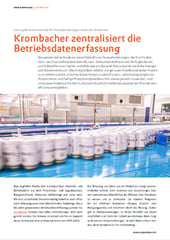
Krombacher centralizes its plant data collection (Germany)
Success Story
Breweries today face a number of challenges that impact their production and business processes, such as fluctuating prices and the availability of raw materials like hops and malt. In addition, breweries consume a lot of energy and water. As a result, it is increasingly important to accurately identify the cost of each individual bottle and to understand the source of these costs. At the same time, there are growing demands for sustainable production practices. To meet these challenges, innovative approaches are needed that support continuous improvements in production efficiency.
A filled beer bottle generates a considerable amount of operating data from production and logistics processes. This data can provide information about energy consumption, downtime, filling quantity, and much more. To ensure that you are managing this data effectively, you must be able to collect data efficiently and provide clear reporting. Krombacher's legacy systems were no longer meeting these high standards for plant data collection. The brewery decided to invest in a completely new system and, since then, Krombacher has been using zenon from COPA-DATA.
Collecting data from production has internal benefits for businesses. Good analytics and reporting can help companies measure and improve the efficiency of their machines. It provides forecasts for filling times for certain batches, including times for changeover or cleaning and, thus, make it easier to plan. Manufacturers are also required by law to carry out data reporting. However, the large volume of data collected can present a significant challenge. The more data collected, the more complex the reports are to prepare.
After 15 years, Krombacher's operational data system was no longer up to date and it required a lot of manual workarounds to prepare analytics and reporting. Additional data points had to be entered manually in Excel using Visual Basic scripts. It was not possible to prepare automated PDF reports or distribute data centrally. A separate application was available for visualization. However, it came with a downside: data had to be maintained and updated separately in this application.
Any modifications to the system also cost Krombacher considerable time and effort. The old system came from the equipment provider and it was configured specifically for the filling machines. This customization quickly became an obstacle as soon as modifications became necessary. Changes were not easy to make and, in some cases, Krombacher was unable to make the adjustments itself. It was also hard to implement other machines, such as compressed air stations or energy systems, because the system and its operation were configured specifically for filling lines. “When our last service provider ended support after 15 years and the server landscape was so outdated that it no longer ran on the current Windows systems, we decided to change systems,” says Marc-Philipp Böttler, Head of Operations & Engineering at Krombacher.
Krombacher elected to work with the system integrator Actemium, which introduced the zenon software platform from COPA-DATA. One reason for this was that the new system would no longer focus strictly on filling. From the malt grain to the filled and packaged bottle, the process steps needed to be as efficient and transparent as possible. Until that point, the machines in the brewhouse, cold area, filling, and logistics at Krombacher ran on different systems. As a result, comprehensive reporting based on the data was only possible with considerable manual effort. Actemium's task was to standardize the scattered data collection activities and systems landscape, thereby making reporting easier for the customer. In addition, all the collected data had to be available centrally.
When selecting the new system, Krombacher deliberately opted for an open system, so that adjustments could be made independently. zenon also impressed with its graphical representation, clear visualization, and ease of use – in other words, a central data hub that can be customized as needed and still functions as an off-the-shelf solution. Additionally, zenon provides an important interface to Krombacher's main tool for Business intelligence (BI).
The new can filling line installed during the project phase operated as a pilot project. Ralf Kirchner, Project Engineer at Actemium, explains, “The new can filling line served as a pilot project for us as it was installed during the project. One advantage of this was that it meant that there was no legacy data that needed to be integrated. This allowed us to develop the structure of the system from scratch.”
However, transferring the system to other lines and areas brought with it some challenges. Ralf Kirchner adds, “The existing equipment filled bottles, not cans. This meant that to extend the system we had to implement additional steps and update symbols. This rework took a lot of effort.”
zenon now runs on twelve lines, each with several machines. More than 262 programmable logic controllers (PLCs) for mash tubs, fermentation tanks, or labeling machines are connected. Approximately 230,000 variables are recorded and evaluated in more than 350 reports. A connection to the SAP ERP application enables the customer to query upcoming planned orders and send tax-related numbers. Moreover, forecasts can be calculated from the data, for example, for the running times of individual batches or for changeover or cleaning times or the recording and comparison of measured and target values.
“We really appreciate the open system and its benefits. It gives us flexibility when purchasing and connecting new machines from different manufacturers. We can make minor adjustments ourselves and thus respond more quickly to trends,” says Marc-Philipp Böttler. “zenon is not just a system for collecting operating data. It also supports control and visualization. This will lead to new synergies that we can leverage in the future, for example, in logistics.”
Despite digitalization and advancing automation, people remain an essential factor in the success of this type of project. “What good is the most modern technology, if it is not accepted by the people who are supposed to use it?” says Thomas Will, who is responsible for automation at Krombacher. “Fortunately, we were able to count on an experienced team.” Involving employees early on is important because it helps to develop acceptance for new systems and, thus, ensures the project will be successful.
Actemium and Krombacher are currently working to make sure that even more data can be collected, evaluated, and presented in visual formats in the future. A large part of the production costs should be determined automatically and evaluated on a batch-specific basis. For this purpose, the production process from malt grain to finished pallet has to be retraced using a batch tree. There is also further potential for visualizing the actual processes in filling and logistics – this could include the time remaining for the current batch until switching to the next product. Root cause analytics are also in development. In the future, automated reports will identify the machine in the production facility that actually caused the downtime. This will help to identify potential for increasing overall equipment effectiveness (OEE).
We really appreciate the open system and its benefits. It gives us flexibility when purchasing and connecting new machines from different manufacturers. We can make minor adjustments ourselves and thus respond more quickly to trends.
Success Story
Wir freuen uns über Ihre Fragen. Kontaktieren Sie uns einfach, wie es Ihnen am liebsten ist: