Sistemi di controllo di processo industriale
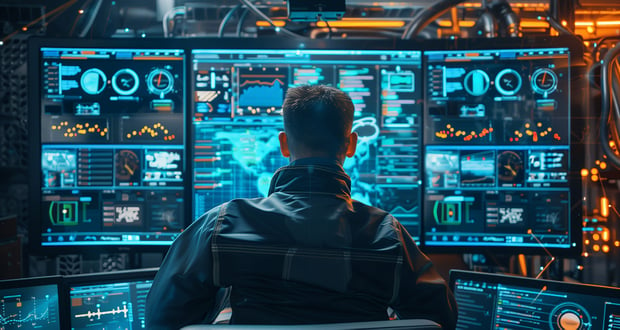
In quanto parte essenziale di molte organizzazioni, il sistema di controllo di processo industriale (abbreviato in ICS) esegue controlli automatici su un’ampia gamma di componenti in diverse sedi. Gli ICS sono disponibili in varie tipologie e sono in grado di supportare una molteplicità di elementi in diversi ambiti, tra cui quello energetico, farmaceutico e manifatturiero. Gli ICS offrono vantaggi in termini di efficienza, qualità, analisi e, ovviamente, fatturato.
Ma ora scopriamo di più sugli ICS e su come semplificano le operazioni industriali.
Cos’è un sistema di controllo di processo industriale?
I sistemi di controllo di processo industriale gestiscono vari componenti, ad esempio dispositivi di monitoraggio e sistemi software, al fine di eseguire operazioni e, quando possibile, di automatizzarle. Tali sistemi si occupano della gestione dei vari componenti necessari per operare in un ambiente industriale, garantendo che funzionino in modo efficiente e in sincronia. Un ICS può controllare autonomamente l’intero processo o prevedere un’interazione umana. Sono disponibili opzioni manuali, in anello aperto o chiuso.
Un ICS può risultare particolarmente utile nel caso in cui la vostra organizzazione industriale utilizzi sistemi intelligenti basati su Industrial Internet of Things (IIoT) o di altro tipo, poiché riduce i rischi per la sicurezza. In generale, gli ICS migliorano la visibilità e il controllo delle reti di componenti complesse. Tra gli elementi che potete trovare all’interno di un ICS vi sono i seguenti server e controller:
- Remote terminal unit (RTU): una RTU (unità terminale remota) è un dispositivo di campo che comunica con una master terminal unit (MTU) e funge da controller di supervisione.
- Human-machine interface (HMI, Interfaccia uomo-macchina): l’HMI, consente l’interazione con i componenti hardware che controllano il macchinario. L’HMI solitamente adotta un’interfaccia utente grafica (GUI) che genera una piattaforma leggibile all’uomo (un software) in cui gli utenti possono visualizzare gli stati attuali, monitorare i set point, ricevere gli avvisi di sicurezza, modificare i parametri e gli algoritmi, valutare i dati d'archivio e molto altro.
- Programmable logic controller (PLC): il PLC è uno dei controllori presenti in un ICS. Consente di gestire i processi locali o di collegarsi a una HMI. Un altro tipo di controllori programmabili sono i controllori di automazione programmabili (PAC), simili ai PLC, ma che spesso sono più avanzati e offrono più memoria e maggiore flessibilità nella programmazione, nonché funzionalità aggiuntive.
- Soft PLC: i PLC possono essere presenti anche in banche dati centrali, alimentate dai dati del processo di produzione. zenon Logic, per esempio, offre un ambiente PLC integrato a cui gli ingegneri hanno accesso tramite una banca dati condivisa. In questo modo basta che creino gli oggetti una volta per potervi accedere ripetutamente nel sistema.
- Server di controllo:questo server ospita il software di controllo della supervisione per un PLC o un distributed control system (DCS). Può comunicare inoltre anche con i dispositivi di controllo a livelli inferiori.
- Tecnologie operative e informatiche: dispositivi diversi, come ad esempio i sensori, monitorano le operazioni sul campo.
- Circuito di controllo: un circuito di controllo dispone di vari tipi di hardware, come PLC, attuatori che interpretano i segnali dei sensori, interruttori, valvole di controllo ecc. In seguito, le informazioni vengono inviate a un controllore per eseguire una determinata attività.
- Sistema di manutenzione remota: questo sistema è in grado di rilevare anomalie o guasti, e se possibile, di eseguire azioni preventive.
- Master terminal unit (MTU, unità terminale master) o server SCADA: la MTU o il server supervisory control and data acquisition (SCADA) può impartire i comandi alle RTU sul campo.
- Dispositivi elettronici intelligenti: un dispositivo intelligente è in grado di raccogliere dati e comunicare con altri dispositivi. Con le infrastrutture SCADA e DCS, questi dispositivi possono eseguire automaticamente controlli a livello locale.
- Server di archiviazione dei dati: i dati raccolti dall’ICS e dal suo ambiente operativo vengono memorizzati in un server di archiviazione dati ed esportati in un altro sistema informatico, in cui potranno essere analizzati ulteriormente e utilizzati per elaborare strategie.
I vantaggi di un sistema di controllo di processo industriale
L’automazione industriale tramite ICS offre alle organizzazioni industriali una serie di vantaggi. I benefici del sistema di controllo di processo includono:
-
grazie a una minore esigenza di interventi manuali e a una maggiore produttività, un ICS aumenta l’efficienza delle operazioni. Le operazioni manuali e l’uso di energia possono essere ridotti. Il funzionamento 24 ore su 24 e 7 giorni su 7 di un ICS rappresenta un ottimo modo per usufruire di un’automazione continua o usare i tempi morti per elaborare e analizzare le informazioni, sfruttando meglio le vostre ore di esercizio.
-
la riduzione dei costi amplia il margine di profitto. Aumentando e migliorando gli output, è possibile ampliare i propri margini di profitto, semplificare i requisiti per il personale e ridurre il prezzo delle operazioni.
-
i processi ottimizzati da un ICS contribuiscono a ridurre le risorse necessarie per la creazione di prodotti e a raggiungere una gestione più efficiente. Se si riduce la quantità di rifiuti, non occorrerà spendere così tanto tempo per differenziarli o per acquistare i materiali da cui vengono generati. Inoltre, se il numero di errori è minore, è inferiore anche lo sforzo richiesto per risolvere i problemi o contenere i danni quando i problemi raggiungono il cliente.
-
un ICS contribuisce a migliorare la qualità del prodotto in molti modi. Può monitorare la qualità o adattare i processi in base alle esigenze. L’automazione dei processi industriali può inoltre ridurre al minimo la possibilità di errore umano, e fornire informazioni preziose sui prodotti tramite le analisi. Grazie alle molteplici funzionalità di un ICS, è possibile migliorare notevolmente la qualità dei propri prodotti e godere di maggiore soddisfazione, costi inferiori e benefici sulla reputazione.
-
indipendentemente dall’avere o meno un ICS a disposizione, il dato di fatto è che la vostra struttura industriale deve gestire moltissimi dati. Un ICS può raccoglierli e organizzarli tutti e fungere da luogo centrale in cui sia possibile analizzarli e controllarli. Inoltre, un ICS collega tutti i sistemi, i sensori e i componenti della struttura per consentirvi di visualizzarli e controllarli dall’alto.
Nei contesti industriali, l’automazione vanta un potenziale significativo e sempre più aziende si avvalgono di essa per continuare a essere competitive. Si prevede che il mercato, nel suo complesso, entro il 2028 registrerà un incremento del tasso di crescita annuale composto pari all’8,9%, raggiungendo 288,93 miliardi di dollari.
Quali tipi di sistemi di controllo di processo industriale esistono?
Esistono vari tipi di sistemi di controllo di processo industriale, ideati per i diversi ambienti di applicazione. Di seguito riportiamo i diversi tipi di sistemi di controllo di processo disponibili.
SCADA
Un sistema supervisory control and data acquisition (SCADA) raccoglie i dati e controlla gli impianti in diverse sedi. Il controllo avviene al livello della supervisione, con PLC, RTU e moduli distribuiti in viarie sedi per raccogliere e trasmettere i dati anche a lunghe distanze. Possono essere collegati a macchinari, sensori o altri tipi di impianti. Le HMI integrate inviano i dati e gli utenti visualizzano le informazioni in arrivo. Tale processo può avvenire in loco o presso un’altra sede, e può comprendere innumerevoli input e output.
I sistemi SCADA possono essere semplici o complessi e sono molto utilizzati in settori che comprendono gli impianti di gestione delle acque e delle acque reflue, la trasmissione e la distribuzione dell’energia, il Food & Beverage, il settore farmaceutico e quello automotive. Un sistema SCADA si basa principalmente su una solida piattaforma HMI con un’interfaccia intuitiva e vaste funzionalità che facilitano la raccolta dei dati, la visibilità e l’efficienza.
DCS
Un Distributed Control System è un sistema che viene utilizzato presso una sede e opera con i setpoint, ovvero i valori impostabili per una determinata variabile o per un determinato processo. Questo sistema invia un setpoint a un controller in grado di muovere componenti come valvole e attuatori per garantire il mantenimento del setpoint desiderato. Un DSC usa un circuito di controllo della supervisione per gestire i dispositivi come parte del processo generale di produzione. Un DCS controlla, monitora e organizza i vari controller utilizzati in tutto lo stabilimento.
Un DCS consente agli utenti di accedere rapidamente ai dati necessari. Dal momento che molti dispositivi sono collegati a esso, tale sistema riduce al minimo l’impatto di un eventuale guasto su tutto il sistema ICS. Molte aziende nel settore manifatturiero, di produzione e distribuzione dell’energia, idriche e di gestione delle acque reflue scelgono questo tipo di soluzione.
PLC
Sebbene i controllori a logica programmabile siano una parte essenziale di entrambi i metodi summenzionati, tecnicamente, sono in grado di funzionare in totale autonomia. I PLC raccolgono le informazioni da un input ed elaborano i dati, inizializzando gli output in base ai parametri dati. Possono essere a loro volta semplici o complessi.
Molti PLC presentano componenti integrati, ma possono anche essere utilizzati con un approccio modulare collegandoli a dispositivi quali sensori, contatori, luci, relè e valvole. Altri componenti che possono essere impiegati con un approccio integrato o modulare includono l’alimentazione elettrica, le porte e i protocolli per la comunicazione con un sistema SCADA o HMI.
I PLC sono diffusi nei settori manifatturiero, compresa la produzione batch, e della distribuzione. Possono essere utilizzati in una o più sedi. Il principale svantaggio dell’utilizzo dei PLC senza un sistema di tipo DCS o SCADA associato è costituito dalla mancanza di visibilità e controllo a livello centrale. I PLC operano a livello locale e, se usati da soli, non comunicano con altri sistemi. Pertanto, un approccio solo PLC potrebbe non essere la soluzione vincente per un’azienda in crescita. I PLC restano tuttavia componenti vitali di un ICS, poiché garantiscono il funzionamento di questi sistemi.
Come si configura e usa un sistema di controllo di processo industriale?
Creando i progetti in un ICS si può godere di una maggiore efficienza e un maggiore controllo in futuro, poiché il progetto viene ingegnerizzato con l’ICS e considerando la sua struttura. Inoltre, un ICS vanta funzionalità che agevolano la pianificazione e lo sviluppo del progetto. Scoprite nel dettaglio il processo con la piattaforma software zenon e in che modo questa vi consente di creare progetti con efficienza. Le fasi di progettazione di zenon includono:
1. Concezione
La prima fase consiste nel riuscire a bilanciare tutte le esigenze complesse proprie di un progetto di ingegneria, dagli standard di qualità, agli ostacoli economici e alle questioni di efficienza. Un requisito è una rapida prova di progetto che dimostra se un concetto pensato sia realmente fattibile. Questo processo può includere esperimenti, realizzazione di progetti pilota e test. Gli ingegneri devono anche considerare i requisiti di conformità esterna e di compatibilità.
zenon vi aiuta fornendo una generazione di dati rapida e intuitiva per i veloci test iniziali, comprendendo anche una serie di configurazioni e metodi di parametrizzazione standard. Soddisfa i requisiti di conformità di DNP3, IEC 61850, IEC 60870 e altri standard. zenon inoltre dispone di modelli di componenti e campioni per aiutarvi ad avviare e sviluppare le vostre soluzioni di prova.
2. Sviluppo della soluzione
Durante la fase di sviluppo e implementazione della soluzione, l’efficienza acquisisce sempre più importanza. Simboli, modelli e un orientamento agli oggetti possono aiutarvi a creare più rapidamente la vostra soluzione per il settore dell’energia. I modelli vi fanno risparmiare tempo grazie al riutilizzo dei componenti e alle tempistiche di apprendimento ridotte. Inoltre, contribuiscono a mantenere il progetto in ordine e ben organizzato, consentendo la verifica singola e riducendo il tempo dedicato ai test.
Altre funzioni utili includono gli strumenti di automazione e la configurazione per le funzioni esistenti. Per fare in modo che questa fase sia semplice e lineare, zenon offre funzioni quali:
- Modelli di schermate e simboli: zenon consente una visualizzazione semplice con layout diversi per le varie attività, tra cui le liste di tipo Lista Eventi Cronologica (CEL), la gestione della sequenza di commutazione e l’elaborazione dei comandi. Potete usare simboli d’immagine generici e assegnare variabili dinamiche e funzioni. Successivamente, il simbolo può essere usato in vari punti dell’applicazione HMI, mentre l’implementazione originale del simbolo resta centrata in un unico punto.
- Smart Objects: con gli Smart Objects, zenon vi permette di creare modelli di automazione elaborati. Potete usare simboli grafici, variabili, tipi di dati, driver, gruppi di comando, schermate dettagliate e interblocchi per pre-configurare un modello di dati e allegare avvisi e viste al modello.
- Meccanismi di import/export e default: utilizzate robusti meccanismi di import/export e default per aumentare l’efficienza e ottenere un ambiente di modelli con varie capacità.
- Configurazione e parametrizzazione: queste funzioni riducono la complessità consentendovi di impostare i parametri essenziali e facendo in modo che il resto della soluzione si configuri correttamente. Non occorre sviluppare o modificare codice personalizzato o ricorrere a elevate competenze di programmazione. Queste risorse possono ridurre gli errori di un codice personalizzato e memorizzare parametri standardizzati da trasferire facilmente durante lo sviluppo della soluzione.
- Automazione: la progettazione automatica consente di risparmiare tempo offrendo una semplice pianificazione della visualizzazione. Con l’ingegneria orientata agli oggetti di zenon, ad esempio, potete creare variabili e procedure guidate personalizzate per eseguire attività standardizzate e ripetitive. Una tale capacità vi consente di ridurre al minimo l’errore umano, di standardizzare e aumentare l’efficienza.
3. Messa in funzione
Nella fase di messa in funzione, vi occorre sapere che la vostra soluzione è rapidamente scalabile per applicazioni grandi effettuando tutte le verifiche necessarie. La standardizzazione di zenon contribuisce a ciò con funzioni come modelli, building block e strumenti di progettazione automatica per algoritmi personalizzati e procedure guidate di configurazione. Durante i test, potete vedere i collegamenti di comunicazione e gli stati all’interno di zenon e utilizzare i modelli di processo per evitare di svolgere i test due volte.
Un altro prezioso elemento della fase di messa in servizio è la simulazione di processo. Essa consente di preparare schermate, controllare gli algoritmi, eseguire i primi test e ottimizzare i progetti. zenon ottimizza la simulazione del processo consentendo il passaggio dei driver alla modalità di simulazione, il mantenimento delle variabili su valori statici o l’animazione dinamica.
4. Estensione e aggiornamenti
L’efficienza in questa fase contribuisce a garantire un funzionamento totalmente automatico in futuro. Una volta terminato un progetto, avrete la possibilità di aggiornare o estendere il contenuto, apportare rapide modifiche al progetto ed estendere l’architettura a seconda delle esigenze. In zenon, l’architettura modulare del progetto vi consente di apportare modifiche ed eseguire aggiornamenti in modo rapido e semplice. La struttura modulare implica la possibilità di aggiungere all’architettura moduli duplicati, specializzati e basati su modelli.
Le funzioni di un solido ICS rendono più possibile la compatibilità a lungo termine, consentendo retrofit, aggiornamenti ed estensioni anche molto tempo dopo la conclusione del progetto.
Implementazione del corretto ICS con zenon
Un ICS è un elemento necessario per gli ambienti industriali, in grado di fornire una chiara visibilità, il controllo e la raccolta dei dati a varie organizzazioni. E proprio per il fatto che è un elemento così vitale, vi serve un ICS progettato da esperti. zenon di COPA-DATA è una potente piattaforma software modulare che valorizza al massimo gli ambienti SCADA e fornisce vantaggi in termini di efficienza, costi, gestione dei dati e non solo.
Noi di COPA-DATA operiamo nel settore dal 1987 e non smettiamo mai di perfezionare la nostra piattaforma per soddisfare le esigenze in continuo cambiamento del settore. Utilizziamo tutta la logica e tutti gli algoritmi necessari per mantenere la vostra azienda attiva. Contattateci subito per ottenere maggiori informazioni su zenon e su quello che può fare per la vostra organizzazione.
Wir freuen uns über Ihre Fragen. Kontaktieren Sie uns einfach, wie es Ihnen am liebsten ist: