Merck modularizes its process development (Germany)
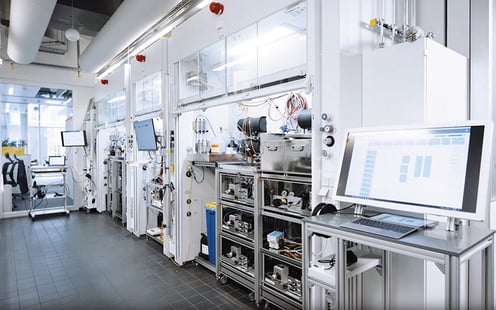
In the chemical and pharmaceutical industry, product lifecycles are becoming shorter and shorter. Merck KGaA was looking for a new solution that would make it easy to create and update system configurations and rapidly upscale from the laboratory to production. With zenon, the technology company was able to roll out modularization according to MTP standards in a higher-level Process Orchestration Layer (POL). This flexible application of modules is accelerating time to market considerably.
Highlights
- Accelerate time to market
- Cost savings thanks to faster development times
- Flexible system configuration using orchestration
- High rate of reproducibility for trial setups
- Rapid upscaling from laboratory to production
- Lab technicians do not need any programming skills
How can we bring new products to market as quickly as possible? This process development question is important for Merck. The leading German science and technology company is active in the healthcare, life sciences and electronics sectors. To optimize its process development and achieve faster time to market, Merck decided on a completely new approach: modularization based on Module Type Package (MTP) standards. "At first we didn't even consider MTP because the technology was still in its infancy. COPA-DATA convinced us to test the MTP/POL standard on a pilot project. After half a year, we were won over, and we applied our initial experiences to the main project," states Manfred Eckert, Associate Director Process Development at Merck.
Dynamic solutions require great flexibility
Merck's laboratory facility contains some 120 fume hoods equipped with lab equipment such as pumps, stirrers and dosing modules. In the past, trials with the different modules were carried out either manually or using a conventional laboratory management system. The frequent reconfiguration of the lab setup called for a major investment of time and resulted in high costs. "Nowhere else is such a dynamic environment found as in the laboratory. Trials are set up there almost every day. Modular automation has tremendous potential, particularly in this sector," states Christof Franzke, Senior Technical Consultant Key Accounts at COPA-DATA.
After successfully completing the pilot project, Merck and COPA-DATA began automating 60 fume hoods with the related process modules in a new lab facility. MTP interfaces were created for the individual devices. This is a prerequisite for the subsequent automation and orchestration of the modules via POL. The module profile in process development is very small. MTP provides a major benefit here as well because a range of control systems in differing scales can be used to produce the necessary interfaces, whatever the hardware or its manufacturer. As a result, not every module has to be equipped with an expensive PLC.
Plug & Produce for laboratory personnel
The orchestration sheet is used to plan and visualize networks of individual machines and services.
The goal was to ensure that lab technicians do not need to have any programming knowledge in order to add the modules needed to their trial setup. This approach provides the greatest possible flexibility and saves considerable time. The functionality and principle of MTP can be compared to a printer driver. The driver software is included in the delivery scope with the printer. This allows it to be connected to any PC and controlled without any further programming. Services such as printing or scanning can be actioned immediately after connection thanks to the "plug and play" approach. "Plug and Produce" in the process industry comes directly from this idea. MTP technology enables users to assemble, orchestrate and operate a production system based on several process modules very quickly and easily. The modules have their own intelligence, so that they only need to be connected to the network to be operated from the POL. No further programming is necessary. The system configuration can be quickly changed and adapted to the appropriate process at any time. Communication is supported by the OPC UA open communication protocol.
High rate of reproducibility for trial setups
Individual modules for recipes are orchestrated and managed by zenon Batch Control.
In addition to ease of use, flexibility and a faster time to market, modular automation provides a further benefit for process development: high reproducibility of individual trial setups. This is because the POL is doing more than managing and visualizing the trial setup based on the recipes. Data from the trial can be recorded and reported with the zenon Report Engine. Once a development process and a specific recipe have been defined, the manufacturing process can be reproduced again and again using the same framework parameters. This saves the lab technicians from having to manually document the defined parameters and also facilitates documentation and quality assurance.
Agile project management to develop a POL
The rollout of modular automation and integration in the POL took place over just two years. "For a project like this, that is an exceptionally short time," states Manfred Eckert. "Our collaboration was characterized by a high degree of agility. After all, until that point, no POL had previously met Merck's requirements. We only developed this in the course of the project."
It was not only the tight timeline that posed a major challenge for the project participants. In parallel to the rollout of the MTP technology, a new IT infrastructure was implemented at Merck. The aim was to set up the IT close to production. This was intended to meet the security requirements in production and guarantee round-the-clock availability. The POL was embedded directly in the new IT infrastructure. In addition, there were updates to the VDI/VDE 2658 standard at the same time, which had to be taken into account when implementing the project.
The further rollout of MTP is now planned at Merck in the US. Additionally, the newly automated processes can ensure such a high level of reliability that the processing facilities can run continuously, even overnight. This is an important advantage because, particularly when handling chemicals, safety risks have to be eliminated.
Leading the way into the future
"The zenon POL is one of the first POLs on the market with virtually end-to-end POL functionalities. We are pleased that we were able to co-develop the system and that we can use it for our process development from now on. It has been a joint journey with constant adjustments, changes and optimizations. We also plan to continue optimizing the POL together with COPA-DATA in the future," states Manfred Eckert.
-
For us, it is important that the technology supports a smart scale-up. Upscaling from the laboratory to production has to be quick and easy.
Manfred Eckert | Associate Director Process Development, Merck
More information:
- Merck Introduces Modular Automation for Laboratories – A First for the Chemical Industry
- Modular production / Plug & Produce
- Modul Type Package
Download
-
Bringing automation to the laboratory – with MTP standards and zenonMerck_SUS_EN.pdf