zenon - integrated assembly process at Volkswagen Emden (Germany)
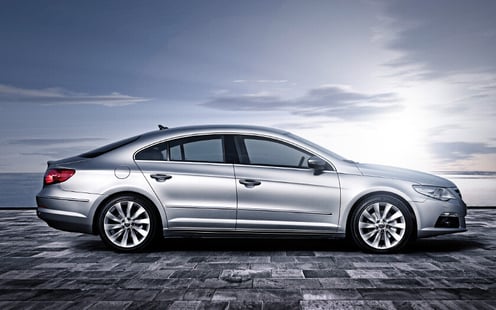
Production that is transparent down to the last detail and a well thought out material and production flow are the factors of success in automobile production – today and in the future. As one of the largest automobile manufacturers, Volkswagen masters these processes perfectly. zenon is part of the modern infrastructure at Volkswagen Emden and makes it possible to provide all process and production data consistently and transparently at any time in order to monitor, visualize and analyze manufacturing.
zenon is used at Volkswagen in Emden for the central monitoring of the whole assembly process. At the same time, the car manufacturer also uses the HMI/SCADA software from COPA-DATA for individual assembly processes. "We therefore looked for an HMI/SCADA solution that could meet our requirements for both visualization and process control, but also guarantee complete integration of all business and production processes. Production is dependent on information. zenon is a solution for all duties”, explains Mario Ewen, project leader for the introduction of the new super-ordinate visualization in the assembly area at Volkswagen Emden. One of the production stage that zenon provides visualization and analysis for is the application of adhesive onto the windows. This stage of the assembly takes place before the parts are assembled. During assembly, the interior – instruments, seats, trim panels, carpets, etc. – are installed, as well as the mounted parts - windows, windshield wipers, lights, wheels, etc.
Consistently automated
Previously, the windshields were delivered to the adhesion cell manually. Now, the windshield adhesive application facility at Volkswagen is largely automated. The company ATN Hölzel GmbH, a specialist for adhesive technology and automation, provided the new equipment for this assembly process and implemented the project in conjunction with COPA-DATA.
Today in the assembly department at Volkswagen Emden, there are a total of four windshield adhesive machines for the front and rear screens and the left and right side windows. In the windshield adhesive application process, the required window is initially brought to the equipment in pre-converted magazines. KUKA robots take the window out of the magazine and, after centering it, automatically guide it to the adhesive application tower, where the adhesive is applied. After this, the robots give the window to the ‘manipulator’, which transports the window to the installation point. At the installation point, the VW employees take the window using suction grips and place it into the vehicle, which will already have been transported in to place by the production line conveyor.
zenon – information that gives you the complete picture
All processes and information that are necessary for the operation and control of the equipment are displayed transparently using zenon – be it process statuses and values, equipment operating types, communication connections or status reports. The equipment and its components are shown in the overview screen. Starting from this screen, the user can switch into the different process stages. In the detail views, operators see, amongst other things, the individual cells – trolley cells or stacking column cells – in the same way that they can also see individual robots and their status data. In the detail views of the adhesion cells the user can, for example, set values, activate or deactivate sensors and tighten or loosen trolleys.
In the first process stage the robot takes the window out of the magazine and places it on the centering table. The window and its exact positional values are visible in zenon and the window can therefore be re-positioned for a perfect fit. For the adhesion process, zenon offers an overview of all status information and also the positions of the robots. This status information for the adhesive process includes the amount of adhesive applied, the pressure in the dose feeder, target revolutions etc. In this process the twin barrel pump transports the adhesive or sealing mass through pipes in the dose feeder, which supply the nozzles with the adhesive mass for the job. Here, all data on air pressure, temperature and fill level is visible. The manipulator, which travels with the line, takes the corresponding window and brings it to the vehicle. All positional values of the manipulator and robots are always available to the workers. They can not only adapt these values, they can also trigger subsequent actions.
The alarm management always provides the necessary safeguards in the operation of the facility and ensures that the VW employees react immediately where necessary. Equipment down times are therefore a thing of the past.
"zenon has proven itself in use at Volkswagen Emden. We implemented integrated visualization of the equipment which provides central monitoring of all of the assembly lines. In addition to a well thought out implementation of the project, and the well-engineered technical solutions that we use today, COPA-DATA particularly stood out because of the commitment of their employees – be it during the project preparation and implementation or in the support and training they deliver," explains VW project leader Mario Ewen.
zenon – An integrated flow of information ensures complete integration
The outstanding advantage of the zenon application is the direct connection to the Manufacturing Information and Control system. This system is used throughout the Volkswagen factory, in order to control material flows for automobile production and to forward production-related information to the production lines. Worldwide, the Manufacturing Information and Control system automates the supply chain in the Volkswagen factories and controls the supply chain extremely effectively. The solution has been used since the middle of the 1990s and records all necessary data on each individual car that Volkswagen produces. This includes the job, the specification details, the serial numbers of individual components as well as recorded production times or production sequences. In addition, it provides information such as throughput times, adherence to deadlines, utilization of capacity and order status information. The direct connection between zenon and the Manufacturing Information and Control system makes it possible that all relevant product information is available in the window assembly line too. Thanks to the display of the production line that zenon provides, the workers can gain an overview of which vehicle or model – Passat Variant, Passat CC or Passat Limousine – is the next to arrive on the production line conveyor. The window that is to be installed also arrives, precisely cycled, at the desired time and in the correct sequence.
The connection to the Manufacturing Information and Control system is created as a sub-project in zenon. This makes it possible to use this connection universally for other applications too, at low cost and with only small adaptations.
"When choosing the new solution for the visualization and monitoring of manufacturing, the standard connection to our Manufacturing Information and Control system was decisive", stresses project leader Mario Ewen. Until this development, programmers had created individual applications for each interface and connection to the group-wide Manufacturing Information and Control system. Mario Ewen continues "Today we benefit from the standard connection between zenon and the Manufacturing Information and Control system, which is available to us for use with further applications in Production. This reduces the planning and maintenance costs considerably, just as it does the deployment time and costs." The fact that the person in charge of the project, Mario Ewen, and his colleagues at Volkswagen are satisfied - and that zenon has risen to meet all their requirements in full - is evidenced by the most recent activities at Volkswagen Emden. Building on the facility-wide production monitoring and visualization of the new window equipment, the automotive group is now implementing further projects with COPA-DATA’s HMI/SCADA solution: in the future, Volkswagen will also rely on zenon for visualization and control of the tire equipment and the filling of coolant and brake fluid.
Volkswagen Emden – facts and figures
The Volkswagen factory in East Friesland employs around 8,800 people and is the largest industrial employer in the region. Volkswagen can produce 1,250 vehicles a day in Emden: in total, the company has produced over 9.5 million vehicles up to now in Emden. The factory is supplied with parts from around 660 suppliers. In the initial years after the factory was founded in 1964, Volkswagen manufactured the Beetle there. Since 1977, the Passat has been built in Emden. Since then, several generations of the Passat have been manufactured there. Emden is the leading factory in the world for this successful model. The sixth generation of the Passat Variant was put on the market in August 2005. In November 2007, Volkswagen produced the 15 millionth Passat worldwide in Emden. 2008 was the launch year of the new Volkswagen model, the Passat CC, which - just like the Passat Variant - will be exclusively produced in Emden.
The author of the article is Axel Netuschil, Product Manager at COPA-DATA GmbH in Cologne (www.copadata.de).
Download
-
Success StoryVolkswagen_Emden_Assembly_Windshields_SUS_EN.pdf