Sistemas de controle industrial
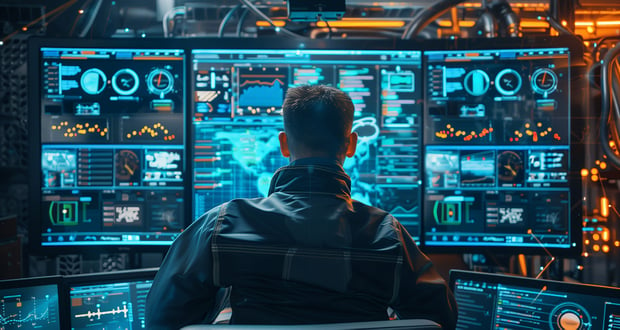
Um sistema de controle industrial (ICS) é uma parte fundamental de muitas organizações, fornecendo controles automatizados para uma ampla gama de componentes em vários locais. Existem diferentes tipos de ICSs, que podem dar suporte a uma enorme quantidade de elementos em diversas operações, de energia até fabricação e farmacêutica. Eles proporcionam benefícios para eficiência, qualidade, análise e, é claro, seus resultados financeiros.
Vamos ver os ICSs em mais detalhes e o que eles podem fazer pelas operações industriais.
O que é um sistema de controle industrial?
Os sistemas de controle industrial lidam com vários componentes, como dispositivos de monitoramento e sistemas de software, para gerenciar operações e automatizá-las quando possível. Eles equilibram os muitos componentes necessários para operar um ambiente industrial, garantindo que esses componentes funcionem de modo eficiente e em sincronia entre si. Um ICS pode assumir o controle por completo ou fazer parte de uma abordagem híbrida que incorpore interação humana. Circuito aberto, circuito fechado e opções manuais estão disponíveis.
Se a sua organização industrial envolve a Internet das Coisas Industrial (IIoT) ou outros sistemas inteligentes, um ICS é especialmente útil e minimiza os riscos de segurança. No geral, os ICSs dão maior visibilidade e controle fácil de uma complexa rede de componentes. Alguns elementos que você pode encontrar dentro de um ICS incluem servidores e controladores como:
- Unidade de terminal remoto (RTU): uma RTU é um dispositivo de campo que se comunica com uma unidade de terminal mestre e funciona como um controlador supervisório.
- Interface homem-máquina (HMI): com uma HMI, os humanos podem interagir com o hardware que controla a máquina. A HMI costuma assumir a forma de uma interface gráfica do usuário (GUI) que cria uma plataforma legível por humanos, em essência, software. Os usuários podem visualizar os status atuais, monitorar pontos de ajuste, receber alertas de segurança, ajustar parâmetros e algoritmos, avaliar dados históricos e muito mais.
- Controlador lógico programável (PLC): como um dos controladores de um ICS, um PLC permite o gerenciamento de processo local ou a conexão a uma HMI. Você também pode ver controladores de automação programáveis (PACs), que são similares a PLCs, mas costumam ser mais avançados e podem incluir mais memória e flexibilidade de programação, além de outros recursos.
- Soft PLCs: PLCs também podem ser encontrados em um banco de dados centralizado, alimentado por dados da linha de produção. A lógica do zenon, por exemplo, oferece um ambiente de PLC integrado que os engenheiros podem acessar por meio de um banco de dados compartilhado. Eles precisam apenas criar os objetos uma vez e então podem acessá-los repetidamente no sistema.
- Servidor de controle: esse servidor hospeda software de controle supervisório para um PLC ou sistema de controle distribuído (DCS). Também pode se comunicar com dispositivos de controle de nível inferior.
- TI e técnico operacional: diferentes dispositivos, como operações em campo do monitor de sensore.
- Circuito de controle: um circuito de controle tem diferentes tipos de hardware, como PLCs e atuadores que interpretam sinais de sensor, comutadores, disjuntores, válvulas de controle e muito mais. Eles então enviam essas informações para um controlador para realizar uma dada tarefa.
- Sistema de manutenção remoto: esse sistema pode monitorar e detectar anomalias ou falhas, possivelmente agindo para prevenir problema.
- Unidade de terminal mestre (MTU) ou servidor SCADA: a MTU ou o servidor controle de supervisão e aquisição de dados (SCADA) pode entregar comandos a RTUs em campo.
- Dispositivos eletrônicos inteligentes: um dispositivo inteligente pode coletar dados e comunicar-se com outros dispositivos. Com infraestruturas SCADA e DCS, esses dispositivos podem executar controles locais automaticamente.
- Historiador de dados: dados coletados do ICS e seu ambiente operacional são armazenados em um historiador de dados e exportados para outro sistema de informações. Lá, eles podem ser processados para mais análise e para traçar a estratégia.
Os benefícios de um sistema de controle industrial
A automação industrial por meio de um ICS tem muitas vantagens para organizações industriais. Alguns benefícios do sistema de controle industrial incluem:
-
com menos exigências manuais e mais produtividade, um ICS ajuda você a aumentar a eficiência. Você pode reduzir as operações manuais e o uso de energia. A funcionalidade ininterrupta de um ICS é um ótimo modo de desfrutar de automação a qualquer hora ou usar tempo de inatividade para análise e processamento mais profundos das informações, aproveitando melhor suas horas de operação.
-
reduzir seus custos ajuda muito a aumentar os lucros. Conforme você aumenta e aprimora sua produção, pode aumentar suas margens de lucro, simplificar os requisitos de alocação de pessoal e reduzir o preço das operações.
-
os processos otimizados que vem de um ICS ajudam a minimizar os recursos necessários para criar produtos e contribuir para um gerenciamento mais eficiente. Com menos desperdício, você não precisa gastar tanto tempo detectando nem comprando os materiais que geram o desperdício. Menos erros também reduzem os esforços necessários para corrigir os problemas ou controlar os danos após os problemas chegarem a um cliente.
-
um ICS contribui para a qualidade do produto de muitas maneiras. Ele pode monitorar a qualidade ou ajustar os processos conforme necessário. A automação de processo industrial pode minimizar o erro humano também, além de dar suporte a insights valiosos por meio de análise. Com todos os recursos de um ICS, você pode aumentar muito a qualidade e aproveitar a melhoria da satisfação e das economias de custo, além das vantagens para a reputação associadas.
-
tenha você um ICS ou não, muitos dados passam pela sua instalação industrial. Um ICS pode coletar e organizar todos os dados e criar um local centralizado para análise e controle fáceis. Ele também se conecta a todos os sistemas, sensores e componentes da instalação para visibilidade e controle de cima para baixo..
Nas configurações industriais, a automação tem um potencial significativo e mais empresas as estão aproveitando para se manterem competitivas. O mercado como um todo deve aumentar a uma taxa de crescimento anual composta de 8,9%, alcançando US$ 288,93 bilhões até 2028.
Quais são os tipos de sistemas de controle industrial?
Existem diversos tipos de sistemas de controle industrial feitos para diferentes ambientes. A seguir estão os tipos de sistemas de controle industrial disponíveis.
SCADA
Um sistema de controle de supervisão e aquisição de dados (SCADA) coleta dados e controla equipamentos em vários locais. O controle acontece no nível de supervisão, com PLCs, RTUs e módulos distribuídos em diferentes locais para coletar e transmitir dados em longa distância. Eles podem estar vinculados a máquinas, sensores ou outros tipos de equipamentos. HMIs integradas enviam os dados e os humanos supervisionam as informações recebidas. Esse processo pode ocorrer no local ou externamente e incluir várias entradas e saídas.
Os sistemas SCADA podem variar de simples a complexos e são populares em setores como água e esgoto, transmissão e distribuição de energia, alimentos e bebidas, farmacêutico e automotivo. Um sistema SCADA conta fortemente com uma plataforma de HMI robusta para aproveitar uma interface fácil de usar e amplos recursos que facilitam a coleta de dados, a visibilidade e a eficiência.
DCS
Um sistema de controle distribuído é usado em um local e funciona com pontos de ajuste, que são os valores alvo para uma variável ou processo. Esse sistema envia um ponto de ajuste para um controlar que pode mover componentes como válvulas e atuadores para manter o ponto de ajuste desejado. Um DCS usa um circuito de controle de supervisão centralizado para gerenciar os dispositivos como parte de um processo de produção geral. Um DCS controla, monitora e organiza os muitos controladores usados em toda uma fábrica.
Um DCS permite que os usuários acessem rapidamente os dados necessários. Já que muitos dispositivos se conectam a ele, isso também minimiza o impacto que uma falha pode ter sobre o sistema ICS geral. É uma escolha popular para empresas nos setores de fabricação, refino de petróleo, produção de energia e distribuição de água e esgoto.
PLC
Embora os controladores lógicos programáveis sejam uma parte essencial de ambos os métodos acima, eles tecnicamente podem funcionar sozinhos. Os PLCs coletam informações de uma entrada e processam os dados, iniciando saídas com base nos parâmetros informados. Eles podem, novamente, variar de simples a complexos.
Muitos PLCs têm componentes integrados, mas também podem adotar uma abordagem granular para conectarem-se a dispositivos como sensores, medidores, luzes, relés e válvulas. Outros componentes que podem ser integrados ou serem modulares incluem o abastecimento de energia e portas e protocolos para comunicação com um sistema SCADA ou HMI.
Os PLCs são comuns em setores como distribuição e fabricação, incluindo fabricação em lote. Eles podem ser usados em um ou vários locais. A principal desvantagem de usar PLCs sem um sistema associado como DCS ou SCADA é a falta de visibilidade e controle centralizados. Os PLCs funcionam localmente e, por conta própria, não se comunicam com outros sistemas. Quanto maior uma empresa se torna, menos viável uma abordagem apenas de PLC será. Ainda ainda, eles são um componente vital de um ICS, fornecendo a maior funcionalidade desses sistemas.
Como um sistema de controle industrial é configurado e usado?
Iniciar projetos em um ICS proporciona mais controle e eficiência no futuro, pois o projeto é elaborado com o ICS e pensando na sua estrutura. Um ICS tem recursos que ajudam no planejamento e no desenvolvimento de projeto também. Acompanhe o processo com a plataforma de software zenon e veja como ele habilita práticas de engenharia eficientes. As fases de engenharia do zenon incluem:
1. Concepção
O primeiro estágio é para equilibrar todas as complexidades envolvidas em um projeto de engenharia, dos padrões de qualidade às barreiras de custo e preocupações sobre eficiência. Um requisito é uma rápida prova de conceito, que mostra que um conceito de design é viável. Esse processo pode incluir experimentos, projetos piloto e teste. Os engenheiros também precisam considerar os requisitos de conformidade e compatibilidade externos.
O zenon ajuda fornecendo uma geração de dados rápida e fácil para teste inicial ágil, além de uma variedade de métodos de parametrização e configuração padrão. Ele cumpre os requisitos de conformidade para DNP3, IEC 61850, IEC 60870 e outros. O zenon também tem componentes de modelo e amostras para ajudar você a começar a desenvolver suas soluções de amostra.
2. Desenvolvimento de solução
Conforme você desenvolve e implementa sua solução, a eficiência começa a ganhar importância. Símbolos, modelos e orientação a objeto podem ajudar você a criar sua solução de energia mais rapidamente. Os modelos permitem que você poupe tempo reutilizando componentes e minimizando o tempo de aprendizado. Eles também tornam mais fácil manter o projeto limpo e organizado enquanto permitem a verificação única e minimizam o tempo de teste.
Outros recursos valiosos incluem ferramentas de automação e configuração para funções existentes. Para tornar esse estágio tranquilo e simples, o zenon oferece recursos como:
- Modelos e símbolos na tela: o zenon permite a fácil visualização com diferentes layouts para diferentes tarefas, incluindo listas de sequência de eventos (SoE), gerenciamento de sequência de comutação e processamento de comando. Você pode usar símbolos de tela genéricos e atribuir variáveis e funções dinâmicas. Então, o símbolo pode ser usado em vários ativos na HMI enquanto a implementação do símbolo original fica centralizada em um ponto.
- Objetos inteligentes: com objetos inteligentes, o zenon possibilita a modelos de automação elaborados. Você pode usar símbolos gráficos, variáveis, tipos de dados, acionadores, grupos de comando, telas detalhadas e intertravamentos para pré-configurar um modelo de dados e anexar alarmes, funções e visualizações ao modelo.
- Importar/exportar mecanismos e padrões: utilize mecanismos robustos de importação/exportação e padrões praticáveis para maior eficiência e um ambiente de modelo de maior capacidade.
- Configuração e definição de parâmetros: esses recursos reduzem a complexidade permitindo que você defina seus parâmetros essenciais e ajudam o restante da solução a ficar no lugar certo. Não é preciso desenvolver nem realizar engenharia reversa de código personalizado nem usar habilidades de programação altamente avançadas. Esses recursos podem reduzir erros de codificação personalizada e reter parâmetros padronizados para transferências fáceis enquanto você desenvolve a solução.
- Automação: engenharia automatizada pode poupar tempo oferecendo fácil planejamento de visualização. Com a engenharia orientada ao objeto do zenon, por exemplo, você pode criar variáveis e assistentes personalizados para realizar tarefas padronizadas repetitivas. Essa habilidade permite que você minimize o erro humano, padronize e aumente a eficiência.
3. Comissionamento
Na faze de comissionamento, você precisa saber que sua solução pode se expandir rapidamente para aplicações grandes com todas as verificações corretas em vigor. A padronização do zenon ajuda nessa área com recursos como modelos, blocos de construção e ferramentas automatizadas para algoritmos personalizados e assistentes de configuração. No que se refere a teste, você pode ver links de comunicação e status no zenon e utilizar modelos de processo para evitar testes duplicados.
Outro componente valioso do comissionamento é a simulação de processo. Isso ajuda você a preparar telas, realizar primeiros testes, controlar algoritmos e otimizar designs. O zenon otimiza o estímulo de processo alternando os acionadores para o modo de simulação, mantendo as variáveis em valores estáticos ou animando variáveis de modo dinâmico.
4. Extensão e atualizações
A eficiência nessa fase ajuda a garantir a operação autônoma no futuro, Depois de concluir um projeto, é bom poder atualizar ou estender o conteúdo, fazer alterações ágeis ao projeto e estender a arquitetura conforme o necessário. No zenon, a arquitetura de projeto modular permite que você faça alterações e realize atualizações de modo rápido e fácil sem afetar módulos independentes. Com o design modular, é possível também adicionar a arquitetura conforme necessário com módulos duplicados, especializados e com modelos predefinidos.
Os recursos de um ICS forte tornam fácil alcançar compatibilidade de longo prazo, possibilitando aprimoramentos, atualizações e extensões muito tempo depois de o projeto ter sido concluído.
Como implementar o ICS certo com o zenon
Um ICS é uma necessidade para ambientes industriais, levando visibilidade clara, controle e coleta de dados para várias organizações. Como um ICS é uma parte tão importante do quebra-cabeças, você precisa de um que seja criado pelos especialistas. O zenon da COPA-DATA é uma potente plataforma de software modular que aproveita ao máximo os ambientes SCADA e proporciona os benefícios para eficiência, custos, gerenciamento de dados e muito mais.
Aqui na COPA-DATA, estamos no ramo desde 1987 e estamos aprimorando continuamente nossa plataforma para atender às necessidades em constante evolução do setor. Nós utilizamos toda a lógica e todos os algoritmos necessários para manter o progresso do seu negócio. Entre em contato conosco hoje mesmo para saber mais sobre o zenon e o que a plataforma pode fazer pela sua organização.
Wir freuen uns über Ihre Fragen. Kontaktieren Sie uns einfach, wie es Ihnen am liebsten ist: