Simple parameterization, transparent visualization - zenon at AUDI AG (Germany)
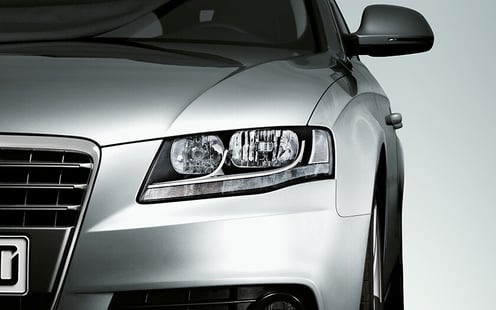
The base coating process at AUDI AG adds the first coat of paint to customized parts and specific standard parts. Reliability and high availability are of utmost importance, as the production processes that follow depend on the timely supply of all components from this section.
Base coating is a special coating process that is characterized by a smooth and accurate paint surface. Minimum error tolerance is a must. Cataphoresis* protects parts from corrosion and so-called ‘subsurface corrosion’. The components are placed on specifically shaped carriers and pre-processed in different baths (for degreasing, rinsing, bating, activating and zinc-phosphatization). The coating process that follows is also performed as an immersion process. The parts are coated by cataphoresis. The part acts as the cathode (negative pole) and the positive pole consists of anodes made of special materials; the dip tank is grounded. Following this, the paint is hardened in a convection oven. The customer parts and standard parts produced here then are sent directly to the assembly operation.
More information and greater production reliability
In order to achieve the increasing requirements for reliability of production, the control systems of the coating line had to be modernized. The most important goal was to collect and analyze much more information about the coating process. At the same time, the visualization of the line had to become easier to use and more intuitive.
zenon is always the right choice
The project team at AUDI AG analyzed, compared and evaluated a number of software tools. After the evaluation of several competitors, they selected zenon by COPA-DATA. Two of the reasons for this decision were the affordability of zenon and the feasibility of the required solution. With zenon, AUDI AG now has an open and platform-independent system that allows the use of any kind of hardware. Over 300 drivers guarantee compatibility with all PLC and bus systems on the market. This makes the customer completely independent and protects existing investments.
Project implemented as scheduled
For the implementation of the new logic, the production was supposed to be halted only during weekends. After that, all processes had to be restarted smoothly and reliably. This is why AUDI AG trusted Prozesstechnik Kropf from Oberkotzau for the implementation of the project. A reliable partner since 1992, this service provider has about 35 employees. Prozesstechnik Kropf is a professional full-service partner specialized on the design and implementation of automation solutions. Their focus lies on process control technology, energy management, data management, but also industrial switching systems. Prozesstechnik Kropf offers a wide range of services, ranging from consultation and implementation to training and reliable support.
The decision: zenon
AUDI considered two options for the modernization of the existing control equipment: the complete exchange of hardware and software or the exchange of CPU components only. Each option had its pros and cons. Costs, time and work effort required for testing and implementation opposed the positive effects like having new powerful components and an extended warranty for several years. “We chose to compromise, because the effort had to be in proportion to the result. The challenge was to exchange the central PLC and at the same time keep the existing I/O level, which was still up-to-date”, says Kurt Siebenwurst, responsible for automation technology in coating at AUDI AG in Ingolstadt. zenon is perfect for this, as it allows for the combination of different hardware components. The operation of the system has also become more comfortable. Changes do not necessarily have to be made on the shop floor; they can also be made in the control room. With a few mouse clicks, all the relevant information is presented to both line operators and to management.
Fast implementation
It only took three months from ordering to the launch of the new solution. “The time window was very narrow. As we were dealing with a very critical exchange of essential components and software, we needed a fall-back mechanism”, explains Werner Kropf, managing director of Prozesstechnik Kropf.
All customer requirements fulfilled
Prozesstechnik Kropf provided a continuous visualization for all processes in this paint line. The line consists of nine separate systems for the different stages (pre-processing, coating and drying), all of which are interconnected with each other, and the conveying system consisting of six cranes with part carriers (loading devices). Nine PLCs (Schneider Electric Quantum) deliver several thousand variables that are processed by zenon. The central control room consists of two servers in parallel operation.Besides the visualization for operating and monitoring the production processes, the automobile producer also wanted to be able to generate daily protocols of the base coating processes for reporting purposes. Such reports include information about the part carriers, the media consumed, different temperatures, conductance values etc. Kurt Siebenwurst explains, “We can operate and monitor these systems perfectly – even from the main control room. Any malfunctions are immediately recognized. Another positive side-effect: Thanks to the new control system, the part carriers no longer abruptly start moving. The mechanical strain on the drive mechanisms of the six loading devices was reduced to a minimum.” It was also important for AUDI AG to have an operational record that could be traced back at any time. With the modern zenon software solution, all events and manipulations of production process by users are automatically logged. The chronological event list (CEL) assigns a time stamp to every event. The line operators can look up a summary of collected information or forward it to colleagues or supervisors at any time.
Tools for efficient work
The next step for AUDI was to extend the existing solution. For example, the automobile producer uses the Industrial Performance Analyzer (IPA) by COPA-DATA to create informative and well-structured malfunction statistics. Additionally, the Industrial Maintenance Manager (IMM) is also in use today: this tool allows for the structured scheduling of maintenance tasks and the reproduction and documentation of already completed actions such as maintenance, repairs or replacements. Furthermore, it can be used to localize weak points and calculate error frequencies. The Industrial Maintenance Manager can store its data in any ODBC-compliant SQL database. These two zenon modules, IPA and IMM, significantly reduce downtime, avoid unnecessary repairs and facilitate the work of operators and maintenance teams.
* Coating bath and method for cataphoretic coating of metallic iron surfaces from aqueous solutions and/or aqueous dispersions of salts of cationic film-forming agents. An additional content of metallic ions from metallic salts is dissolved in the coating bath, the potential of which in the electrolytic voltage series of the cations (an ion that has a positive electrical charge and is attracted towards the cathode in electrolysis) is higher than the potential of the metal surfaces.
Download
-
Success StoryAudi_Ingolstadt_Base_Coating_SUS_EN.pdf