SMLC: 보틀링에 대한 풍부한 정보로 스마트한 의사결정 (레바논)
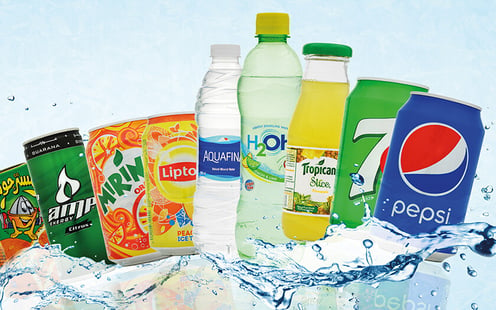
PepsiCo의 파트너사인 SMLC는 레바논 최대 규모의 음료 보틀링 회사로 다양한 유리병, PET 병, 캔, 팩 제품을 생산합니다. 이 회사는 COPA-DATA의 zenon 소프트웨어를 기반으로 하는 라인 관리 시스템을 구축하여 더 이상 데이터의 수동 입력없이 효율적인 보틀링 공정을 위한 포괄적인 정보를 획득합니다.
하이라이트
- SMLC를 위한 보틀링/패키징 라인 관리 시스템으로 zenon 사용
- 중앙집중식 시스템 모니터링
- 수동 데이터 수집 필요성 제거
- 포괄적인 관리 정보
- 빠른 라인 축적 설계 검증
- 높은 시스템 안정성, 낮은 저장소 사용량
- 프로그래밍 없이 새로운 동적 정보 차트의 빠른 생성
1950년대에 가정용 냉장고, 백화점, 슈퍼마켓이 출현하면서 PepsiCo와 같은 음료 제조업체의 시장 원칙에 큰 변화가 생겼습니다. 펩시콜라를 만드는 PepsiCo는 글로벌 소비 시장이 확대되면서 엄청난 성장 기회를 잡을 수 있었습니다. 1952년 PepsiCo는 레바논 베이루트에 소재한 SMLC(Société Moderne Libanaise pour le Commerce)와 협력하기 시작했습니다. 이 회사는 PepsiCo 브랜드의 탄산음료, 아이스티, 스포츠 음료, 주스, 에너지 드링크, 생수를 보틀링하여 배급합니다.
유리병, 블로우 성형 PET 병, 알루미늄 캔, 복합소재 팩을 생산하는 10개의 보틀링 라인을 갖춘 SMLC는 레바논 최대 규모의 음료 보틀링 업체입니다. 수많은 수상 경력을 보유한 이 회사는 최근 PepsiCo International로부터 Performance with Purpose 상을 수상하면서 수자원 및 에너지 소비량 절감을 위한 그동안의 노력을 인정받았습니다.
투명성 결핍
SMLC의 패키징 공정은 지금까지 효율적으로 운영되어 오기는 했지만, 생산 데이터 수집 및 정보 관리에서는 비효율적인 서류 양식 또는 스프레드시트 소프트웨어를 이용한 수동 데이터 기입 과정이 여전히 존재했습니다. 우선 순위가 다른 작업을 가지고 있는 생산 및 유지보수 직원에게 성가신 업무로 여겨지는 단순 기입 작업은 빈번하게 부정확한 보고서 생성을 초래했습니다. 실제 보고할 값이 아니라 원하는 상태가 반영되는 경우도 빈번했습니다.
이런 이유로 SMLC는 품질 및 효율성 제고를 목표로 현대화 이니셔티브에 착수했습니다. 여기에는 조직 재구성, 최첨단 생산 라인에 대한 투자 및 신규 건물 건설이 포함되었습니다. 이러한 혁신의 일환으로 경영진은 모든 패키징 라인을 아우르는 소프트웨어에 투자하기로 결정했습니다. 주목적은 작업 현장에서 최고 경영진까지의 정보 흐름을 개선하여 보다 빠르고 정보 기반의 의사결정을 내리는 것이었습니다. 또한 회사의 CIP(Clean In Place) 공정에 필요한 정보를 제공받기 위한 목적도 포함되었습니다.
부진한 성과를 가져온 초기 시도
SMLC는 보틀링 라인 한 곳을 커버하는 파일럿 설치 작업을 위해 Teknologix와 계약을 체결했습니다. 베이루트 소재 Teknologix의 산업 자동화 전문가팀은 수년간 SMLC를 위해 다양한 자동화 및 레트로피팅 프로젝트의 성공적인 구축을 통해 호평을 받아왔습니다. 고객과 가까이 위치해 유럽 내 공급업체들과 달리 제안서에 시운전 및 사후 지원에 필요한 막대한 출장 비용을 포함할 필요가 없습니다.
전송 및 처리할 데이터의 양을 줄이기 위해 Teknologix는 PLC를 사용하여 각 라인별로 라인의 개별 스테이션에서 데이터를 수집하고 집중화하여 사전 처리하는 시스템 구성을 설계했습니다. Teknologix의 창립자이자 CEO인 Lucien Kazzi는 “저희가 생각한 개념이 옳다는 것을 알았으며 SMLC의 요구사항을 충족하기 위해 많은 노력을 기울였지만, 결과적으로 고객을 만족시키지 못했습니다.”라고 당시를 회상하며, 다음과 같이 그 이유를 설명합니다. “올바른 소프트웨어를 사용하지 않았기 때문입니다.”
유명한 글로벌 자동화 솔루션 공급업체에서 널리 사용되는 공정 시각화 시스템을 받아 수 차례 애드온과 업그레이드로 기능을 강화했지만, 애초에 선택한 소프트웨어 제품으로는 고객의 리포팅 요구사항을 지원할 수 없었습니다. Lucien Kazzi는 다음과 같이 당시 상황을 설명합니다. “시스템 내 정보를 기반으로 간트(Gantt) 다이어그램을 표시하는 스크립트를 프로그래밍하는 데 몇 개월이나 허비해야 했습니다.” “간트 다이어그램 생성에 2분이나 소요되는 등 보고서가 매우 느렸으며, 이 마저도 종종 새로고침에 실패하거나 멈춤 현상을 보였습니다.”
올바른 소프트웨어를 사용하여 정보 문제 해결
수차례 서로 다른 플랫폼을 시도해보았으나 필요한 모든 요건을 충족하는 제품은 없었습니다. 더 나은 솔루션 플랫폼을 검색하던 중, Lucien Kazzi는 보틀링 기술 및 패키징 기계의 선도적인 공급업체가 COPA-DATA의 zenon 소프트웨어를 제어 시스템 전반의 솔루션으로 사용하고 있다는 사실을 알게 되었습니다. “그 업체에 적합한 제품이라면 저희가 찾던 바로 그 제품일 가능성이 있었죠.”라고 생각한 Lucien Kazzi는 COPA-DATA에 연락했습니다.
이는 올바른 결정이었고, 수렁에 빠진 프로젝트를 구제할 수 있었습니다. zenon의 기능은 즉시 사용 가능하며, 프로그래밍없이 완전히 사용자 친화적인 그래픽 인터페이스에서 구성을 설정하는 것만으로 프로젝트를 생성할 수 있습니다. Lucien Kazzi는 zenon은 다른 시스템을 구축하는 것보다 훨씬 쉬웠을 뿐만 아니라, 예상보다도 훨씬 쉬웠다고 말합니다. Teknologix는 첫 zenon 교육을 받은 후 단 몇 주 만에 SMLC를 위한 첫 번째 라인 관리 시스템 프로젝트를 성공적으로 완료했습니다. Lucien Kazzi는 “매우 유연하고 동적인 zenon의 리포팅 도구는 정말 큰 도움이 되었습니다. 파이 차트와 파레토(Pareto) 다이어그램을 사용하여 인스턴스 품질 보고서, 성능 분석, 근본 원인 분석 보고서를 쉽게 생성할 수 있습니다.”라고 하면서 다음과 같이 이야기를 마쳤습니다. “COPA-DATA의 탁월한 사후 지원 품질과 빠른 응대도 성공의 핵심 요인으로 꼽을 수 있습니다.”
포괄적인 솔루션
Teknologix는 zenon을 사용하여 단기간에 포괄적인 데이터 수집 및 라인 관리 솔루션을 구축했습니다. 이 회사의 자동화 전문가들은 이 경험을 토대로 템플릿을 만들고, 추가로 네 개의 라인을 빠르게 이어 구축했습니다. 현재 zenon 기반의 시스템은 재활용 병 라인 한 곳, PET 병 라인 두 곳, 캔 라인 두 곳, 이렇게 다섯 개의 음료 생산 라인에 적용되어 있습니다.
zenon의 매우 광범위한 통신 드라이버를 통해 다른 PLC를 사용하는 다양한 제조업체의 기계와 통신할 수 있습니다. 표준 PLC 블록을 생성하면 구형 장비와도 통합할 수 있습니다. zenon 소프트웨어의 최적화된 데이터베이스 구조는 데이터 저장소 사용량을 줄이고 보고서 로딩 시간도 단축해줍니다. 기존 시스템에서는 보틀링 라인 한 곳당 데이터가 월 500GB에 달했지만, zenon 기반 솔루션에서는 일 년 내내 10GB면 충분합니다. 기존에 2분씩 소요되던 Gantt 보기 다이어그램 생성을 이제 2초만에 생성할 수 있으며, 시스템 충돌 문제도 발생하지않습니다.
zenon을 구축하면 동적 리포팅 기능을 사용할 수 있습니다. 기존 시스템 아키텍처에서는 정적인 시간 프레임에 대해서만 표시할 수 있었지만, zenon의 Extended Trend 모듈에서는 손쉽게 병합해 비교할 수 있고, 실시간으로 모니터링하며 실시간 추세를 표시할 수도 있습니다. 기존 소프트웨어로는 Teknologix가 프로그래밍하는 데 2개월 이상 소요되던 간트 다이어그램을 zenon의 Extended Trend 모듈을 통해 단 한 시간 만에 구성할 수 있습니다.
현명한 의사결정을 위한 견고한 토대
Teknologix가 구축한 zenon 기반 솔루션은 기존에 사용하던 시스템의 단점을 극복하고, 예측 분석과 같은 향후 확장을 고려 중인 고객의 요구사항을 충족합니다.
-
zenon 기반 관리 시스템은 수동 입력을 최소화하고, 품질 보고서, 성능 분석, 근본 원인 분석, 시간 손실 범주 보고서 등 다양한 동적 보고 관리 기능을 제공합니다. 이 시스템은 생산 과정에 대한 완전한 투명성을 제공하며, 라인 축적 설계 검증과 같은 견고한 기초를 통해 현명한 의사 결정을 위한 충분한 정보를 제공합니다.
Shady Khoury | SMLC의 운영 디렉터
Download
-
성공 사례SMLC_PepsiCo_SUS_KR.pdf
Wir freuen uns über Ihre Fragen. Kontaktieren Sie uns einfach, wie es Ihnen am liebsten ist: