SMLC: Filling in the information for smart decisions (Lebanon)
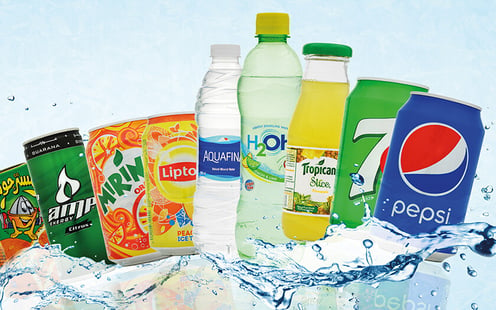
Producing a variety of beverages in glass and PET bottles, cans and cartons, PepsiCo partner SMLC is Lebanon’s biggest beverage bottling company. The implementation of a line management system based on zenon software from COPA-DATA put an end to manual data entry, providing comprehensive information for efficient filling operations.
Highlights
- Use zenon as filler/packaging line management system for SMLC
- Central system monitoring
- Elimination of manual data collection
- Comprehensive management information
- Fast line accumulation design validation
- High system stability, low memory requirement
- Fast creation of new and dynamic information charts without programming
The advent of household refrigerators, department stores and supermarkets in the nineteen-fifties changed market rules for drinks manufacturers such as PepsiCo. The makers of Pepsi Cola seized the tremendous worldwide growth opportunities presented by the consumer society. In 1952, they entered a co-operation with the Société Moderne Libanaise pour le Commerce (SMLC) in Beirut, Lebanon, who serves as bottler and distributor of the popular PepsiCo brands of soft drinks, iced tea, sports drinks, juices, energy drinks and water.
With ten filling lines for glass and stretch blow molded PET bottles, Aluminum cans and composite cartons, SMLC is the country’s biggest beverage bottler. The company has won several awards, most recently the Performance with Purpose award from PepsiCo International that recognizes the outstanding efforts made to reduce water and energy consumption.
A lack of transparency
Although SMLC’s packaging operations had generally always been quite efficient, production data acquisition and management information involved manual data recording using paper forms and spreadsheet software. As both production and maintenance staff has other work priorities and regard record-keeping a cumbersome side activity, reports were often inaccurate and sometimes contradicting. In some instances, they even reflected a desired status rather than actual reporting values.
Thus, the company started a modernizing initiative aimed at improving both quality and efficiency. This involved organizational changes, investment in state of the art production lines as well as the construction of new buildings. As part of this transformation, management decided to invest in software spanning all packaging lines. Its main purpose was to improve the information flow from the shop floor to the top floor to facilitate faster and better informed management decisions. It was also meant to provide the information required for the company’s clean in place (CIP) process.
Early attempts with humble results
SMLC awarded the contract for a pilot installation covering one bottling line to Teknologix. This team of industrial automation specialists based in Beirut enjoyed a favorable reputation from various automation and retrofitting projects they had successfully implemented for SMLC in previous years. Unlike European suppliers, they also did not need to include massive travel expenses for commissioning and after sales support in their proposal.
To reduce the amount of data to transport and process, Teknologix designed a system configuration using a PLC for each line to collect, concentrate and preprocess the information from the line’s individual stations. “Although we knew the concept was right and we spent many days and nights in a herculean attempt to fulfill SMLC’s requirements, we were not able to satisfy the customer”, admits Lucien Kazzi, founder and CEO of Teknologix. “The reason was that we were not using the right software.”
Although well-established process visualization systems from major global automation solutions suppliers and enriched with numerous add-ons and upgrades, the software products originally chosen failed to support many of the customer’s reporting requirements. “We needed to spend several months programming scripts to display Gantt diagrams based on the information within the system”, says Lucien Kazzi. “Reports were also slow, with a Gantt diagram taking two minutes to build up, they often failed to refresh and frequently crashed.”
Using the right software for better information
Several attempts were made using different platforms but none was able to satisfy all of the required criteria. In search of a better solution platform, Lucien Kazzi found that a leading supplier of filling technology and packaging machines was relying on the zenon software platform from COPA-DATA as an overall control system solution. “If this is right for them chances are it is what I am looking for”, he thought and decided to make contact with COPA-DATA.
This proved the right thing to do to rescue the project. zenon can be used out of the box, projects can be created with user-friendly graphical interfaces entirely by configuration without any programming. Lucien Kazzi confirms that using zenon was not only much easier than implementing the other system but generally much easier than expected. Consequently, Teknologix successfully completed the first line management system for SMLC only weeks after he took his first zenon training. “This was greatly helped by zenon’s highly flexible, dynamic reporting tools making it easy to create for instance quality reports, performance analyses or root cause analyses using pie charts or Pareto diagrams”, Lucien Kazzi says. “Another key to success was the excellent quality and fast response of COPA-DATA’s after sales support.”
A comprehensive solution
Using zenon, Teknologix implemented a comprehensive data acquisition and line management solution in a very short time. The automation experts used the experience gathered there to create templates so four more lines followed at a fast rate. The zenon-based system now spans five beverage production lines, one for returnable bottles, two with PET bottles and two with cans.
A long list of communication drivers enables zenon to communicate with machines from various manufacturers using different PLCs. Creating standard PLC blocks even allows integration of older equipment. The software’s optimized database structure reduces memory requirement for data storage as well as report loading time. While in the old system, data for one bottling line amounted to 500 GB per month, the zenon-based solution only requires 10 GB for a full year. Similarly, a Gantt view diagram builds up in two seconds as opposed to two minutes and it never crashes at all.
The implementation comes with dynamic reporting capabilities. While the previous system architecture had allowed only static time frames to be displayed, in zenon’s Extended Trend module these can easily be merged for comparisons and live trends can be displayed for real-time monitoring. The Gantt diagrams that had taken Teknologix more than two months to program in the software previously used, for instance, took only one hour to configure using zenon’s Extended Trend module.
A solid foundation for smart decisions
The zenon-based solution implemented by Teknologix has overcome the drawbacks of its predecessor and fulfills the requirements of the customer, who is considering future extensions such as predictive analytics. “The new zenon-based line management system has eliminated the need for manual entries and provides us with dynamic management reporting including quality reports, performance analyses, root cause analyses and time losses categories”, says Shady Khoury, Director of Operations at SMLC. “This gives us full transparency of our production and provides us with the information needed to make smart decisions based on solid foundations such as line accumulation design validations.”
-
The zenon-based line management system
gives us full transparency of our production
and provides us with the information needed to make smart decisions on a solid foundation.Shady Khoury | Director of Operations at SMLC
Download
-
Success StorySMLC_PepsiCo_SUS_EN.pdf