Ergonomically monitored and efficiently controlled flour production at GoodMills (Austria)
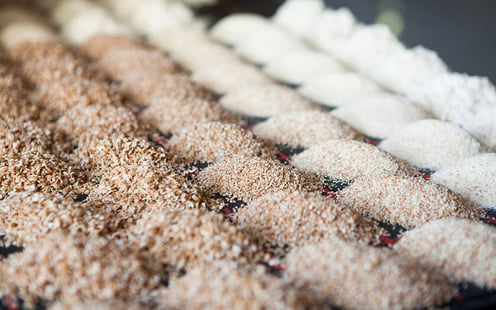
200,000 tons of grain are processed by the mills at GoodMills Austria for flour, semolina and brown-bread mixes. At two sites, control systems based on the HMI/SCADA software zenon from COPA-DATA ensure ergonomics, robustness and energy efficiency in operation. Installed there since 2003, the system always remains future-proof, thanks to ongoing further development. It also supports users to secure and increase their competitiveness.
Highlights
- One central control room per mill
- Complete connection of the control landscape by means of Profibus
- Data storage in zenon Historian
- Control of parameters with the zenon Recipegroup Manager
- Reduced energy costs due to needs-based control
- Location independence and improved ability to respond by means of mobile web clients
Organic food is fashionable. For a long time this has been the case not just in health-food shops, but also in leading supermarket chains. This is why the percentage of organic food out of the total produced in Austria has crept up to a two-digit figure – and continues to grow.
Rannersdorfer Bio-Mühle, south east of Vienna, has been processing only organic grain since 2012 with a stone mill. It is Austria's leading processor of organic grain and a part of GoodMills Austria, the largest milling group in the country, with 125 employees. It includes a large mill in Schwechat and a Farina mill in Raaba, Graz, which, in addition to flour, also produces durum wheat semolina for making pasta products. Founded in 1879, GoodMills Austria has been providing flour, semolina and brown-bread mixes under recognized brand names to bakeries, manufacturers of frozen products and the retail trade.
Flour production with efficiency and quality
"Flour and semolina are, as natural products, dependent on the quality of the raw materials. However, customers always expect a level of quality that remains the same, often in accordance with customer-specific requirements," explains Peter Stallberger. The foodstuffs technician has been with the company for over 20 years and is now the CEO of GoodMills Austria. "This quality – like the difference with products from other manufacturers – is barely detectable at first glance and, since the product is considered a mass-market commodity, its profit margins are low."
It is therefore important that operations are highly-efficient and largely automated, with the ability to guarantee consistently high product quality throughout the whole year. "The equipment at Bio-Mühle Rannersdorf runs in three-shift operation, six to six-and-a-half days a week, and constantly seven days a week in the run-up to Christmas," explains Stallberger. "We ensure the quality through strict incoming-goods checks, by discharging unwanted grains with a vision system and by controlling the composition of the separately-stored individual flours."
Transparent, reliable processes
Complete traceability of all processes is significant in the production of the food staples of flour and semolina. It must stretch right back to the contracted farmer in the case of organic products. "The ability to deliver is just as important as these quality criteria," Stallberger says. "Just one day of production downtime would be difficult to compensate for; any more than that would be a catastrophe."
In normal operation, a miller on the job monitors the complete operation of the mill. This includes all processes before and after the milling. This ranges from the unloading of the truck on delivery through to the storage, cleaning and sorting according to color, as well as drying the grain, through to the composition of different mixes, packaging and palleting and/or truck loading.
Reliability over many years
For efficient monitoring and operation, the mills in Rannersdorf and Raaba have been equipped with a comprehensive installation of the zenon HMI/SCADA system from COPA-DATA since 2003. It was implemented by an automation partner, upon whose services the mill managers at Rannersdorf and Raaba have relied since 1983, which now trades as KPS Automatisierungstechnik GmbH out of Lannach, near Graz. COPA-DATA's software system impressed us with its openness, which allows simple integration of various subsystems," said KPS CEO Walter Pummer. "Because zenon remains at the forefront of technological innovation thanks to continual further development, the HMI/SCADA system has now become an in-house standard."
"Before the introduction of the zenon-based HMI/SCADA system, there were only mimic diagrams at GoodMills, which enabled only a very rough overview of the electrical switchgear," remembers Stallberger. "The uppermost objective of the roll-out of this software was to make it easier for millers to monitor and control all processes in the mill."
Simple operation, integrated data storage
"zenon met these expectations in full, with visualization that is easy to understand and operation that is easy to learn," confirms Andreas Seidl, Operations Manager at Farina-Mühle in Raaba. "Furthermore, as a result of the data storage in the background – zenon Historian has already been implemented in Raaba – all recordings, such as lot tracing, which our colleagues previously had to do by hand, are now dealt with by the system."
The zenon software system continues to be developed. Since it was first launched, it has changed the working methods of the millers and delivered a huge improvement on the previous situation and considerably increased the robustness of the processes. Today, even very complex processes are controlled by means of the simple selection of recipes. These provide the appropriate parameters to individual items of equipment, connected via Profibus.
Cost-optimized with safety
Because the system constantly monitors the prescribed values during operation, it can intervene to control the interaction of individual parts of equipment and avoid blockages or downtime. "As a result of the optimization of all process stages with a quality of control that would be hardly possible manually, the HMI/SCADA system allows us to achieve high quality and high yield," Stallberger said. "This contributes considerably to the cost-effectiveness of the equipment as a whole."
The same applies to the reduction of energy costs. For example, the system enabled a needs-based control based on grain size that reduced the energy consumption of the vacuum conveying equipment by around 20%. The zenon-based automation was extended into the existing hydro-electric power station in Rannersdorf and the photovoltaics equipment constructed in Raaba in 2009, as well as an incineration plant for grain dust. The solution not only reduces the volumes of electrical energy purchased, but gives GoodMills the ability to generate the heat required in the building and to pass on surpluses to the district heating network.
Ergonomics in all operating situations
The control system has completely changed the everyday work of the millers, because they now monitor and control the equipment from a central control room at each site. In the event of major problems, which the miller on duty cannot resolve, the head miller intervenes in his capacity as the operations manager. From a computer at his workspace or from a mobile end device, he can review the situation at the plant and intervene directly.
"This allows our millers to intervene, using a tablet PC, even during an unmanned shift," explains Franz Egert, Head Miller and Operations Manager at Rannersdorfer Bio-Mühle, espousing the benefits of the web-based zenon user interface. "It gives you the option to carry out on-call duties from home and thus contributes to quality of life and motivation."
-
A comprehensive zenon-based system
revolutionized ergonomics and cost-effectiveness at two of our milling sitesPeter Stallberger | CEO of GoodMills Austria
Download
-
Success StoryGoodMills_SUS_EN.pdf