Sistemas de control industrial
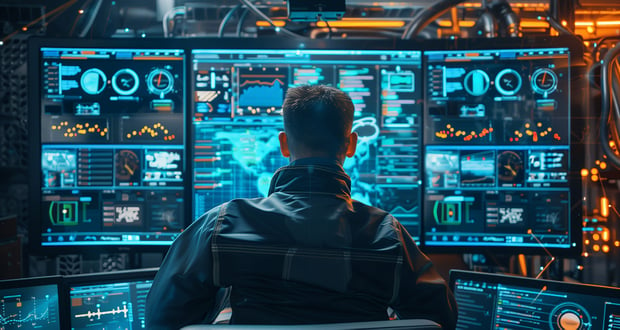
Los sistemas de control industrial (ICS) son una parte esencial de muchas organizaciones, suministran controles automatizados para una amplia gama de componentes en múltiples centros. Los ICS están disponibles en varios tipos diferentes y son compatibles con una enorme cantidad de elementos de diversas operaciones, desde la energía hasta la fabricación de productos farmacéuticos. Ofrecen beneficios en cuanto a eficiencia, calidad, análisis y, por supuesto, su balance final.
Veamos más de cerca los ICS y lo que pueden ofrecer a las operaciones industriales.
¿Qué es un sistema de control industrial?
Los sistemas de control industrial manejan diversos componentes, como dispositivos de monitorización y sistemas de software para gestionar operaciones y automatizarlas en la medida de lo posible. Equilibran los muchos componentes necesarios para operar un entorno industrial, garantizando que dichos componentes funcionen de manera eficiente y en sincronía entre sí. Un ICS puede tomar el control por completo o ser parte de un enfoque híbrido que incorpore la interacción humana. Están disponibles las opciones de bucle abierto, bucle cerrado y manual.
Si tu organización industrial está relacionada con el Internet de las Cosas Industrial (IIoT) u otros sistemas inteligentes, un ICS te resultará especialmente útil y minimizará los riesgos de seguridad. En general, los ICS proporcionan una mayor visibilidad y un control sencillo de redes complejas de componentes. Entre los elementos que puedes encontrar dentro de un ICS se incluyen servidores y controladores como:
- Unidad terminal remota (RTU): una RTU es un dispositivo de campo que se comunica con una unidad terminal maestra y funciona como un controlador de supervisión.
- Interfaz humano-máquina (HMI): con una HMI, los humanos pueden interactuar con el hardware que controla la maquinaria. La HMI suele ser una interfaz gráfica de usuario (GUI) que crea una plataforma legible por los humanos, en esencia, un software. Los usuarios pueden visualizar estados actuales, monitorear puntos de referencia, recibir alertas de seguridad, ajustar parámetros y algoritmos, evaluar datos históricos y mucho más.
- Controlador lógico programable (PLC): omo uno de los controladores de un ICS, un PLC permite gestionar procesos locales o conectarse a una HMI. También puedes visualizar controladores de automatización programables (PAC), que son similares a los PLC, pero suelen ser más avanzados y pueden incluir más memoria y flexibilidad de programación junto con características adicionales.
- Soft PLC: los PLC también se pueden encontrar en una base de datos centralizada, alimentada por datos procedentes de la línea de producción. Por ejemplo, zenon Logic ofrece un entorno de PLC integrado al que los ingenieros pueden acceder a través de una base de datos compartida. Solo necesitan crear objetos una vez y pueden acceder a ellos repetidamente en el sistema.
- Servidor de control: este servidor aloja el software de control de supervisión para un PLC o un sistema de control distribuido (DCS). También puede comunicarse con dispositivos de control de nivel inferior.
- TI y tecnología operativa: diferentes dispositivos, como sensores, monitorizan las operaciones de campo.
- Bucle de control: un bucle de control tiene diferentes tipos de hardware, como PLC y actuadores, que interpretan señales de sensores, interruptores, disyuntores, válvulas de control y más. Después, envían la información a un controlador para realizar una determinada tarea.
- Sistema de mantenimiento remoto: este sistema puede monitorizar y detectar anomalías o fallos y, en algunos casos, también introducir medidas para evitar problemas.
