is able to see, even from a distance, the status of the vision system by means of intuitive and easy to interpret indicators. They can immediately see whether it is working properly or in alarm mode and the current speed of the machines vs. the ideal speed. Staff can also see an instant analysis of the diameter and length of the filters produced by a given line to instantly understand whether they are within the previously defined tolerance limits and how close the current measurements are to the nominal value. These monitors greatly increase the ergonomics for the user because they no longer have to be near the production line to have a complete overview of operations.
Real-time monitoring and review of production performance is essential to implement corrective actions and continuously improve the performance of individual machines and entire lines, as well as to schedule maintenance activities that help avoid downtime.
zenon is used to assess the performance of the individual lines, filter by batch or by time, check downtime and its causes and obtain a complete list of alarms and events. Management can create specific and personalized reports based on role. They can filter by time or batch in order to investigate particular situations and their causes.
Every Monday morning, De Martini management automatically receives a summary report of the previous week for each line via zenon Message Control. The report was created using zenon Report Builder and outlines the production trends.
Each employee has different duties and therefore needs different information and they may prefer to view this immediately or in a weekly report. To enable this, dashboards and graphs indicate the production volumes, the ranking of the five main causes of downtime, and the five most frequent causes of rejection. All the staff involved, from the operators to senior management, can use these dashboards and reports to identify the best corrective actions to be implemented to continually optimize production performance.
Lucio Bonandini, owner of Motion Engineering S.r.l., concludes, "The use of zenon has proved crucial for collecting large amounts of data in real time, within as little as a few milliseconds. The tools that zenon makes available – including trends, alarm and event lists, and dashboards – already allow precise analysis. Plus, the platform has proved to be open to the development of custom controls and interfaces, which permit connection with the company’s ERP and MES systems.”
Thanks to zenon we can easily and thoroughly investigate the correlations between the various parts of our production lines and the effects on the finished product.
Success Story