- Unidad terminal maestra (MTU) o servidor SCADA: la MTU o el servidor de control, supervisión y adquisición de datos (SCADA) pueden enviar órdenes a RTU en el campo.
- Dispositivos electrónicos inteligentes: un dispositivo inteligente puede recopilar datos y comunicarse con otros dispositivos. Con infraestructuras de SCADA y DCS, estos dispositivos pueden ejecutar controles locales automáticamente.
- Historial de datos: los datos recopilados del ICS y su entorno operativo se almacenan en un historial de datos y se exportan a otro sistema de información. En él, se puede procesar para realizar más análisis y trazar estrategias.
Los beneficios de los sistemas de control industrial
La automatización industrial por medio de un ICS tiene una serie de ventajas para las organizaciones industriales. Algunos de los beneficios de los sistemas de control industrial son los siguientes::
-
con menos requisitos manuales y una mayor productividad, un ICS te ayudará a aumentar la eficiencia. Podrás reducir las operaciones manuales y el uso de energía. La funcionalidad 24/7 de un ICS es una excelente manera de disfrutar de la automatización las 24 horas del día o utilizar el tiempo de inactividad para procesar y analizar la información, aprovechando mejor las horas de funcionamiento.
-
reducir tus costes te permitirá obtener mayores beneficios. A medida que aumenta y mejora tu producción, puedes aumentar tus márgenes de beneficio, simplificar los requisitos de personal y reducir el precio de las operaciones.
-
los procesos optimizados que provienen de un ICS ayudan a minimizar los recursos necesarios para la creación de productos y contribuyen a una gestión más eficiente. Reduciendo el desperdicio, no necesitarás pasar tanto tiempo revisando o comprando los materiales que dan lugar a dicho desperdicio. La reducción de los errores también disminuye el esfuerzo requerido para solucionar problemas o controlar los daños después de que dichos problemas lleguen a un cliente.
-
un ICS contribuye a la calidad de los productos de muchas maneras. Puede monitorear la calidad o ajustar los procesos según sea necesario. La automatización de procesos industriales también puede minimizar los errores humanos y poner a disposición información valiosa del producto a través de análisis. Con todas las características de un ICS, puedes aumentar en gran medida la calidad y disfrutar de una mayor satisfacción, ahorro de costes y las ventajas de reputación derivadas de todo ello.
-
ya tengas un ICS o no, por tu instalación industrial pasa una gran cantidad de datos. Un ICS puede recopilar y organizar todos esos datos y crear una ubicación centralizada para facilitar el análisis y el control. También conecta todos los sistemas, sensores y componentes de la instalación para una visibilidad y control de arriba hacia abajo.
En los entornos industriales, la automatización tiene un potencial importante y cada vez más empresas están beneficiándose de ello para mantener su competitividad. Se espera que todo el mercado crezca a una tasa de crecimiento anual compuesta del 8,9 %, alcanzando los 288.930 millones de dólares en 2028.
¿Qué tipos de sistemas de control industrial existen?
Los sistemas de control industrial están disponibles en diferentes variedades diseñadas para distintos entornos. A continuación se muestran los diversos tipos de sistemas de control disponibles.
SCADA
Un sistema de control, supervisión y adquisición de datos (SCADA) recopila datos y controla equipos en múltiples centros. El control se produce en el nivel de supervisión, con PLC, RTU y módulos distribuidos en diferentes ubicaciones para recopilar y transmitir datos a largas distancias. Pueden estar vinculados con maquinaria, sensores u otros tipos de equipos. Las HMI integradas envían los datos y los humanos supervisan la información entrante. Este proceso puede realizarse in situ o en otro lugar y puede incluir numerosas entradas y salidas.
Los sistemas SCADA están disponibles en distintos niveles de complejidad y son populares en los sectores industriales del agua y las aguas residuales, la transmisión y distribución de energía, los alimentos y bebidas, las farmacéuticas y el sector automotriz. Un sistema SCADA se basa en gran medida en una sólida plataforma HMI para aprovechar una interfaz fácil de usar y amplias funciones que facilitan la recopilación de datos, la visibilidad y la eficiencia.
DCS
Los sistemas de control distribuido se utilizan en una ubicación y funcionan con puntos de referencia, que son los valores objetivo de una variable o proceso. Este sistema envía un punto de referencia a un controlador que puede mover componentes, como válvulas y actuadores para mantener el punto de referencia deseado. Los DCS utilizan un bucle de control de supervisión centralizado para gestionar los dispositivos como parte del proceso global de producción. Los DCS controlan, monitorizan y organizan los diversos controladores empleados en toda una planta.
Un DCS permite a los usuarios acceder rápidamente a los datos necesarios. Puesto que muchos dispositivos se conectan a él, también minimiza el impacto que cualquier fallo tendría en el sistema ICS global. Se trata de una opción popular en empresas de fabricación, refinación de petróleo, producción y distribución de energía y agua y aguas residuales.
PLC
Si bien los controladores lógicos programables son una parte clave de los dos métodos anteriores, técnicamente pueden funcionar por sí solos. Los PLC recopilan información de una entrada y procesan los datos, iniciando salidas basadas en los parámetros especificados. Estos también pueden variar de simples a complejos.
Muchos PLC tienen componentes integrados, pero también pueden presentar un planteamiento modular para conectar dispositivos como sensores, medidores, luces, relés y válvulas. Otros componentes que pueden estar integrados o incluidos de forma modular incluyen la alimentación de energía y puertos y protocolos para la comunicación con un sistema SCADA o HMI.
Los PLC son habituales en industrias como la distribución y la fabricación, incluyendo la fabricación por lotes. Se pueden utilizar en una o en múltiples ubicaciones. El principal inconveniente de utilizar PLC sin un sistema asociado, como DCS o SCADA, es la falta de visibilidad y control centralizados. Los PLC funcionan localmente y, por sí solos, no se comunican con otros sistemas. Cuanto mayor sea una empresa, menos viable resultará optar por un enfoque únicamente con PLC. Aun así, son un componente vital de un ICS, pues proporcionan la mayor funcionalidad de estos sistemas.
¿Cómo se configura y utiliza un sistema de control industrial?
Iniciar proyectos en un ICS proporciona un mayor control y eficiencia en el futuro, ya que el proyecto está diseñado teniendo en cuenta el ICS y su estructura. Un ICS también tiene características que ayudan a la planificación y el desarrollo de proyectos. Descubre el proceso con la plataforma de software zenon y comprueba cómo hace posibles prácticas de ingeniería eficientes. Las fases de ingeniería de zenon incluyen:
1. Concepción
La primera fase consiste en equilibrar todas las complejidades que implica un proyecto de ingeniería, desde estándares de calidad hasta barreras de costes y cuestiones de eficiencia. Se requiere una prueba de concepto rápida que demuestre que el concepto de diseño es factible. Este proceso puede incluir experimentos, proyectos piloto y pruebas. Los ingenieros también deben tener en cuenta los requisitos de cumplimiento normativo y compatibilidad externos.
zenon te ayuda proporcionando una generación de datos rápida y sencilla para pruebas iniciales rápidas, completa con una gran cantidad de configuraciones estándar y métodos de parametrización. Satisface los requisitos de cumplimiento normativo de DNP3, IEC 61850, IEC 60870 y otros. Además, zenon también tiene componentes de plantillas y modelos para ayudarte a comenzar y desarrollar tus soluciones de muestra.
2. Desarrollo de soluciones
Para desarrollar e implementar tu solución, la eficiencia comienza a ganar importancia. Los símbolos, las plantillas y la orientación a los objetos pueden ayudarte a crear tu solución energética más rápidamente. Las plantillas te permiten ahorrar tiempo al reutilizar componentes y minimizar el tiempo de aprendizaje. También permiten mantener el proyecto limpio y organizado más fácilmente al tiempo que hacen posible una verificación única y minimizan el tiempo de prueba.
Otras características valiosas son las herramientas de automatización y la configuración para funciones ya existentes. Para que esta fase resulte sencilla y fluida, zenon ofrece características como:
- Plantillas y símbolos de pantalla: zenon permite una fácil visualización con diferentes diseños para distintas tareas, incluidas las listas de secuencias de eventos (SoE), la gestión de secuencias de conmutación y el procesamiento de comandos. Puedes utilizar símbolos de pantalla genéricos y asignar funciones y variables dinámicas. Después, el símbolo se puede usar en múltiples activos en la HMI mientras la implementación del símbolo original permanece centrada en un solo lugar.
- Smart Objects: Con Smart Objects, zenon hace posibles plantillas de automatización elaboradas. Puedes utilizar símbolos gráficos, variables, tipos de datos, controladores, grupos de comandos, pantallas detalladas e interbloqueos para preconfigurar un modelo de datos y adjuntar alarmas, funciones y vistas a la plantilla.
- Mecanismos de importación/exportación y valores predeterminados: utiliza mecanismos robustos de importación/exportación y valores predeterminados practicables para una mayor eficiencia y un entorno de plantilla más capaz.
- Configuración y parametrización: estas características reducen la complejidad al permitirte definir parámetros esenciales y ayudarte y ayudar a que el resto de la solución encaje como debe. No es necesario desarrollar o aplicar ingeniería inversa a un código personalizado ni contar con habilidades de programación altamente avanzadas. Estos recursos pueden reducir los errores de la codificación personalizada y mantener parámetros estandarizados para facilitar las transferencias mientras desarrolla la solución.
- Automatización: la ingeniería automatizada puede ahorrarte tiempo ofreciéndote una fácil planificación de la visualización. Con la ingeniería orientada a objetos de zenon, por ejemplo, puedes crear variables y asistentes personalizados para realizar tareas repetitivas y estandarizadas. Esta capacidad te permitirá minimizar los errores humanos, así como estandarizar y aumentar la eficiencia.
3. Puesta en marcha
En la fase de puesta en marcha, necesitas saber que tu solución puede ampliarse rápidamente para aplicaciones mayores con todas las verificaciones correctas. La estandarización de zenon ayuda en esta área con funciones como plantillas, componentes básicos y herramientas automatizadas para algoritmos personalizados y asistentes de configuración. Cuando se trata de pruebas, podrás ver enlaces de comunicación y estados dentro de zenon y utilizar plantillas de procesos para evitar pruebas duplicadas.
Otro componente importante para la puesta en marcha es la simulación de procesos. Esta te ayudará a preparar pantallas, realizar primeras pruebas, controlar algoritmos y optimizar los diseños. zenon optimiza la simulación de procesos cambiando los drivers al modo de simulación, manteniendo las variables en valores estáticos o animándolas de manera dinámica.
4. Extensión y actualizaciones
La eficiencia en esta fase ayuda a garantizar la operación sin necesidad de manipulaciones en el futuro. Después de finalizar un proyecto, querrás poder actualizar o ampliar el contenido, realizar cambios ágiles en el proyecto y ampliar su arquitectura en función de tus necesidades. En zenon, la arquitectura de proyecto modular te permite realizar cambios y actualizaciones de forma rápida y sencilla sin que los módulos interdependientes se vean afectados. Además, gracias al diseño modular, también puedes ampliar la arquitectura según sea necesario con módulos duplicados, especializados y plantillas.
Las características de un ICS fuerte hacen que resulte fácil lograr la compatibilidad a largo plazo, lo que permite modificaciones, actualizaciones y extensiones mucho después de que el proyecto haya finalizado.
Implementando el ICS correcto con zenon
Los ICS son una necesidad en los entornos industriales, ya que aportan visibilidad, control y recopilación de datos claros a varias organizaciones. Puesto que el ICS es una pieza fundamental del rompecabezas, necesitas uno diseñado por expertos. zenon de COPA-DATA es una potente plataforma de software modular que aprovecha al máximo los entornos SCADA y ofrece ventajas en términos de eficiencia, costes, gestión de datos y mucho más.
COPA-DATA lleva en este negocio desde 1987 y nos esforzamos constantemente por mejorar nuestra plataforma con el fin de satisfacer las necesidades del desarrollo de la industria. Nos servimos de todos los sistemas lógicos y algoritmos necesarios para mantener tu empresa en movimiento. Ponte en contacto con nosotros hoy mismo para obtener más información sobre zenon y todo lo que la plataforma puede hacer por tu organización.
Wir freuen uns über Ihre Fragen. Kontaktieren Sie uns einfach, wie es Ihnen am liebsten ist: